OCTOPUZ was created to meet the rising needs in the robotics industry, and uses a revolutionary method of combining offline programming of robots with manufacturing process simulation.
Contributed by | In-House Solutions
If one robot can save your company time and money, just imagine what four can do!
Tech-Con Automation, an automation solutions company in Burlington, Ontario, recently programmed and simulated a waterjet cutting cell using Yaskawa Motoman robots and OCTOPUZ, the offline robotic programming software developed by In-House Solutions.
The video shows four HP20D robots, equipped with waterjet cutting heads and operated by an NX100 controller, cutting out carpets for the inside of a car. The simulation was programmed in just hours rather than days using a single CAM file with all tool on/off commands from OCTOPUZ and multiple user frames. The four simultaneously-moving robots were collision-checked against each other and their surroundings, avoiding any unpredictable motions or collisions ahead of time.
“Being able to see a simulation of the waterjet cutting cell in action convinced us that we could not only increase our efficiencies but be aware of any potential issues before going into production,” said Rick Bobzener, GM of Applications.
OCTOPUZ was created by In-House Solutions to meet the rising needs in the robotics industry, and uses a revolutionary method of combining offline programming of robots with manufacturing process simulation.
Here are a few reasons why an increasing number of companies are making OCTOPUZ part of their automation solutions:
-
Programming time is much faster.
-
Robot can still operate and generate revenue while the next part is being programmed.
-
Collisions and unpredictable motions can be avoided ahead of time, resulting in substantial savings in time and money.
-
Complex paths can be made using any CAM system.
-
The tool set can be positioned perpendicular to the surface if possible.
OCTOPUZ is the intelligent offline robotic software ideal for any path-sensitive application. To learn more about OCTOPUZ or to request a free personalized software demo for your application, visit www.octopuz.com.
About OCTOPUZ
OCTOPUZ is an intelligent offline robot programming and simulation software ideal for any path-sensitive application. Created by In-House Solutions, the company took a revolutionary approach by combining the offline programming of robots with a manufacturing process simulation. Today, OCTOPUZ provides a mainstream, versatile, powerful and effective solution for any robotic challenge.
About In-House Solutions
More than 27 years ago, In-House Solutions (www.inhousesolutions.com) began reselling and developing powerful software tools accessible to small- and medium-sized manufacturers. Today, the company provides CAD/CAM, DNC, PCMM and OCTOPUZ robotic programming software solutions to organizations of all sizes. The In-House Solutions team of experts, with offices in the U.S., Canada and Germany, are dedicated to selling, supporting, developing and implementing a full spectrum of software tools, particularly those specializing in NC programming and optimization, shop floor DNC communications and offline programming of industrial robots. In-House Solutions is the Canadian Mastercam distributor, and OCTOPUZ completes the company’s software solutions for manufacturing.
The content & opinions in this article are the author’s and do not necessarily represent the views of RoboticsTomorrow
Comments (0)
This post does not have any comments. Be the first to leave a comment below.
Featured Product
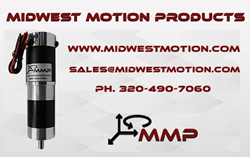