A robot has multiple axis, so a wireless switch is sensing position on those different axis. A Limitless™ wireless solution includes wireless switches and I/O devices that are paired and communicate with a PLC or controller interface.
Joseph Citrano III | Honeywell Sensing and Control (S&C)
What kinds of robotic manufacturing applications are moving away from cables and are adopting wireless?
Any robots that bend and flex and need position sensing. The value wireless brings:
- At the OEM level, it has the capability of simplifying design, resulting in a more reliable robot
- At the user level, wireless helps avoid downtime, maintenance and troubleshooting from broken cables
802.15.4 is one of the most common technologies used for industrial wireless networks. What is 802.15.4, what is its range, how does it handle robustness, security, interference, power demands, etc?
802.15.4 is designed to be a relatively low-power, low bandwidth wireless radio protocol yet it offers levers that provide the necessary flexibility to meet various application needs. Its range, security, and how it deals with interference has more to do with the appropriate use of these levers and the application layer built on top of 802.15.4. An example of a standard that uses these levers and uses a suitable application layer is the ISA-100 industrial wireless standard. Some of the levers include SSL-security encryption. Interference and robustness is managed through a variety of methods including time synchronized transmissions, frequency hopping and retries.
Are 802.15.4 devices compatible between different manufacturers?
Yes, 802.15.4 devices are compatible because 802.15.4 is an IEEE standard.
What are the three primary reasons that assembly lines are moving to industrial wireless networking?
- Easy configurability. No engineering is needed to change or reconfigure wire runs. This can be valuable especially in automotive manufacturing where the factory needs to reconfigure/retool every year.
- Cost, to save the cost of wiring sensors. When wire runs exceed 25 feet, the total installed cost of wireless is usually lower than comparative wired solutions.
- Downtime. Wireless eliminates downtime associated with replacing cables that are prone to breakage and failure, i.e., those that are subjected to flexing, high temperature, cutting, chemicals and other environmental challenges.
How long does it take to install a wireless network in a manufacturing environment?
Installation depends on the number of sensors and receivers to be installed and how complicated the application, but a small installation with one receiver and ten switches can be done in as little as a couple of hours. With a Limitless™ solution, you can pair ten wireless switches and one receiver in less than thirty minutes.
What are the cost savings as compared to a standard cabled installation?
It’s dependent on the cost of labor, whether it’s new construction or retrofitting and the length of cable run. We have a calculator that will show how in most cases, wireless is less expensive after 25 feet of cable, and installations where more than $10,000 were saved by using Limitless™ wireless solutions. This is only comparing installation costs, and doesn’t include the value saved from engineering time, less troubleshooting, and downtime from broken cables.
Can you give us an overview of the installation process and the typical devices that are required?
A robot has multiple axis, so a wireless switch is sensing position on those different axis. A Limitless™ wireless solution includes wireless switches and I/O devices that are paired and communicate with a PLC or controller interface.
What are the challenges faced by wireless networks operating in an industrial environment and how do Honeywell’s wireless solutions handle those?
-
Reliability
- IEEE 802.15.4 made-for-industrial-use radio
- Communication and battery diagnostics built in
- Security – 128 bit SSL security encryption, which is uncrackable by the world’s fastest super computers
- Able to be used without additional training – plug-n-play, omni-directional antennas work with no RF engineering required
- User-friendly – Automatic field pairing with no special software or tools required
- Rugged fit for tough applications – Robust, metal enclosures with IP 67 or better sealing and operating temperature range -40° F to 185 °F to handle the most rugged applications
- Low maintenance - Long battery life with easy replacement
- Expense - Commercially available replacement parts – little to no training required to use the product
Are special skills required to maintain a wireless network or is the system plug and play?
The system is as close to plug-and-play as it can get. It’s very similar to setting up blue tooth headsets and mice for computers. The system is designed to be virtually maintenance free and no engineering degree is required to maintain the system. The battery is the only thing thing that needs to be maintained, and the user gets a two to four week notice of a low battery on the receiving side. Other than that, there is little to maintain.
What’s next in wireless robotic system technology?
As the awareness and confidence in wireless grows, we expect to see an ever increasing utilization of wireless alternatives to traditional control and power cabling. The savings from avoiding downtime and ease of installation are driving market acceptance.
About Joseph Citrano III,
Global Product Manager for Honeywell Sensing and Control (S&C)
Joseph Citrano III is a Global Product Manager for Honeywell Sensing and Control (S&C). In this role, Joseph is responsible for S&C’s wireless switch and sensor product line, driving integrated product and technology roadmaps, program vision and leading new product introduction efforts. He develops global execution and go to market plans, identifying potential technologies and strategic direction.
Joseph has 15 years experience in product marketing, with extensive experience in the oil and gas, automation systems and sensing and control industries. Joseph holds a bachelors of science degree in chemical engineering from Rutgers University.
The content & opinions in this article are the author’s and do not necessarily represent the views of RoboticsTomorrow
Comments (0)
This post does not have any comments. Be the first to leave a comment below.
Featured Product
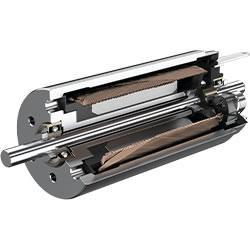