Carbon nanotubes hold great promise for more efficient robotic muscles as well prosthetics. There are many other technologies that will benefit from carbon nanotubes, including nanotechnology, electronics, optics, and architecture because of their exceptional electrical properties, astonishing strength and effectiveness in heat conduction.
Len Calderone for | RoboticsTomorrow
Advanced robotic muscles are made from nanotech yarns and infused with paraffin wax. These robotic muscles can lift 100,000 times their own weight and generate 85 times more power than the same size human muscle. Made from layers of graphite similar to what is found in pencils, the artificial muscles are comprised of carbon nanotubes, which are seamless hollow cylinders. Pound-for-pound, nanotubes are stronger than Kevlar, yet flexible and lightweight, being 10,000 – 50,000 times smaller than a human hair.
Photograph: Alamy
Yarns woven from carbon nanotubes can contract like muscles at extremely high speeds to lift large weights. These artificial muscles can be utilized as actuators in robots, and powered by electricity, light or some chemicals.
Researchers grow a forest of vertically aligned carbon nanotubes in a chemical reactor. Then they drag a roller over the nanotubes, which separate from the surface and get tangled up in a long nanotube web. The researchers spray the surface of the web with a powder and then twist it into a yarn. The powder is restricted to the inside of the spirals of the nanotube web, resulting in yarns that are 95 to 99 percent powder by weight.
A mixture of powdered boron and magnesium is used to make superconducting yarns by a simple process. The conventional process for making superconducting wires involves packing the powders in copper tubes and heating and drawing them multiple times to stretch them into wires. But the superconducting yarns are heated just once to anneal the powders and form a superconducting thread.
The University of Texas at Dallas twist-spun nanotube threads together, which increased their collective strength a thousand fold. The technology is like spinning wool, which mankind has been doing for centuries.
Ray Baughman at UT created artificial muscles by adding wax, such as paraffin, to the threads and twisting them to the point that they coil. The coiling process is similar to what rubber bands go through on a rubber band airplane. If the propeller is rotated, the twist turns to coiling. This coiling amplifies the yarn’s ability to expand and contract by a factor of 10.
The yarn will contact and expand on its own when exposed to super high temperatures; and the wax helps the yarn perform at temperatures that are not extreme, as the wax can be easily melted. The wax turns into a liquid, when an electrical current is passed through the yarn, causing the yarn to contract. When the current is turned off, the yarn will expand. This is similar to how a human muscle acts.
To develop a single yarn actuator into a large actuator, in which hundreds of individual yarn muscles operate in parallel, is a challenge for the future. Because of their simplicity and high performance, these yarn muscles could be used for applications in robots, as they are not yet viable for use in humans.
It just takes 25-thousandths of a second for a muscle made from nanotubes to contract or reverse. The contractile power density of 4.2 kW/kg has been proven. This is four times the power-to-weight ratio of common internal combustion engines.
The human muscular tissue is similar to nanotube yarn technology. The muscular tissue exhibits a unique property called contractibility. It is the capacity of the cells to exhibit regular contractions and relaxations. Hence, it is also known as contractile tissue.
If we look at a human muscle, the construction is similar to nanotube muscles in that a human muscle cell is made up of many myofibrils, just as an artificial muscle is comprised of many nanotubes. A human muscle is further made up of muscle cell bundles. Nanotube yarns will be bundled in a similar fashion.
The human skeletal muscular system is capable of contracting longitudinally in response to nervous stimulation. The muscle cells contain small contractile strands of protein (myofibrils). They contract when stimulated, returning to their original state as soon as nervous stimulation ceases.
To understand how robotic muscles need to work, it is important to understand that most muscles of the human trunk & extremities are arranged in opposing muscles. When one muscle (prime mover/agonist) is contracting to achieve a desired movement, its opposite muscle (the antagonist) is being stretched.
The function of a robotic arm works on the same principle of the agonist-antagonist muscles. The robotic arm is taught coordinates by using a learning mathematical algorithm to measure the corresponding pressures on the actuators to the visual input received from the robot’s cameras. The agonist is the primary muscle used for motion at a joint. The agonist muscle contracts to create movement. The antagonist muscle does the opposite motion of the agonist muscle.
The robotic arm needs to supply the correct grip. Feedback encoders can be used to provide data to the robot’s brain to establish an approximate gripping pressure. Current is set on the valves controlling the robotic grips based upon the feedback data.
Of course, we have the problem of powering our humanoid robot and its muscles, since these robots must work with humans and be capable of continuous operation for many hours without running out of energy. Presently, battery technology is not up for this kind of operation unless the power consumed by a robot is greatly reduced. Their muscles do not work without power to them.
One way to power the robot is to use super capacitors that use carbon nanotubes to increase the charge capacity simply by increasing surface area. If researchers can get lithium-ion batteries to charge in minutes or even seconds instead of hours, the robot might only need short breaks to recharge.
We might not be able to send a miniature submarine into a patient’s bloodstream like they did in the movie, “Fantastic Voyage,” but by utilizing nanotube muscles, doctors might be able to send tiny nanobots to diagnose and treat medical conditions.
With the development of carbon nanotube muscles that are small and strong, nanobots can be pushed through a patient’s bloodstream by mimicking the flagella of bacteria on the back of these tiny swimming robots. These nanobots can deliver drugs, remove parasites and fight cancer.
Carbon nanotubes hold great promise for more efficient robotic muscles as well prosthetics. There are many other technologies that will benefit from carbon nanotubes, including nanotechnology, electronics, optics, and architecture because of their exceptional electrical properties, astonishing strength and effectiveness in heat conduction.
Will Olympic weightlifting contests for robots be far behind?
For additional information:
About Len
Len has contributed articles to several publications. He also writes opinion editorials for a local newspaper. He is now retired.
This article contains statements of personal opinion and comments made in good faith in the interest of the public. You should confirm all statements with the manufacturer to verify the correctness of the statements.
The content & opinions in this article are the author’s and do not necessarily represent the views of RoboticsTomorrow
Comments (0)
This post does not have any comments. Be the first to leave a comment below.
Featured Product
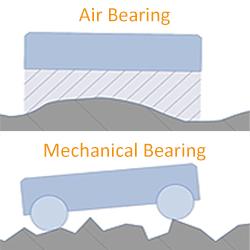