AI and Cobots: The Dynamic Duo Changing Manufacturing
Cobots have made impressive strides in manufacturing. They’ve made automation safer and more flexible, but there’s still room for them to improve, especially as artificial intelligence (AI) functionality becomes increasingly common. Combining AI and cobots yields better results than either technology.
Many cobots already come with some AI features. Others can incorporate external AI technologies if manufacturers have the technical expertise to integrate the two. In either case, AI has several promising use cases in collaborative automation.
Machine Vision
Computer vision is one of the most impactful applications of AI integration in cobots. These machine learning models analyze visual data from cameras and related sensors to “see” their surroundings.
Machine vision benefits cobots in several ways. They could use it to detect nearby employees or unexpected obstacles to navigate safely along factory floors. In addition to preventing collisions, the functionality could let them find the most efficient routes. Considering walking can take up to 50% of the time spent on warehouse operations, any efficiency boost would result in significant improvements.
Machine vision also expands cobots’ use cases. Robots with such features could perform visual-dependent tasks like quality inspections, opening the door to further automation and greater productivity gains.
Sensor Data Aggregation
AI can also improve cobots by aggregating data from multiple sensors. Conventional robot functions often rely on a single sensor system for each action. AI can look at the overall picture between various inputs to make more accurate decisions or adapt to changing conditions.
For example, mobile robots can use AI to combine cameras and GPS for precise obstacle detection. Quality control robots could aggregate vibration sensors, laser measurements and visual inspections to get a better picture of a product’s compliance with company standards.
Sensor data aggregation is particularly valuable in facilities running extensive Internet of Things (IoT) networks. Cobots can gather information from IoT devices throughout the production line and analyze it in context to understand changing conditions within the factory. The robot can then adapt as necessary, such as accounting for slowed speeds after an accident or looking for misaligned parts.
Improved Decision-Making
Similarly, combining AI with cobots enables nuanced automated decision-making. Older, non-AI-capable robots struggle to perform at their peak outside of repetitive and predictable workflows. Machine learning provides the thought process necessary to overcome that limitation.
Such complex decision-making is most impactful in processes where the optimal approach varies between situations. Truck loading and material handling are common examples. Some AI-enabled robots can assess billions of possible layouts within milliseconds to determine the best way to stack boxes.
Over time, these AI models become increasingly accurate as they learn from past experiences and data. Consequently, AI integration ensures automation’s productivity and error reduction benefits increase exponentially.
Easier Collaboration
AI can also improve the fundamental feature differentiating cobots from conventional robots — working with humans. Human-robot collaboration has driven throughput increases up to 300% in some companies, and machine learning makes such substantial gains easier to attain.
Manufacturers can make cobots more collaborative through a few different AI applications. Natural language processing (NLP), which allows automated systems to interpret spoken or written words, is among the most beneficial. A cobot with NLP functionality could operate on voice controls or simple text inputs, making it easier for human co-workers to direct or adjust it.
Alternatively, machine learning algorithms can enable automatic adjustments as cobots learn how their human co-workers tend to behave. No-code, plug-and-play programming is another option, lowering the technical barrier to integrating cobots into new environments.
Ongoing Improvements
AI integration opens the door to ongoing improvements. A cobot investment can yield increasing benefits over time if manufacturers adjust their surrounding workflow. Machine learning takes things further by letting the bot automatically learn from experience, much like a human does.
Consider a mobile material-handling cobot. A non-AI-equipped solution would follow a set path or static programming to retrieve and deliver parts the same way every time. A machine learning-enabled alternative could recognize which paths are more efficient than others or where obstacles often arise. It could then take a different route each time to maintain peak productivity in any situation, improving decision-making over time.
Ongoing improvements like this don’t just apply to efficiency, either. AI-enabled cobots can also become safer or increasingly accurate with new data.
Predictive Maintenance
Some applications of AI-cobot integration happen behind the scenes but are equally beneficial. Predictive maintenance (PdM) is a prime example.
PdM uses machine learning algorithms to monitor health factors like temperatures, vibrations and moving part tolerances. It can predict incoming failures by noticing when operations fall outside the norm. By alerting workers to these issues, AI prevents cobot breakdowns and eliminates unnecessary repairs, as all fixes will be needs-based.
This maintenance optimization can result in cost savings of up to 98% and up to 45% reductions in downtime. Those figures are particularly valuable in light of cobots’ high upfront costs. Applying PdM to a cobot fleet will minimize the ongoing expenses and provide a faster ROI on automation.
Proactive Cybersecurity
Alternatively, manufacturers could use AI monitoring solutions to watch for cybersecurity threats. Manufacturing now accounts for 25.7% of all cyberattacks, making it the world’s most-targeted industry, so proactive security is essential. Machine learning enables a higher level of protection.
The most useful AI applications aren’t part of the cobots themselves but monitor the networks the bots are connected to. Automated breach detection or endpoint behavior analysis algorithms learn how robots and other devices typically behave on a network. As a result, they can spot suspicious activity — implying a breach — in real time.
Once AI security tools identify a potential attack, they can take the cobot offline and alert IT teams. Manufacturers can then address it sooner and prevent the worst outcomes of a compromised robot.
AI Integration Takes Cobots to New Heights
AI and cobots are a perfect match. The adaptability, accuracy and functionality that AI provides push all the normal benefits of cobots to a higher level.
These seven use cases are just a sample of the ways manufacturers can improve their cobot operations with AI. Capitalizing on this potential today will help companies maximize their cobot ROIs and ensure success well into the future.
Comments (0)
This post does not have any comments. Be the first to leave a comment below.
Featured Product
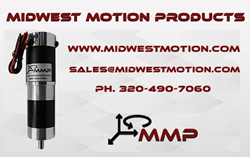