Purigo - Unmanned Orchard Spraying Robot
This electric robot performs the same spraying tasks with only 15.1% of the power (59.5 kW for conventional sprayers, 9 kW for Purigo), consuming six times less energy than traditional systems. Through this innovation, Purigo has achieved unprecedented energy-saving technology and successfully transitioned to eco-friendly electric technology, dramatically reducing operational energy. Purigo sets a new standard for orchard management and paves the way for the future of sustainable agriculture.
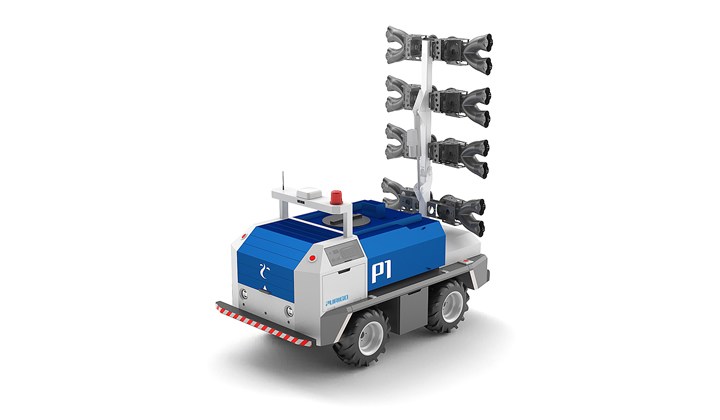
Purigo is compatible with most diluted liquid pesticides (including water-soluble and suspension concentrates), except for solid formulations such as GM, offering a wide range of applications.
Comments (0)
This post does not have any comments. Be the first to leave a comment below.
Featured Product
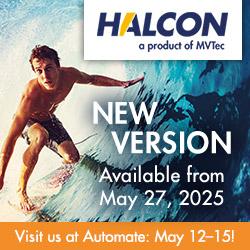