Tips for choosing the optimal lighting solution for a machine vision application.
Eight Tips for Optimal Machine Vision Lighting
Shaina Warner | Microscan
Proper lighting is critical to the success of a machine vision application, and should be the first consideration when setting up a system. A well planned lighting solution will result in better system performance and save time, effort, and money in the long run. This article presents the following tips:
1. Use Bright Light to Detect Missing Material
2. Use Appropriate Wavelength for Accurate Component Placement
3. Use Non-Diffused Light to Detect Cracks in Glass
4. Use Diffused Light to Inspect Transparent Packaging
5. Use Color to Create Contrast
6. Use Strobed Light for Rapidly Moving Parts
7. Use Infrared Light to Eliminate Reflections
8. Use Infrared Light to Diminish Color Variation
Before & After Correct Lighting
How Does Lighting Affect a Vision Application?
Machine vision systems rely on quality images for quality output. High quality images enable the system to accurately interpret the information extracted from an object under inspection, resulting in reliable, repeatable system performance. The quality of the image acquired in any vision application is highly dependent on the lighting configuration: the color, angle, and amount of lighting used to illuminate an object can mean the difference between a good image, resulting in good performance, and a poor image, yielding poor results.
Machine vision lighting should maximize feature contrast while minimizing contrast of the rest, thereby allowing the camera to clearly "see" the part or mark. High contrast features simplify integration and improve reliability; images with poor contrast and uneven illumination require more effort from the system and increase processing time. The optimal lighting configuration is dependent on the size of the part to be inspected, its surface features and part geometry, and the system needs. With a broad range of wavelength (color), field of view (size), and geometry (shape) options available, machine vision lighting can be tailored to specific application requirements.
Five Considerations When Choosing Lighting:
- Is the surface flat, slightly bumpy or very bumpy?
- Is the surface matte or shiny?
- Is the object curved or flat?
- What is the color of the barcode or mark?
- Are you inspecting moving parts or stationary objects?
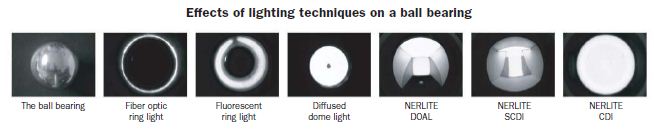
Tip #1: Use Bright Light to Detect Missing Material
Identifying “Short Shots” in Plastic Molding
Are your shots falling short?
Identifying missing material from plastic molding applications is important to ensure good sealing surfaces. When material is missing, you have a “short shot” condition (i.e. insufficient quantity of material injected into the mold). To identify short shots, a NERLITER DOALR (Diffuse On-Axis Light) illuminator is used to highlight missing material on the sealing surface.
Illumination Technique: Bright Field
The bright field lighting technique relies on surface texture and flat topography. Light rays hitting a flat specular surface reflect light strongly back to the camera, creating a bright area. Roughly textured or missing surfaces scatter the light away from the camera, creating dark areas.
Illumination Example:
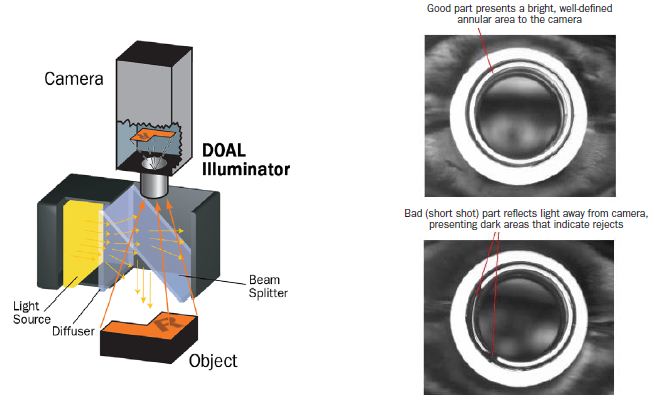
Tip #2: Use Appropriate Wavelength for Accurate Component Placement
Inspecting “Flipped Chips”
Are your chips flipped?
