How to Choose the Right NDT Methods for Robotics Manufacturing
Source: Photo by Matias Luge on Unsplash
Robotics must meet high quality standards to function in today’s demanding industrial environments. Considering how expensive these assets are, manufacturers must rely on non-destructive testing (NDT) when ensuring such reliability. However, the optimal NDT methods for robotics are not always immediately evident.
With so many NDT options available, the best one depends on the specific materials and functions in question. As a result, it is often most helpful to vary methods between components. Here is a closer look at which NDT solutions are generally preferable for various robotics component types.
1. Best NDT Methods for Motors and Actuators
Moving parts like motors and actuators must move smoothly but showcase minimal wasted motion and strong material resilience. Consequently, they are often ideal use cases for vibration analysis and ultrasonic testing.
Ultrasonic analysis uses sound waves to identify material flaws. Because it exhibits high sensitivity to minuscule defects, it can detect minor cracks, corrosion or other weak points in areas of contact or corners that may be difficult to inspect visually. Motors and actuators often feature many such geographies, so this advantage is hard to overlook.
Whereas ultrasonic testing is ideal for crack and corrosion detection, vibration analysis is preferable for recognizing bearing failures or misalignment. Defects like these will showcase higher amounts of motion than normal, so vibrations are a relatively easy way to highlight them without rigorous experimentation.
2. Best NDT Methods for Robotics Sensors
NDT is also valuable for sensors, which are often among a robot’s most sophisticated and expensive components. Given such sensitivity, they require gentle, noninvasive quality assurance methods like laser measurement and infrared inspection.
Lasers can detect surface flaws with sub-nanometer precision and are faster than many other measurement techniques. As a result, they are ideal for monitoring optical lenses or sensitive exposed electronics pieces for warping, cracks or similar issues.
Infrared thermography is the optimal NDT solution for other types of robotics sensor flaws. It reveals discrepancies in thermal conductivity, which can indicate surface flaws. More importantly for this use case, though, it can also reveal material degradation or electrical issues in a sensor.
3. Best NDT Methods for Robotics Circuitry
The wiring, transistors and other circuit components within a robot are sensitive. However, physical deformations are not the most common manufacturing error with these components, so they require different testing techniques. Generally, electrical resistance (ER) testing is the best NDT method for robotics circuitry.
ER analysis measures a subject’s ability to resist an electrical current. Consequently, it can identify metal loss from corrosion, reveal if resistors and transistors work correctly, and detect current loss in a circuit.
Most electrical problems will showcase an unexpected change in electrical resistance, making ER testing versatile enough for most PCB and wiring inspections. It is also relatively easy to perform, which is crucial when robotics manufacturers must achieve high output levels.
4. Best NDT Methods for End Effectors
Robotic end effectors are often less sensitive than sensors and circuitry, but they may also be more varied. While this component class differs widely depending on the robot’s use case, most examples benefit from NDT methods centered around determining material integrity.
Radiographic testing (RT) is often the best way forward here. This process uses X-rays or gamma rays to provide an image of the subject’s makeup, highlighting areas of varying density. Just as an X-ray helps doctors detect broken bones in humans, RT reveals material defects that may not be visible to the naked eye.
RT covers both surface and sub-surface flaws, offering a comprehensive look at an end effector’s structural integrity. It does carry some health risks — repeated exposure to ionizing radiation can increase cancer risks without proper protection — but these hazards are fairly easy to account for, and many RT processes are automatable.
5. Best NDT Methods for Complete Robots
Manufacturers must also consider NDT methods for robotic units after assembly. RT can again be of use here, especially when ensuring all wiring remains intact while connecting components. However, visual inspections are often sufficient if separate parts all underwent their own testing.
The key advantage of visual inspections is that they are fast and require minimal preparation, but companies should recognize that manual methods are too error-prone and slow for modern standards. While visual testing is sufficient for complete robots, it must use an automated process.
Machine vision is far more reliable than manual visual inspection, as it offers increased precision and does not entail risks from human error. It is also more efficient, with some systems tracking objects 1,000 times faster than human vision, enabling testing at the speed of production.
How to Identify the Best NDT Methods for Any Component
The key to choosing the right NDT methods for robotics components is understanding which types of flaws are most prevalent. Nearly all NDT techniques are suitable for sensitive systems, as they all involve no invasive procedures and minimal physical contact. The most crucial factor is what they detect.
Laser measurements and infrared inspections are fast, accurate ways to detect surface imperfections. By contrast, RT is better for identifying internal material flaws, and ER testing is more appropriate for electrical faults. No one technique is better than another in all scenarios, but each is superior in a given use case.
The Right NDT Method Depends on the Situation
Once manufacturers understand which types of defects to look for in each component, they can select the optimal NDT solution. Matching robotic parts to the ideal testing technique will ensure producers can uphold both efficiency and quality assurance goals. Doing so is critical to surviving the rising demands in the automation market.
Lou Farrell is the Senior Editor at Revolutionized, and has several years of experience covering cutting-edge topics in the fields of Robotics, AI, and Manufacturing. He enjoys writing more than almost anything else, and has an intense passion for sharing his knowledge with anyone he can.
Comments (0)
This post does not have any comments. Be the first to leave a comment below.
Featured Product
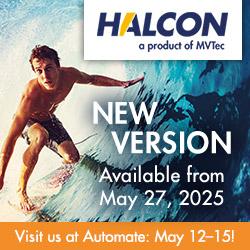