Trends in Industrial Robotics to Watch in 2022
Over the last decades, robots have transformed from expensive industrial exhibition pieces--in 1966, GM’s Unimate played golf and poured a beer on the Johnny Carson show--into everyday workhorses. We’ve seen increasing adoption by diverse industries, from life sciences to electronics, to food and consumer goods manufacturing. This is primarily owing to new dexterity, better machine vision, as well as wider robotics availability. In fact, according to statistics from the Robotic Industries Association (RIA), Q4 2020 marked the first time non-automotive orders exceeded those by automotive vendors.
Meanwhile, the last two years accelerated ongoing robotic trends like AI integration, agile design, and widespread IIoT adoption. At the same time, new pressures from changing worker availability, supply chain disruptions, and ongoing pandemic concerns created a higher marketplace demand for manufacturing robots.
The next twelve months will set us on a path that may prove difficult to turn from. Changes happening now lead forward, and it’s unlikely we will ever come back from where they lead. Here are five industrial robotics trends and how they will affect industrial sectors in 2022 and beyond.
Maintenance Robots on the Rise
Maintenance is one of the most important tasks for any industrial location, offering a chance to predict and prevent breakdowns rather than react to them. A report from the National Institute of Standards and Technology(NIST) estimates maintenance costs to be 15% to 70% of the cost of goods produced, and showed a favorable return on investment for shifting maintenance toward predictive techniques.
Maintenance tasks are repetitive by nature, so are well-suited to turning over to robotics. Additionally, the AI tools within these advanced machines can help move maintenance to a higher level, from a human-centric activity to a highly autonomous one. With time, AI and robotics may move maintenance from a ‘best practices’ preventive check-list to more proactive predictive actions determined by identifying potential problems through regular data analysis--more of a ‘repair before the problem exists’ model.
Robots As A Service
Formerly, expertise (and the cost to retain it) was a restricting factor for smaller firms who wanted to add robotics to their manufacturing floor. But now with the rising everything-as-a-service (*aaS) trend, this is no longer an issue.
Not every company has the means to hire all the employees required to support industrial robotics, especially during the largest skills crisis manufacturing has faced in decades. Yet, now companies can enjoy robotic process automation through RaaS, or Robots-as-a-Service models, without traditional ownership headaches. Such subscription-based plans became familiar to many as SaaS (software as a service) models. RaaS plans work in a similar fashion.
Rather than buying outright, robotic devices are leased. Subscriptions often include monitoring, analytics, and preventive maintenance. The benefits are many. This includes rapid scalability, decreased upfront capital, the capability to rework platforms as needs change.
Robotics for New Places, New Challenges
According to a 2021 McKinsey report, 2030 will see as much as ten percent of today’s manufacturing default to 3D and 4D additive manufacturing processes. 3D printers, most of which are Cartesian coordinate robots, offer broader design possibilities and quicker customization as they minimize waste and energy consumption. Increasing 3D robotics adoption will enable new business models, including Printing-as-a-service (PaaS.)
Meanwhile, as robotics become smaller, tougher, and more agile, industries find new uses in both the largest and smallest spaces. Mecademic Robotics has introduced a line of “the world’s smallest, most compact, and precise industrial robots.” These robot arms integrate with PLCs or PCs without a proprietary programming language. The line includes six-axis and four-axis industrial robot arms as well as a miniature parallel gripper. At the same time, companies like Astrobotic and OffWorld, Inc have focused their attention on creating landers, rovers, and mining robots for NASA and other off-world customers.
Cobots Replacing Live Workers
Worker shortages are hanging on, even as employment subsidies fall by the wayside. As the economy recovers, certain jobs are being permanently replaced by collaborative robots.
Often, these new cobot workers are faster and more efficient than the workers they replaced. They don’t take time off, and they don’t call in sick. It’s unlikely we will see a return to flesh-and-blood staff for many positions any time soon.
Are these trends cause for concern? Some will certainly think so. But at a time when available labor is unable to keep up with demand, it’s unlikely a robot will drive out the need for humanity. Instead, the expectation remains that robots will take over those monotonous and dangerous jobs that need doing while their human coworkers move up to higher-value tasks. Research by the World Economic Forum suggests by 2025 machines will do more work than humans. However, this robot revolution will also add 58 million net jobs to the global economy.
Technology writer Marla Keene works for Automation Industrial, an industrial automation supplier located in North Carolina. Her articles have been featured on EPSNews, Vault, and Quality Magazine. Before working for Automation Industrial, Marla spent twelve years running her own small business.
Comments (0)
This post does not have any comments. Be the first to leave a comment below.
Featured Product
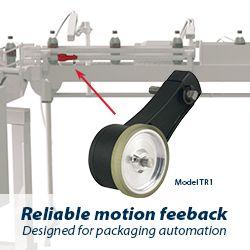