Identifying proper component orientation is a common machine vision application in PCB assembly. In this example, chips were incorrectly “flipped” in an automated assembly step. Instead of being placed onto the substrate with copper side down for proper electrical connection, the chip is flipped over, silver side down, causing component and assembly failure.
Illumination Technique: Bright Field
To identify problem assemblies, a NERLITER DOALR illuminator with a blue wavelength is used to highlight chip orientation. This lighting technique relies on wavelength and coaxial lighting geometry. The blue wavelength (460 nm) sharply differentiates the silver and copper surfaces: copper absorbs the blue light and appears dark, silver reflects the blue light and appears bright. The unique NERLITER coaxial lighting geometry eliminates the root cause of false rejects: unwanted
glare, reflections and dark spots.
Illumination Example:
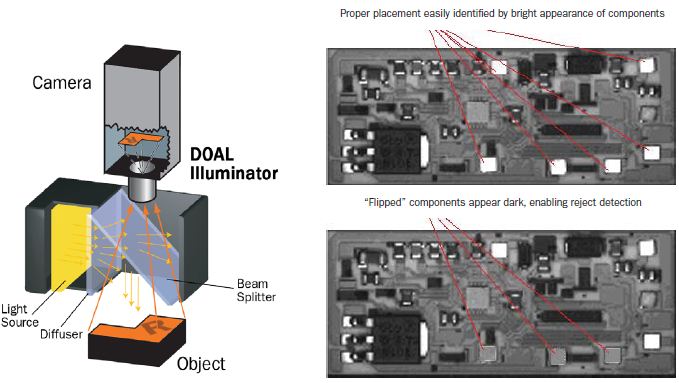
Tip #3: Use Non-Diffused Light to Detect Cracks in Glass
Detecting Cracks in Glass Containers
You’ve had your fill of glass defects
Detecting cracks during sidewall inspection of glass containers prior to packaged-goods shipment is an important way to minimize waste, decrease returns and increase consumer confidence. To detect cracks in transparent material, a NERLITER Area Array is used to highlight the imperfection.
Illumination Technique: Dark Field
In this application, dark field lighting is used to create a bright, easily detectable feature of interest within a dark background. Light rays are directed at the transparent bottle from a dark field region (i.e. from outside the camera’s field of view). Most of the rays pass through the transparent object undetected by the camera. If a material irregularity such as a crack exists, some light rays strike that irregularity. Cracks, in particular, create an internal void, where light rays refract and reflect, scattering in many directions including back to the camera. These are the rays that turn an otherwise difficult to detect crack into a bright
feature on the dark background.
Illumination Example:
Tip #4: Use Diffuse Light to Inspect Transparent Packaging
Verifying Contents of Blister Packs
What’s inside that blister?
Detecting missing, damaged and/or incorrect contents in the cells of blister packages is an important inspection step for ensuring the quality of finished pharmaceutical goods. Illuminating the packages to avoid reflections from cell coverings can often be a tough challenge. To present an accurate image of the cells and their contents to the machine vision camera, a NERLITER CDI® (Cloudy Day Illuminator) employing white LEDs is used. The CDI eliminates reflections from the clear cell coverings, making them virtually disappear, while at the same time providing a high contrast, neutral color view of the cell contents.
Illumination Technique: Continuous Diffuse
The continuous diffuse lighting technique de-emphasizes surface textures and changes in elevation. It provides a very large solid angle of illumination to guide light rays to the object from a multitude of angles, thereby eliminating the reflections and shadows typical of unidirectional or single-plane light sources.
