How Is Modular Robot Design Reshaping Factory Automation?
Modular robotic systems are altering workflows in the manufacturing industry. How industrial robots work constantly adapts to increased demand and novel technologies, but it enhances automation potential the most. What is shifting and how can production engineers and electronics experts in these sectors fully leverage the benefits?
Flexibility and Scalability
Industrial workforces and management teams notice the ability of modular robotic systems to expand corporate scopes into new verticals. Their contributions and supplementary assistance to staff allow seamless scaling and flexibility. Engineers may reconfigure any aspect of the machine to execute the most necessary tasks.
For example, consider how a production line may need a robot’s end effectors to measure, but cutters and welders require immediate help. Reworking the modular robot’s controllers allows operations to shift to tackle spontaneous demand. Conventional robotics were less capable of working alongside staff. Their clunky designs and lack of adaptability made them stationary instead of collaborative. Modular options expand their realm of assistance because they have greater mobility and heightened safety standards.
Integration is a breeze, providing a precise yet malleable hand to support the workforce instead of replacing it. Innovations like chain-based modular robotics allow operators to rearrange robotic structures to enhance agility or expand functionality with additional links, instead of seeking a completely different unit for tasks.
Rapid Prototyping and Production
Production cycles constantly forge mainstay products, but management teams allocate countless resources for constructing prototypes. As models come into being, designers scrap blueprints and the process begins anew — creating more waste and throwing away money with every iteration. Modular robotics systems expedite prototyping with a reduced time-to-market window. Pair this alongside 3D printing for reduced material costs and parts scarcity for a powerful working duo.
Research and development are required for all production to maintain competitiveness, especially in industries like automotive and energy. However, only some invest among other pressing financial and labor priorities. Incorporating modular robotics creates in-house R&D opportunities via experimentation, so the environment fosters continued learning. Generating physical prototypes quickly and cheaply lets corporations test ideas for laser cutting or assembly of groundbreaking products with minimal consequences.
Interoperability and Plug-and-Play Integration
Digital transformations struggle to overcome interoperability hurdles. Numerous devices are incompatible with existing infrastructure, but modular robotics systems supersede these concerns while offering plug-and-play solutions for immediate action.
The devices must be user-friendly enough to work alongside humans, but they must also synergize with existing robots of different makes and models. Modularity promotes this ecosystem. Manual configuration may not even be necessary, automating onboarding and setup. Imagine replacing an accessory, like a sensor or gripper, without excessive programming.
Mobile modular robotics (MMRs) are a prime example of their intuitive installation capabilities. These independent units are smaller, but engineers and manufacturing staff may feel free to easily change their peripherals, like manipulators or feedback devices. MMRs can navigate warehouses with complex setups or deliver materials.
Cost Efficiency and Return on Investment
Modular robotics systems also have the chance to automate budget savings without making contentious cuts. As previously explored with R&D, the amount of resources modularity saves by reducing prototypes and defective products to hasten deliverables. The enhanced B2B and B2C satisfaction will make profits more consistent and flourishing, increasing financial and emotional commitments from stakeholders.
Additionally, it slashes operational costs by eliminating the potential for human error from technicians. The ROI for modular systems is more tangible and swift compared to legacy robotics, which requires greater upkeep and layered processes to make it relevant with incompatible digital ecosystems.
Advanced modular robotics support comprehensive data analytics. Integration with machine learning, artificial intelligence, IoT and other Industry 4.0 and 5.0 systems provides transparency from production that conventional robots could not deliver. The insights automate process discovery and business continuity planning by clarifying goals without guesswork.
Maintenance and Upgradability
When one aspect of an antiquated robotic tool is faulty, the rest may become obsolete too. Components may be unavailable, price-gouged, back-ordered or out of print. How industrial robots work to overcome these stopgaps is modular tech. The robots are designed for mass production and quick assembly, meaning upgrading parts and executing preventive maintenance are more intuitive and accessible. Consider the ease of replacing multiconductor cable layers or mounting systems with less headache.
Installing modular parts severely reduces unplanned downtime and planned maintenance. Integration with smart technologies aids operators in knowing when parts are beginning to fault or when an upgrade needs to be addressed. These notifications automate maintenance while opening up production windows for enhanced productivity.
Modular Robotic Systems
The ways industrial robots work to help industry are diverse and ever-expanding. Modular robotics systems amplify this potential tenfold. Their applications are seemingly infinite, shifting to the needs of the manufacturers, engineers, operators and designers. Workflows refine while increasing staff morale by alleviating tedious, precise and dangerous tasks.
Corporations embedding modular units into their processes and operations will experience returns in positive reputation and financial resilience. The best time to get ahead on modular robotics is now.
Comments (0)
This post does not have any comments. Be the first to leave a comment below.
Featured Product
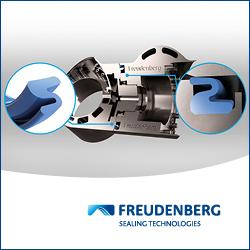