Seafood Processors Turning to Robotics And Automation
Like many industries, the seafood processing industry faces serious challenges — including volatile demand, an unreliable supply chain, and serious labor shortages.
New developments in robotics — including smart robotics, collaborative automation, and similar technology — may be essential for processors handling these modern challenges.
Some of the latest robots can assist workers, simplify seafood handling, and even fully automate processes that could never have been automated before — allowing processors to keep up with demand despite a growing labor gap.
Automation, Robots Necessary for Modern Seafood Processing
Seafood buyers demand cheap fish in massive quantities. For processors, this has often meant turning to automation to process fish and seafood at a pace that enables them to stay competitive.
For smaller processors, the pressure to adopt new tech that increases facility throughput can be especially intense.
Some cutting-edge robots fully automate tasks, taking over labor that previously had to be performed by humans. In 2017, for example, some of the first crab plant robots in Alaska went online.
These robots cut and shell crab that would otherwise go to market still in the shell. For seafood processors, the difference in value that shelled crab meat offers, without extra investment in labor, can have a major impact.
Similar robots that debone and fillet fish are also becoming increasingly common. For example, the FleXicut processing platform uses x-ray technology to identify needle-like pin bones. The system can then neatly remove them using water jets.
While fish that tend to be similar in size, like salmon, have always been a good fit for machine processing, fish that are more variable in size, like cod and whitefish, have typically required human labor. New robots are helping to change this, freeing up workers for more important and less repetitive tasks.
As in many other industries, most processors aren’t after 100% automation, or anything close to that level of adoption. Instead, many are starting to use automation and robotics to support workers, helping to cut down on dull or repetitious work that can lead to musculoskeletal injuries.
For example, collaborative robots, sometimes called cobots, are an increasingly common offering from developers of food processing robotics. These robots typically include safety features — padded joints, force limiters, motion sensors — that enable them to work safely and in close proximity to human workers.
The low weight of many cobots also means they can be easily moved, making them a good fit for agile workflows that may see food processing production switch from one item to another as demand requires.
They can also be less of a commitment than conventional factory robots, which are often heavy and designed to be used for a specific set of tasks, and may be difficult to reconfigure for different types of labor.
For example, gripping and handling robots can be used to gently transport processed fish away from a workstation and prepare it for packaging. This can help a worker focus on tasks that require human attention.
The cobot-worker pair can create a more streamlined workflow and also improve site safety — having a robot arm dedicated to handling raw fish can reduce the risk of cross-contamination.
In the words of Kurt Nielsen, the director of robot technology at Danish food processing robotics company DTI, “robots are not a replacement of humans, but a tool to improve the productivity of people. It’s about collaborative technologies.”
Sustainability in Seafood
The increased demand for seafood may pose challenges for more than just processors.
Overfishing and unsustainable seafood production are likely to blame for declining fish populations around the world. Around 3 billion people worldwide depend on seafood in their daily diets. Overfishing puts both these billions and ocean ecosystems at risk.
At the same time, research from ocean advocacy groups has found that sustainability in seafood fishing can actually have net positive impacts on the environment.
It may be difficult, however, to balance the growing demands of consumers against the less productive and more sustainable practices necessary to process seafood.
Robots, again, may provide some help here, though on the production side. Researchers are experimenting with the use of autonomous, fish-like robots that navigate underwater, providing information on local ecosystems, including environmental conditions and ecosystem health.
How Robotics Can Help Seafood Processors Stay Afloat
Seafood processors are likely to face demand volatility and labor shortages well into the future. Automation provides a valuable tool that can help them manage these challenges. And as tech improves, making cobots and automation platforms even more flexible, they could provide even more value.
While the seafood industry faces challenges that processing technology may not be able to solve — like overfishing — robots may be able to make sustainable seafood processing more widely possible in the near future.
Comments (0)
This post does not have any comments. Be the first to leave a comment below.
Featured Product
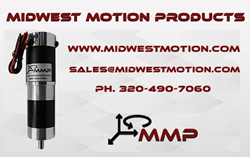