Illumination Example:
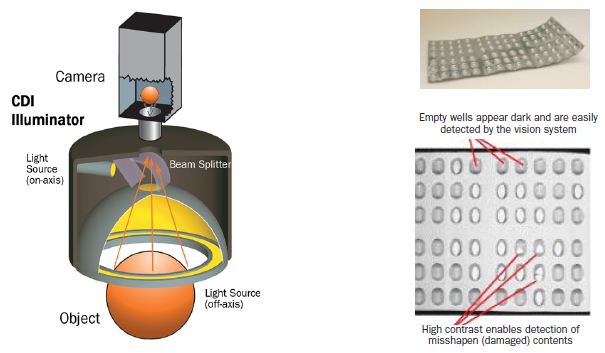
Tip #5: Use Color to Create Contrast
A useful method for creating a high contrast image in a machine vision application is to illuminate the object with light of a particular wavelength (color). A light’s wavelength can make features with color appear either bright or dark to the monochrome camera. Using the color wheel as a reference, choose light of an opposing color to make features dark; choose light of the same color to make features light.
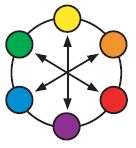
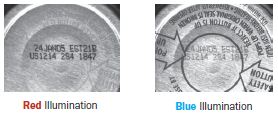
Tip #6: Use Strobed Light for Rapidly Moving Parts
A light should be strobed when a part is moving quickly and the image captured appears blurred. Use the formula on the right to calculate Strobe Pulse Width (maximum acceptable blur image = 1 pixel).
In the formula, field of view (FOV) and pixels are from the axis of travel. For example, assuming a typical 1 inch FOV and a 640 pixel frame, and a part speed of 500 inches per second, a strobe pulse width of 3.1 μs is needed.
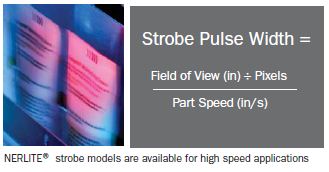
Tip #7: Use Infrared Light to Eliminate Reflections
Machine vision systems rely on transitions of gray levels in a digital image. In many vision applications, ambient light (i.e. overhead room lighting) sources contribute unwanted bright reflections that make it difficult or impossible for the vision system to detect the features of interest. An infrared (IR) light source can be used to eliminate this problem.
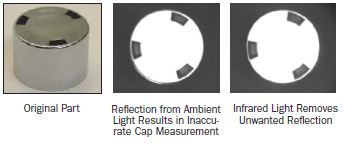
Tip #8: Use Infrared Light to Diminish Color Variation
Infrared light can be used to diminish the grayscale difference between colored objects. Dark objects absorb infrared light waves, thereby creating uniformity in objects of otherwise varying shades. This lighting solution facilitates detection of inconsistencies where color or shade variation is expected and should not affect inspection.
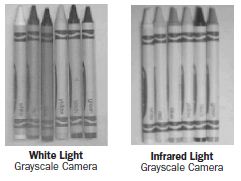
Machine Vision Lighting solutions from Microscan
Microscan’s innovative NERLITE® line of products is the longest established brand of machine vision lighting, enabling machine vision and auto ID systems to perform reliably in thousands of applications worldwide.
A global technology leader with extensive solutions for ID tracking, traceability and inspection, Microscan’s line of 1D and 2D barcode readers, machine vision systems, and machine vision lighting is backed by one of the world’s most robust patent portfolios and years of proven performance in the field. Supported by a highly skilled global integrator network, Microscan products are known and trusted by customers worldwide for their high precision and reliability in industrial automation and control applications, with solutions ranging from basic barcode reading to complex machine vision inspection, gauging, and measurement.
More information on Microscan is available at www.microscan.com.
The content & opinions in this article are the author’s and do not necessarily represent the views of RoboticsTomorrow
Comments (0)
This post does not have any comments. Be the first to leave a comment below.
Featured Product
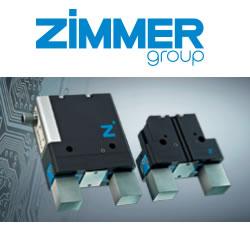
Zimmer Group - THE PREMIUM GRIPPER NOW WITH IO-LINK
IO-Link is the first standardized IO technology worldwide for communication from the control system to the lowest level of automation.