The Intersection of Telematics and Robotics
Telematics is a broad field, covering far more technologies and subcategories than people often realize. While the most recognizable subset is in the transportation industry with things like GPS navigation and usage-based insurance, that’s far from its only application. One of its most exciting and fastest-growing use cases is in robotics.
In its most basic sense, telematics combines telecommunications technology and informatics, the science of computational systems and data. As the Internet of Things (IoT) has grown, this field has stepped into the spotlight. A broad range of commercial activities, from fleet management to manufacturing, now rely on telematics.
The fourth Industrial Revolution, Industry 4.0, has seen telematics and automation come together. Here’s a closer look at the intersection of these two innovations.
Machine Learning Navigation
Perhaps the most recognizable instance of telematics and robotics working together is advanced navigation systems. Machine learning algorithms may not be what people think of when they hear “robotics,” but they are a type of software robot. Some logistics companies today use machine learning to process telematics data and to navigate more efficiently.
The most famous example of AI-based navigation is UPS’s On-Road Integrated Optimization and Navigation (ORION). ORION analyzes road conditions, weather and traffic to determine the most efficient route possible for drivers. UPS says the system reduces travel by 8 miles per driver, leading to considerable time and fuel savings.
To achieve these savings, systems like ORION need both telematics and robotics. Telematics technologies gather and send data that software robots then process to produce actionable insights.
Real-Time Remote Monitoring
Just as telematics itself covers more than just transportation, so does the intersection of telematics and robotics. As Industry 4.0 grows, more manufacturers are integrating IoT connectivity into their facilities’ robotic systems. This trend uses telematics to make real-time data from a factory’s robots remotely accessible.
One of the primary benefits of robotics is that it’s more efficient, but stopping production to inspect a robot hinders that productivity. The answer is to use telematics to send operational data to the cloud or remote devices. Manufacturers can then look at their robots’ condition and operational efficiency without examining the robot itself.
With remote access to real-time operational data, manufacturers can see if and how their robots could improve. They can then make more informed decisions about reorganizing their workflows or investing in future automated systems.
Predictive Maintenance
One of the most valuable applications of this remote data monitoring is predictive maintenance. Traditional maintenance relies on accurate record-keeping, which workers often neglect or overlook due to everyday stresses. Predictive maintenance provides a solution by using sensors to determine when something needs attention and alerting workers remotely.
Poor maintenance strategies reduce a facility’s productive capacity by 5%-20%, mostly due to downtime. Predictive maintenance prevents that by forecasting problems before they cause breakdowns, letting workers fix them with minimal disruption. Similarly, this strategy ensures each machine or vehicle only receives the maintenance it needs, preventing unnecessary repairs, which also cause downtime.
Since robots are substantial investments, many factories use predictive maintenance to keep their systems in optimum condition. Like robotics itself, these maintenance strategies come with high upfront costs from the technology they use but lead to considerable savings over time.
Remote Operation
A newer but growing area of telematics and robotics intersection is remotely operating robots, or teleoperation. Remote work has grown over the past few years, but some jobs, like those in a factory or hospital, aren’t conducive to working remotely. Teleoperation enables workers like doctors and machine operators to perform delicate work across long distances.
Telematically controlled robots let the world’s leading experts lend their skills to people around the world. For example, in 2019, doctors in China performed surgery 1,900 miles away from the patient. Thanks to improvements like 5G connectivity, telematics networks can now support delicate remote operations like this with just milliseconds of lag.
Similarly, factory workers can use telematics to control robots from their homes. This gives these employees flexibility in a field where there used to be none. If factories need to reduce their in-person capacity over health concerns, they can now do so without sacrificing productivity.
Mobile Robots
Telematics can also help robots control themselves. While most industrial robots today are stationary, mobile bots have become increasingly common as technology has advanced. These machines often rely on a combination of sensors and telematics services to navigate safely and efficiently through the workplace.
Material handling and picking are repetitive, often inefficient processes, making them ideal for automation. Telematics networks within a factory or warehouse can guide robots to the correct items, then show where they need to take them. This combination of automation and precise location technology can make these historically slow processes far more efficient.
As telematics technology improves, mobile robots could work in new use cases, traveling farther distances. This movement is already starting to occur, with food delivery robots coming to many campuses this year.
Self-Driving Vehicles
The logical next step in mobile robots, and possibly the most highly anticipated application of telematics and robotics, is autonomous vehicles. These machines rely on complex telematics technologies and robotic processes like machine learning to navigate. While self-driving cars are likely still years away from populating the streets, that future grows closer all the time.
Long-haul trucking is an ideal early use case for driverless technology, as it uses long, often straightforward routes, and highways have more predictable traffic. One autonomous truck startup, TuSimple, plans to start unsupervised driverless routes this year. This step forward could signify that self-driving trucks are not far off from being a reality.
Both telematics and robotics will have to advance for driverless cars to become widespread. As each technology sees broader adoption, they will get the data necessary to push them forward.
Telematics and Robotics Are Growing Closer Together
As technology fields advance, they grow increasingly intermingled. Telematics and robotics may have once been entirely separate sciences, but today, they work together in many applications. From here, they’ll likely only grow closer together until they’re inseparable in many industries.
These examples are just a few use cases of telematics and robotics. While it may not be immediately obvious, the intersection of these technologies is already all around, and it’s growing every day. Together, they can thoroughly disrupt the industrial world.
Author Bio: Martin Banks is the managing editor at Modded. Follow him on Twitter @TModded for frequent updates on his work.
Comments (0)
This post does not have any comments. Be the first to leave a comment below.
Featured Product
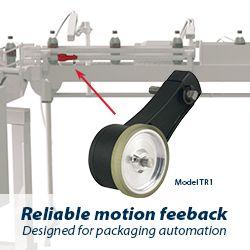