MIT's Modular Robotic Chain Is Whatever You Want It to Be
Evan Ackerman for IEEE Spectrum: As sensors, computers, actuators, and batteries decrease in size and increase in efficiency, it becomes possible to make robots much smaller without sacrificing a whole lot of capability. There’s a lower limit on usefulness, however, if you’re making a robot that needs to interact with humans or human-scale objects. You can continue to leverage shrinking components if you make robots that are modular: in other words, big robots that are made up of lots of little robots.
In some ways, it’s more complicated to do this, because if one robot is complicated, robots tend to be complicated. If you can get all of the communication and coordination figured out, though, a modular system offers tons of advantages: robots that come in any size you want, any configuration you want, and that are exceptionally easy to repair and reconfigure on the fly.
MIT’s ChainFORM is an interesting take on this idea: it’s an evolution of last year’s LineFORM multifunctional snake robot that introduces modularity to the system, letting you tear of a strip of exactly how much robot you need, and then reconfigure it to do all kinds of things. Cont'd...
Comments (0)
This post does not have any comments. Be the first to leave a comment below.
Featured Product
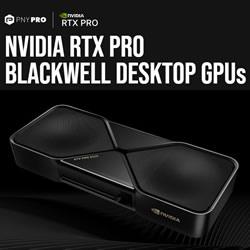