7 Reasons Robots Make a Huge Difference in Food Processing
Robots have been a staple of most manufacturing sectors for decades, but until recently, they’ve been rare in the food industry. Implementing robotics in food processing has historically been challenging, thanks to product irregularity and delicate handling needs. Now that robots have become more precise and adaptive, that automation gap is closing.
Despite their relative novelty, food processing robots have many applications. Here are seven use cases highlighting robots’ disruptive potential in the food and beverage industry.
1.Food Safety
The most important advantage of robotics in food processing is its impact on public health. Roughly one in six Americans get sick from contaminated food or beverages annually, and these foodborne illnesses cost the U.S. $15.6 billion a year. Robots can help by minimizing cross-contamination risks.
Because robots never leave the facility, they cannot introduce outside contaminants to food processing lines like employees can. Similarly, machines can’t catch diseases that then spread among raw ingredients. Automating the most contamination-prone processes helps food manufacturers prevent many outbreaks.
Microbial contaminants can reside on robots’ surfaces, but these machines are typically made of nonporous metals. As a result, they’re easy to clean and disinfect between shifts, further preventing cross-contamination risks.
2.Higher Productivity
General, less industry-specific robotics advantages also apply to the food and beverage sector. One of the most significant is automation’s ability to boost workplace efficiency. Food processing robots can work much faster than human employees, letting facilities sustain higher demand without much disruption.
Martel Foods, a Canadian prepackaged food manufacturer, is an excellent example of this potential. After automating the lidding process of placing the top piece of bread on a sandwich, Martel increased its output from 35 to 52 sandwiches per minute, a nearly 60% increase. If automating such a simple task can yield such significant improvements, consider what facilitywide robotics implementation could do.
In addition to performing tasks like this faster than humans, robots free the workers who once handled these processes to focus on other jobs. Consequently, a single robot can improve productivity in at least two workflows.
3.Error Reduction
Robotics in food processing plants also minimizes error risks. Humans are naturally prone to mistakes, and boring, repetitive workflows like packaging food, filling bottles or checking produce make them even more likely. Robots, by contrast, don’t get bored or tired.
Food processing robots deliver the same precision and quality every time they perform an action. As a result, they’re far less likely to make mistakes. When even simple errors can lead to food safety issues or mislabeled products, that accuracy is difficult to ignore.
Placing robots in quality control workflows further improves error reduction. These machines generate data on each product defect, and analyzing this information can reveal where issues arise. Food manufacturers can then address them at their source to prevent mistakes altogether.
4.Addressing Labor Shortages
The growing prominence of food processing robots may stir up fears of job displacement in some people. However, many facilities face significant labor shortages. Robots fill gaps left by humans rather than replace existing workers.
Filling these gaps is an increasingly pressing concern as demand rises without a similar rise in workers entering the industry. Some food manufacturing lines have doubled their output and still need to expand, and automation has proved the ideal solution amid ongoing labor shortages.
These employment gaps are less impactful when robots handle more once-manual workflows. In many cases, the tasks robots automate are also those employees enjoy the least, so rising automation lets workers focus on more engaging work, boosting morale. That improvement can reduce turnover, further mitigating labor shortages.
5.Data Analytics
A less-publicized benefit of robotics in food processing is that these machines provide more workplace visibility. Using an electronic system to manage a task means facilities generate electronic data points for every action these machines perform. Internet of Things (IoT) technology allows gathering that information for analysis.
Food manufacturers can review robot data to see where their workflows are most efficient, where errors are most likely to occur and where any bottlenecks lie. Once they have this facility-specific information, they can make more relevant improvements to boost productivity or reduce defects.
The more a food processor automates, the more effective these data-driven decisions will be. Additional machinery increases information across various processes, helping narrow down issues’ true sources.
6.Outbreak Tracing
Data analytics is particularly useful for tracing foodborne illness outbreaks. Companies that learn of an episode can review their robots’ data to pinpoint where it started and how it spread.
As soon as produce storage temperatures exceed 40 degrees Fahrenheit, E. coli levels can go from undetectable to infectious. Robots that handle this food can feature temperature-reading tools to reveal where and when these factors have reached that danger zone. Manufacturers then know what to fix to prevent further contamination and which other shipments may be infected, informing more effective recalls.
It’s worth noting that robots also make these incidents less likely in the first place by minimizing contamination risks. However, accidents can still happen, and when they do, this traceability is crucial for effective mitigation measures.
7.Processing Improvements
Robotics in food processing can also apply to secondary work, where companies prepare and cook food to serve. Many of the same manufacturing-side benefits apply to restaurants. Eateries can use robots to mitigate labor shortages, become more efficient and minimize health risks.
Restaurant robots are a newer phenomenon than food manufacturing bots, but they’re quickly becoming a common sight. Chipotle has recently rolled out the “Autocado” robot to help employees prepare guacamole faster. This process used to take just under an hour, but Autocado cuts that time in half, potentially saving Chipotle millions of dollars annually.
Robots like this can also help draw customers in, despite the COVID-19 pandemic making takeout’s popularity surge. The idea of machines preparing a meal sounds futuristic and can attract clients curious about the technology, boosting sales.
Food Processing Robots Could Disrupt the Industry
Food processing robots may be a relatively new reality, but they’re already proving to be disruptive. As more industry players adopt these machines, the sector will become safer, more efficient and more cost-effective.
Implementing robotics in food processing can be intimidating, as robots are expensive and complex. However, as these use cases highlight, the resulting benefits can more than make up for those initial disruptions.
Comments (0)
This post does not have any comments. Be the first to leave a comment below.
Featured Product
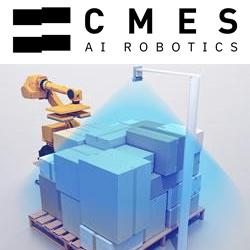