How Robotics Are Being Used in the Packaging Industry
The packaging industry is no stranger to robotics, having implemented robots long before the digital revolution. Though packaging robots may not be anything new, the COVID-19 pandemic has put renewed emphasis on their utility. The use of robotics in COVID has proved how integral these machines are to the industry's success.
If the packaging sector hadn't been an early adopter of automation, it would have struggled through the pandemic. That's not to say that the situation has been easy, but it could've been much worse without robotics. Facilities that took full advantage of automation have fared best.
Robotics use cases in the packaging industry have protected workers, upheld efficiency and made facilities more flexible. Here's how.
Keeping Employees Safe
The most pressing concern for any workplace during a pandemic is protecting its employees' health. The Centers for Disease Control and Prevention (CDC) recommends that factories space workers 6 feet apart, but enforcing this isn't always straightforward. Placing robots in every other position can help ensure employees maintain an adequate distance, reducing their risk of spreading COVID-19.
Costco's highly automated chicken packing plant in Nebraska reported just one COVID case among its 800 employees. While robots were likely not the only factor contributing to that figure, they undoubtedly helped. This instance isn't the only use case of robotics helping reduce COVID infections, either.
Denmark's Danish Crown employs 8,000 workers across eight meatpacking facilities. They also operate a considerable number of robots, which helped them keep COVID infections below 10. Since workers don't have to be in close contact with one another, it's harder for the virus to spread.
Maintaining Efficiency
Protecting worker health hasn't been the only use for robotics amid COVID in the packaging industry. Packaging facilities may not be able to have the same number of people in the building as before. Robots have helped them maintain efficiency with this reduced human workforce.
A frozen food packing facility found it needed additional packaging for a new box style. These boxes account for 30% of their production volume, so adding the new layer efficiently is crucial. With limited human workers, they turned to robotics, which enabled them to maintain their output goals.
As lockdowns began, packaged goods sales skyrocketed, leaving packaging facilities with increased demand. At the same time, many couldn't hire new workers due to COVID safety measures. By turning to robots, companies met this demand without putting lives at risk.
The Changing Role of Robotics
The packaging industry has had to adapt to several new challenges amid the pandemic. In addition to shifting demand and new safety standards, they've faced disruptions in the supply chain. Many of these changes have been unexpected and inconsistent, too, highlighting the need for flexibility.
Robotics in COVID have had to serve different roles and meet new needs, so the industry is shifting. The aforementioned frozen food packing facility had to employ slower, more delicate robots since they'd be working close to humans. As robot-human collaboration is becoming more common, robot design has to account for the safety of human workers.
The need for flexibility leads to a need for more general-purpose bots instead of highly specialized ones. Robots, like the factories they inhabit, need to adapt to new scenarios should they arise. As the packaging industry is becoming more flexible, so are its machines.
Robots Are Helping Sustain the Packaging Sector
The packaging industry is facing unprecedented challenges, but robots are helping sustain it. Given the efficacy of these robotics use cases, it's clear why the packaging robot industry could reach $7.6 billion by 2027. Packaging facilities must automate to survive.
This shift toward automation was inevitable, but the pandemic accelerated it. Robotics in COVID have proved their worth and will undoubtedly see record adoption rates in the years to follow.
Comments (0)
This post does not have any comments. Be the first to leave a comment below.
Featured Product
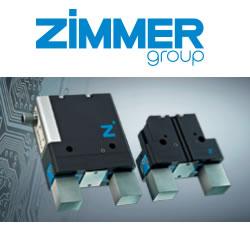