Advanced Robotic Systems in the Automobile Industry
Robots are no strangers to the automobile manufacturing industry, given that it is one of the most highly automated supply chains in the world. Ever since General Motors pioneered the use of robotic systems in car manufacturing back in 1961, the remit of deploying industrial robots has veritably expanded over the years. The latest advanced robotic applications in the sector- for tasks beyond welding and painting- are bringing in a seamless interaction between humans, AI, and robots. Human workers, augmented by robots are accomplishing complex labor-intensive and strenuous tasks with increased precision and flexibility, and therefore, lowering the risks of automation. LinePar explores the integration of sophisticated robotic systems equipped with newer iterations like collaborative robots, AGVs, robotic vision, exoskeletons, etc., that are radically changing the ways of automotive manufacturing.
COBOTS
According to Dan Grieshaber, global director of manufacturing engineering integration at General Motors, Collaborative Robots (or COBOTS) have become a “fundamental game-changer” in the automotive industry. The word “collaborative” describes robots that can operate safely alongside their human counterparts. Thanks to installed sensors, Cobots can react to human contact and monitor the location of humans on the factory floor. The robot automatically shuts down when anybody gets too close to the machinery. Consequently, the robot can be safely used as an assistant alongside human workers on the same assembly line leading to efficient automation of mundane tasks. The strength, force, and speed of Cobots are calibrated to avoid injury. Moreover, Cobots require little to no programming as they can learn through simulation and don’t need to be constantly supervised by highly-skilled technicians. They are smaller and more dexterous, unlike the large, hulking industrial robots of a decade ago.
Robotic Vision
A robot with “eyes” can perform tasks with greater accuracy if it can “see” what it’s doing. That is exactly what Robotics 2.0 is all about- robots being able to handle greater levels of variance through 2D and 3D perception. Driving this major advancement is a library of programming functions called OpenCV (Open Source Computer Vision), which offers free software libraries for computer vision development through real-time image processing. The software algorithm modules coupled with hardware (the camera and laser placed in an array on the robot wrist) are making the robots smarter as they operate more adaptively and not just conduct rote moves. It gives instant feedback by processing visual data, which enables the robot to perform proper offsetting and calibration. And, since it can perceive what goes where, installing a car part, such as windshields, fenders, and door panels, can be carried out with a higher level of accuracy.
AGVs
Automated Guided Vehicles (AGVs) are self-guided vehicles designed to haul heavy loads and materials around a large industrial building. In recent years, these operator-free forklift-sized wheeled carriers have become more popular in production facilities. These transporters rely on software to help navigate their movements around manufacturing plants and assembly facilities, often with the assistance of magnetic strips or lasers. With the help of 3D map technology, they are able to carry goods over short-to-medium length distances repetitively. The applications of AGVs at automotive companies are numerous- ranging from the transport of cars and major components, like front-end modules, fascias, instrument panels, and seats, through the assembly line to ‘chassis marriage’– where the chassis is synchronized with the car body. AGVs help optimize workflow processes and improve workplace safety.
Automated Welding
Robotic welding has been one of the primary robotic applications in the automotive sector since the 1980s, traditionally for spot and arc welding. The smarter six-axis robotic welds of today can perform a range of welding techniques from laser to friction to complete bodywork solutions. Cobots have a shared workspace with not just humans but also work in tandem with other robotic systems engaged in massive assembly lines. Robotic welders and handlers must collaborate to keep the assembly line moving. This makes production facilities more automated and streamlined while improving the welding quality as well as the speed of multi-material vehicle production.
Exoskeleton Devices
Although industrial robotic arms do most of the automotive operations, many of the assembly tasks are still accomplished manually. Hence, to reduce the fatigue on the human hand, exoskeletons—essentially wearable robots— are used for repetitive operations in manufacturing. General Motors has developed robotic glove technology along with NASA, called RoboGlove, to add strength and grip to the human hand. “It’s a glove driven by a mechanical delivery system that you wear on your back like a knapsack, and it increases your grip strength,” Dan Grieshaber at GM, explained. “As you grip, it’s aiding you with more assistance. It greatly reduces fatigue.” The "gripper" comes with sensors, actuators, and simulated nerves, muscles, and tendons that not only reduce fatigue but also increase manual dexterity.
Over the past few years, robots have come a long way- from being intimidating and seemingly life-threatening machines to the slick robotic technology of today, adept at working hand-in-hand with humans. In the present times, when driverless cars are on the verge of becoming a reality, carmakers are rethinking manufacturing processes giving way to innovative, increasingly automated production lines. With the help of artificial intelligence (AI), automotive assembly lines are becoming more efficient, productive, and cost-effective. Furthermore, key players are investing continuously and coming up with better services to cater to the demand of end-users. In the future, this competitive industry is expected to see a revolutionary paradigm shift, ushering in an exciting era of automated vehicles.
Author: LinePar offers reviews and product comparisons of automobile parts and accessories.
Comments (0)
This post does not have any comments. Be the first to leave a comment below.
Featured Product
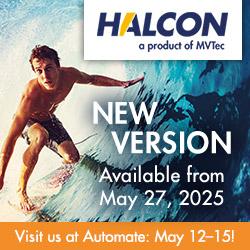