How many robots does it take to change a light bulb?
Tim Sandle for Digital Journal: A newly created robotic gripper has researchers at University of California - San Diego excited. The 'friendly' new robot could help advance the automation of construction and building works.
Engineers at the university have created a gripper-style robot that is capable of picking up and manipulate objects without needing to see them and without needing to be trained. One of the demonstrations of the capability of the robot involved removing and replacing a light bulb.
Twist it, sense it, model it
According to a research note the robotic gripper is different to any seen before. This is based on the combination of three different capabilities. These are: the robot can twist objects; the robot can sense objects; and the robot can build models of the objects it is manipulating. This functionality also allows the gripper to operate in low light and low visibility conditions. The aim was to mimic how a person might operate in low-light conditions.
Development of the robot was led by Dr. Michael T. Tolley. The gripper was fully tested on an industrial Fetch Robotics robot and the combination demonstrated that the machine was able to pick up, manipulate and model a wide range of objects, from light bulbs to other tools like screwdrivers. Full Article:
Comments (0)
This post does not have any comments. Be the first to leave a comment below.
Featured Product
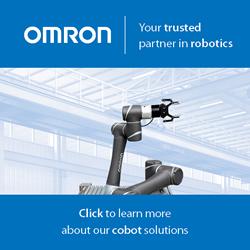