Working With Robots With Different Levels of Collaboration
Collaborative robots are changing the rapidly evolving workplace, improving safety and productivity. Robots offer many potential benefits for businesses in numerous industries. By working with robots, employees can gain valuable technical skills and perform their jobs more efficiently. There are varying levels of collaboration that businesses can implement and strategies they can use to make sure collaborative robots are safe.
The Benefits of Working With Robots
Businesses have compelling reasons for investing in robots, particularly collaborative robots. In fact, the collaborative robotics market has a 35% anticipated CAGR through 2027. Supply chain frustrations and hiring challenges are only accelerating robotics adoption, particularly in manufacturing and warehousing.
These industries are under a high amount of strain due to supply chain, demand, and staffing struggles and have many potential applications for robotics. For example, automated warehouses have gained a 60% increase in sales as a result of the higher productivity offered by robots.
In any industry, robotics has the potential to increase productivity, efficiency, and product quality while reducing waste and expenses. In many industries, robots can take on jobs that present a high risk of employee injury. This reduces stress for employees and increases workplace safety. It is also likely to save employers money on insurance and medical expenses for any workplace accidents that would have otherwise occurred.
Robots alone are often confined to simple tasks that can be pre-programmed in. With the help of AI and IoT, however, robots are capable of a vast array of workplace tasks. A robot could automate quality control using IoT and computer vision, for example.
Balancing Robots and People
The benefits of working with robots are not without their potential drawbacks. Any discussion about robots in the workplace needs to include the possible impact on employment. The level of collaboration a business allows between employees and robots is also a crucial consideration and affects safety as well as employment.
There are generally two narratives going on concerning working with robots. Some argue that robots improve workplace safety and increase productivity and efficiency. Others argue that robots are displacing and negatively impacting employees, particularly those without a college degree.
For example, the automotive industry is estimated to employ 38% of robots in the U.S. A study by the MIT Sloan School found that these robots are negatively impacting employees, specifically by replacing jobs in the automotive industry and others.
This idea that robots are stealing jobs has come into question over the last couple of years as labor shortages have grown. The National Association of Manufacturers estimates that over 2 million manufacturing jobs will go unfilled by 2030. Manufacturing companies are among the largest adopters of robotics, as mentioned above with the automotive industry.
So, if robots truly are replacing jobs in manufacturing, there is little threat of employees suffering as a result. In fact, working with robots is much more likely to improve employees’ experience by reducing strain on understaffed teams. Some robotic equipment can coexist in an area near where people work. Other instances in the factory may require more collaborative efforts between people and machines.
There is a happy medium that businesses can find implementing robots. Collaborative robots are able to deliver the benefits of automation while still utilizing employees’ valuable skills. Collaborative robots augment the strengths of employees rather than attempting to fully replace them.
Are Side-by-Side Collaborative Robots Safe?
Workplace robot integration is a spectrum. A business could confine robots to a closed-off space isolated from any employee contact. On the other hand, they could have people working side-by-side with a fleet of robots independently traversing a workplace floor. The degree to which a business has its employees collaborate with robots depends on the application as well as workplace safety.
The reality is that robots can be dangerous pieces of equipment if operated or handled incorrectly. While robots can improve safety in some regards, for example by eliminating strain caused by repetitive movement, they can still cause harm. Most of the time, though, this is the result of improper use. Therefore, it’s crucial to train workers about the specific hazards of each robotic equipment. Initial training and retrainings will ensure that employees understand the risk and how to work safely around these machines.
Many collaborative robots are built with thorough safety features designed with human co-workers in mind. New technologies are also helping to improve robot safety, as well. For example, AI and IoT sensors can help robots better identify humans around them, allowing them to stop moving if anyone comes within a certain radius.
Normal employees who work with collaborative robots have repeatedly mentioned how helpful they are. It appears working with robots truly can be safe and beneficial for employees, as long as businesses take the necessary safety precautions.
Working With Robots Strategically
Ultimately, businesses need to consider what goals are most important to them in order to pinpoint the level of robotic collaboration they want. A company that needs to boost productivity at any cost may need to shift to wide-scale automation, which would include limited collaboration and a primarily robotic workforce.
In contrast, a business that wants to address staffing shortages may want to encourage collaboration with robots, using them to boost the skills and capabilities of existing employees.
The right level of collaboration also depends on the industry in question. Some industries lend themselves more naturally to certain types of robots than others. Warehousing, for example, has many easy opportunities for collaborative robot integration. A robot can be used to move heavy pallets or transport items around a sprawling warehouse, saving employees time so they can focus on more complex logistics tasks.
In any industry, however, it is important to keep employees in mind. No matter the level of collaboration with robots, employees should receive thorough robotics safety training. Businesses should also remember to keep the workplace culture grounded. Robots may deliver an increase in productivity, but this can also leave employees feeling stressed as they try to compete with their robot counterparts.
The Industry 4.0 Workplace
As Industry 4.0 drives a widespread technological transformation in the workplace, collaborative robots are becoming a central part of the workforce. These robots have the potential to deliver invaluable benefits for businesses, employees, and customers. However, businesses need to be strategic and considerate about how they integrate robots and the degree to which employees collaborate with them. Working with robots successfully requires a commitment to safety and a balance between robot and human skills.
Comments (0)
This post does not have any comments. Be the first to leave a comment below.
Featured Product
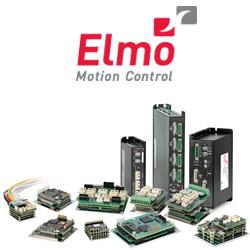