Hyundai Motor Group Develops Wearable Vest Exoskeleton to Alleviate Burden in Overhead Work
Hyundai Motor Group has developed new Vest EXoskeleton (VEX), a wearable robot created to assist industrial workers who spend long hours working in overhead environments.
The VEX enhances productivity and reduces fatigue of industrial workers by imitating the movement of human joints to boost load support and mobility. The wearable vest the polycentric axis – combining multiple pivot points with multi-link muscular assistance – to function, eliminating the need for a battery.
At 2.5kg, VEX weighs 22-42% less than competing products and is worn like a backpack. The user places their arms through the shoulder straps of the vest, then fastens the chest and waist buckles. The back section can adjust in length by up to 18 cm to fit a variety of body sizes, while the degree of force assistance can be adjusted over six levels – up to as much as 5.5 kgf.
"VEX gives workers greater load support, mobility, and adaptability when operating in overhead environments," stated DongJin Hyun, head of Robotics team of Hyundai Motor Group. "Workers will also appreciate how light VEX is to wear and work with."
The newly-developed VEX is targeted at production-line workers whose job is primarily overhead, such as those bolting the underside of vehicles, fitting brake tubes, and attaching exhausts. The development of the VEX included a pilot program in two Hyundai Motor Group plants in the US. The trial was widely successful in assisting workers and boosting productivity and both plants incorporated VEX systems in their production lines.
The Group is considering on implementing the VEX on plants around the world. It is expected to go into commercial production in December by Hyundai Rotem and is projected to cost as much as 30% lower than existing products which usually costs around 5,000 dollars.
Comments (0)
This post does not have any comments. Be the first to leave a comment below.
Featured Product
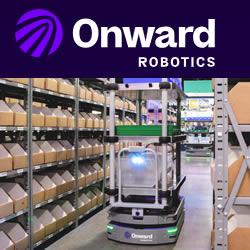