Researchers develop first self-healing, electrically conducive, soft material
Carnegie Mellon University engineers have developed a soft material with metal-like conductivity and self-healing properties that is the first to maintain enough electrical adhesion to support digital electronics and motors. This advance, published in Nature Electronics, marks a breakthrough in softbotics and the fields of robotics, electronics, and medicine.
At Carnegie Mellon University, softbotics represents a new generation of soft machines and robots manufactured by multi-functional materials that have integrated sensing, actuation, and intelligence.
The research team introduced the material, a liquid-metal filled organogel composite with high electrical conductivity, low stiffness, high stretchability, and self-healing properties in three applications (See accompanying video):
- damage-resistant snail-inspired robot
- modular circuit to power a toy car
- reconfigurable bioelectrode to measure muscle activity on different locations of the body
“This is the first soft material that can maintain a high-enough electrical conductivity to support digital electronics and power-hungry devices,” said lead author Carmel Majidi, Professor of Mechanical Engineering. “We have demonstrated you can actually power motors with it.”
The fully untethered snail robot used the self-healing conductive material on its soft exterior, which was embedded with a battery and electric motor to control motion. During the demonstration, the team severed the conductive material and watched as its speed dropped by more than 50%. Because of its self-healing properties, when the material was manually reconnected, the robot restored its electrical connection and recovered 68% of its original speed.
The material can also act as a modular building block for reconfigurable circuits. In their demonstration, one piece of gel initially connected the toy car to a motor. When the team split that gel into three sections and connected one section to a roof-mounted LED, they were able to restore the car’s connection to the motor using the two remaining sections.
“In practice there will be cases where you want to reuse and recycle these gel-like electronics into different configurations, and our toy car demonstration shows that’s possible,” explained Majidi.
Lastly, the team demonstrated the material’s ability to be reconfigured to obtain electromyography (EMG) readings from different locations on the body. Because of its modular design, the organogel can be refitted to measure hand activity on the anterior muscles of the forearm and to the back of the leg to measure calf activity. This opens doors to tissue-electronic interfaces like EMGs and EKGs using soft, reusable materials.
“Softbotics is about seamlessly integrating robotics into everyday life, putting humans at the center,” Majidi explained. “Instead of being wired up with biomonitoring electrodes connecting patients to bio measurement hardware mounted on a cart, our gel can be used as a bioelectrode that directly interfaces with body-mounted electronics that can collect information and transmit it wirelessly.”
Moving forward, Majidi hopes to couple this work on artificial nervous tissue with his research on artificial muscle to build robots made entirely of soft, gel-like materials.
“It would be interesting to see soft-bodied robots used for monitoring hard to reach places. Whether that be a snail that could monitor water quality, or a slug that could crawl around our houses looking for mold.”
Comments (0)
This post does not have any comments. Be the first to leave a comment below.
Featured Product
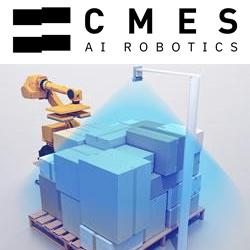