Ocado's collaborative robot is getting closer to factory work
Matt Burgess for Wired: Retailer Ocado is getting closer to creating an autonomous humanoid robot that can help engineers fix mechanical faults in its factories. The firm's latest robot, ARMAR-6, has a human-looking torso, arms with eight degrees of freedom, hands that can grip and a head with cameras inside. But it doesn't have legs and is equipped with a large wheeled base that lets it move around.
"The ambition is that the robot will be able to decide what the technician's intentions are and chip-in as appropriate at the right point in time," says Graham Deacon, the robotics research team leader at Ocado Technology. The robot isn't designed to replace human workers but work alongside them inside within the company's automated warehouses.
To this end, ARMAR-6 uses a three camera systems inside its head to help it detect and recognise humans and objects; speech recognition helps it understand commands; and its hands are able to pick-up and grasp objects.
At present, the robot is still a prototype but getting to this point has taken two and a half years. Four European universities have been working to create each of the systems, under the EU's Horizon2020 project. Full Article:
Comments (0)
This post does not have any comments. Be the first to leave a comment below.
Featured Product
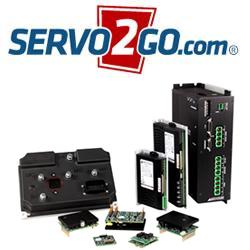