5 Considerations for Deploying Industrial Robotics
Of the Industry 4.0 technologies reshaping industry right now, new industrial robotics has some of the most significant potential to transform factory work.
However, not every deployment of new robots goes smoothly. There are significant challenges to adopting any new technology, and the complexity of cutting-edge robotics means there is serious room for error when deploying industrial robots.
These five considerations are crucial to keep in mind when planning to adopt and integrate industrial robotics.
Robot Safety
Robots are typically dangerous. Moving parts, components like welders, and high levels of force can all pose serious safety risks to workers, especially without the proper precautions.
If a robot will be in close contact with workers, you should consider the safety measures you’ll need in place to keep workers safe. When investigating potential options, you may also want to see which safety features a robot manufacturer can offer, as well as the amount of space and the workflows you’ll need for workers to operate a robot safely.
In facilities where space is at a premium, for example, smaller robots with low-profile footprints may be both cost-effective and safer.
You may also invest in robots that come equipped with safety features, or models specially designed to operate close to human workers.
For example, many new collaborative robots (cobots) are designed with features — like force limiters and padding around sharp edges — that make them safer to work around. However, even these cobots can pose serious safety risks and will require specific safety practices.
Power Consumption and Energy Efficiency
Industrial facilities consume significant amounts of energy. Adding additional automated technology, like robotics platforms, can further drive up a facility’s spending on power.
Before committing to a platform, be sure to consider the amount of power it will consume. In many cases, you may find that a comparable robot or system provides the same features and uses less power.
You should also ensure any new infrastructure used to support your robots meets important energy-efficiency regulations. For example, you’ll want to make sure any newly installed transformers meet the DOE standards on transformer energy efficiency. This will help your facility keep energy costs as low as possible and avoid potential fines.
Platform Complexity
Some robot platforms are more complex than others. This means they may require more technical investment to set up and maintain.
Before committing to a new robot, be sure you know how difficult the system will be to maintain and if current facility technicians are ready to handle the operation and maintenance of the system.
Maintenance Strategy
For any new robot a facility purchases, there should be a plan to maintain it. This plan should include a maintenance strategy for the physical components of the robot plus any digital or cloud platforms that support it.
When developing a maintenance strategy, you may also want to consider the new maintenance strategies enabled by Industry 4.0 tech. With the right platform and combination of IoT sensors, for example, you can implement a predictive maintenance strategy. This uses data on machine performance to predict failure and catch issues earlier.
Platform Cybersecurity
Every internet-connected device in a facility is another opportunity for hackers to break into a facility’s network. If not properly secured, a new robot platform can create serious cybersecurity risks.
Best practices, like endpoint security and the adoption of industry standards for automation platform cybersecurity, can help keep a facility safe.
However, it’s also important to consider native cybersecurity features and identify which platforms or robots may be less vulnerable to a cyberattack than others. In the same way that facility managers want a robot that meets production needs, they should also make sure any robot purchase has cybersecurity features that make site security easier and more practical.
Key Considerations for New Industry Robots
Robotics can offer major benefits for any facility — but managers should be careful when sourcing or deploying a new platform. Issues like robot safety, energy consumption, and cybersecurity can all be much easier to handle with the right choice of robot.
Comments (0)
This post does not have any comments. Be the first to leave a comment below.
Featured Product
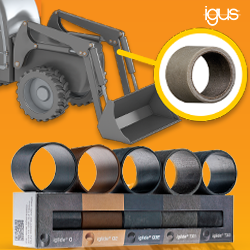