Energy Saving in Die Casting Automation
The manufacturing industry has been at the forefront of automation for as long as robotics have been around. Before the first industrial robots moved onto factory floors, manufacturers were already experienced in finding ways to get more done in less time. Now, with robots everywhere, they're still finding new applications and benefits of automation.
Automation has come a long way since the days of the industrial revolution. Not only are today's robots highly sophisticated, but you can also find them in nearly any sector you can imagine. Even something as seemingly straightforward as die casting benefits from robotics.
Die casting, the process of forcing molten metal into molds, is far from new. Today, casting processes use a lot more advanced technology, specifically robots, than in years past. These 'bots have many advantages in die casting, but energy saving is one of the most substantial.
Die Casting and Energy Consumption
Die casting can be one of a factory's most energy-intensive processes, which creates sustainability and cost issues. As you might imagine, heating metal to a melting point takes a lot of energy. Cooling these materials and moving them around also consumes electricity, leading to some substantial costs.
Energy consumption can account for 25% of die casting costs, so you can see why manufacturers would want to save energy. Figuring out how to lower electricity consumption is not always as straightforward as you might think, though. Some parts of the process aren't possible without using a certain amount of energy.
If you're going to melt metal, you need a lot of heat, and there's no going around that. Since liquid metals aren't particularly light, injecting them into a cast also takes a lot of pressure, which takes energy. As a result, finding places where manufacturers can cut down on energy consumption can be challenging.
Surprisingly, though, 40% of die casting energy consumption happens while the machines are in standby mode. Manufacturers may not be able to reduce the consumption rate of processes like heating by much, but there's still a lot to improve.
Where Automation Fits Into Die Casting
So, where do robots fit into all of this? The process of melting metal and pouring or injecting it into molds doesn't seem like one that needs automation. Despite its apparent simplicity, modern die casting often involves little to no human intervention.
The most obvious application for robots in die casting is in the pouring or injecting stage. Factories use automated machines to get molten metal into molds one way or another. Using robots for this part of the process allows manufacturers to remove the risk that molten metals could pose to human workers.
Moving these casts full of molten metal also typically involves robots for the same reasons. Cooling the molds, either by fans or liquid, is another area that manufacturers often assign to machines. Die casting is a robot-heavy process these days, but what does that mean for energy consumption?
It takes electricity to run a robot. At first glance, you may think they would harm energy savings. As counterintuitive as it may seem, automating the die casting process can improve energy efficiency more than it hinders it.
How Robots Can Save Energy
One of the most substantial benefits of automation in manufacturing is increased consistency. Automated die casters provide the same result every time, which means fewer mistakes, meaning more efficiency. When you don't have to redo anything, you run machines for less time and save energy.
Robots generally work faster than people do, too, which saves energy in the long run. Since they do the same amount of work in less time, they can produce more for the same amount of electricity. Alternatively, they could help manufacturers produce the same amount with less power.
Automated machinery tends to be more precise than human workers, too. Precision may not seem like it impacts energy consumption, but the more accurate you are, the less waste you create. With less waste, you don't have to spend as much energy making up for losses or cleaning.
On top of these advantages, robots don't consume as much electricity as you may think. Compared to the other parts of the process, like running idle machines and cooling, robots themselves use relatively little energy.
Making Die Casting Robots More Efficient
Even with all the benefits they present, die casting robots can still improve their energy efficiency. Many of these improvements happen naturally as engineers conceive more efficient robots. The newer the machine, generally speaking, the less energy it will use doing the same task.
One of the most promising areas for improvement in these robots is their downtime. Many of them idle while they're not actively working, and just like when you let your car idle, that wastes energy. Automating systems so that they power down when not in use can save a considerable amount of electricity and money.
New, high-efficiency motors in robotic pumps can also lead to considerable savings. A new 22 kW motor can save enough energy costs to make up for its price in just 600 hours of operation. A 15 kW model will do so in 1,000 hours, which is still an impressive figure.
A process can only be as fast as its slowest step. If a robot works faster than another step can keep up with, it uses more electricity than necessary. As a result, designing robots to work as fast as needed, not as fast as possible, can lead to more savings.
Automation Can Lead to Substantial Energy Savings
Automation in the manufacturing sector comes with a variety of benefits, or else it wouldn't be so common. As the field of robotics keeps advancing, these advantages only increase.
Die casting may seem like a hopeless case for further energy savings, but that's far from true. With the help of automation, manufacturers can alleviate some of the high energy costs of die casting. It may not be a new practice, but modern-day technologies are making it as good as new.
Comments (0)
This post does not have any comments. Be the first to leave a comment below.
Featured Product
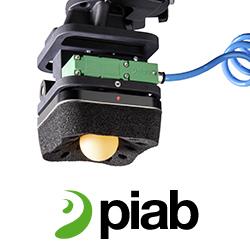