The new standard requires a risk assessment be accomplished when designing and integrating new robot systems and assigns responsibilities for them. The R15.06 and Z434 will also include an update of the popular risk assessment methodology offered in the existing standards.
New ISO Robot Safety Standards Published!
Jeff Fryman | Robotic Industries Association
For several years now, I have been informing you of the progress in the revision of the International Standard for industrial robot safety, the ISO 10218 standards. I am pleased, actually very pleased to announce that the ISO 10218-1 standard for the robot, and the ISO 10218-2 standard for the robot systems and integration were both published effective 1 July 2011. This is indeed a milestone accomplishment. A very dedicated group of international experts, robot, engineering and safety, have been meeting regularly since 2001 to produce this revision of the old 1992 standard. Speaking of the ISO team, they have not quit work, but have moved on to new deliverables for the safety of industrial robots. I will be reporting on this work in the future.
What does the publication of new ISO standards mean for the ANSI/RIA R15.06? The R15.06 drafting committee has been working in step with the ISO team to provide comments and input to the ISO standard with the goal of adopting the international standard as the basis for the next revision of the American National Standard. This means the basic language; the basic technical requirements are now set for the revised R15.06. Since the ISO standard only looks forward from the date of publication, the issues to be resolved by the R15.06 drafting committee have to do with any guidance for existing robots and robot systems, particularly those that do not meet the technical requirements of the 1999 edition of the standard. The unique requirements for the United States, mostly directed to the end user, must be added, and the added annexes updated.
One World; One Standard
We are pleased to announce that the R15.06 team in the U.S. and the CSA Z434 team in Canada have reached agreement on publishing a combined standard for industrial robot safety which includes the full requirements of the ISO 10218-1, ISO 10218-2, R15.06 and Z434. This globally harmonized document resolves differences between requirements in the U.S., Canada and around the world. One document valid world-wide!
The new standard will be significantly more comprehensive than the 1999 edition, and will introduce some exciting new technical capabilities for robots and robot systems that did not exist or were not feasible when the 1999 edition was written. The document has been rewritten and reorganized, but all of the basic safety requirements from the R15.06 and Z434 you have worked with for years are now global requirements. Currently compliant installations remain compliant with no need to make changes until you want to take advantage of new features, modify or move an existing cell.
What Changed?
Everyone is anxious about change and wonders what the changes in the standard may be. If I had to pick one notable change, it is about risk assessment. The new standard requires a risk assessment be accomplished when designing and integrating new robot systems and assigns responsibilities for them. The R15.06 and Z434 will also include an update of the popular risk assessment methodology offered in the existing standards. The new standard includes a lot more detail on what is expected in a risk assessment and what considerations need to be included. This is a direct acknowledgement that it is not practical to offer prescribed safeguarding requirements for every possible robot system design in an industry standard. Every work cell is different, and the detail requirements of the cell have to be individually reviewed. Through a comprehensive risk assessment, the proper safeguarding requirements can be determined and implemented to assure personnel safety in the work place.
What’s new?
I will pick two significant items that I think will enhance worker productivity while still delivering a reliable level of safety for the system. One is called safety-rated soft axis and space limiting. This is the enabling technology for the other – collaborative robot operation. The safety-rated soft axis and space limiting allows positive control of the robot location and thus the safety for the worker. It allows areas in the robot restricted space to be designated inclusive or exclusive by limiting the motion of the robot. Previous case studies presented about robot systems using this technology have suggested floor space savings on the order of 30% and cost savings $125K per robot system.
Collaborative robot operation reintroduces the “man-in-the-loop” in the production cycle of the robot system operation. The 1999 standard eliminated a feature called continuous attended operation. It was considered unsafe with the level of safety technology and sensors of the day. The last ten-plus years have seen a dramatic increase in safety technology, machine control and now safety-rated software. I had the pleasure of assisting in demonstrating the collaborative robot operation concept at the RIA booth at the Automate 2011 show in Chicago last March. I hope that you had an opportunity to observe that. In addition to improving productivity, the collaborative operation can save costs for fixtures. This is all impressive considering the improved level of safety provided to the worker at the same time.
Want to learn more? Please join us for our annual National Robot Safety Conference this in Knoxville, Tennessee, September 19-21, 2011. We have a complete program that highlights important features and requirements in the new standard presented by some of the key persons responsible for the new standard. More details on the conference, including sessions, tabletop trade fair, registration, hotel information and more, can be found at http://www.robotics.org/safety11 or call RIA at 734/994-6088.
I hope to see you in Knoxville! Until then, be safe.
The content & opinions in this article are the author’s and do not necessarily represent the views of RoboticsTomorrow
Comments (0)
This post does not have any comments. Be the first to leave a comment below.
Featured Product
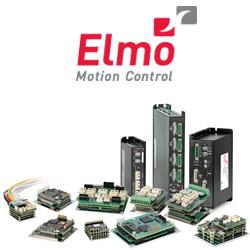