Pioneering an inherently safe solution for automating small parts assembly with human coworkers by redefining human-robot collaboration through a unique integration of components, speed, agility and motion control
Phil Crowther | ABB Robotics
Few production arenas are changing as quickly as small parts assembly. The electronics industry, in particular, has seen demand skyrocket past the supply of skilled labor. As conventional assembly methods diminish in value, manufacturers are finding it strategically and economically imperative to invest in new solutions.
ABB’s market introduction of the YuMi dual arm robot is a groundbreaking solution for human-robot collaboration in the small parts assembly environment. YuMi is “you and me” – creating an automated future together.
YuMi literally removes the barriers to collaboration by making fencing and cages a thing of the past. Its design is based on a revolutionary integration of motion control software, speed-limited hardware, reduced weight, a compact frame and 14-axis agility. The lightweight, padded, magnesium arms can stop the robot‘s motion in milliseconds if necessary (for instance, in the event of an unexpected collision). The com- bined effect of these features is to ensure the safety of human coworkers on production lines and in fabricating cells. In addition to its inherent safety, YuMi is a highly efficient and proficient robot – two qualities that accelerate its return on in- vestment. ABB has designed YuMi to become productive very quickly as an all-in-one solution, with integrated arms, hands, torso, control technology and parts feeding system.
A growing need and opportunity
In designing YuMi, ABB Robotics had the benefit of a bird’s- eye view of manufacturing trends in 53 countries, many with high-growth forecasts for electronics such as those in north Asia. Foremost among these trends is the rapid merging of consumer, computer and communication devices (3C conver- gence). This has led consumers to expect constant innovation at affordable prices, further straining production processes.
For manufacturers, the market has changed the rules in ways that can be addressed effectively only by automation. The “new norm” of small parts assembly is higher product volumes, shorter product lifecycles, shorter lead times and a growing trend to customize goods – particularly electronics – close to final markets. From a human perspective, manufacturing’s role in job creation is also changing as companies invest in process improvements that allow them to compete more effectively. The rapid rise of smart electronics has increased the demand for highly skilled production workers capable of consistent precision. This impacts every industry that incorporates small, sensitive parts into its end products.
With the shift in skill levels comes an increase in labor con- cerns: labor pool limitations, workforce management costs, compensation and retention. Even in countries with low- priced labor, human-robot collaboration compares favorably to the total cost of an all-human workforce. Collaboration is proving to be instrumental in raising throughput, reducing waste and taking humans out of harm’s way.
YuMi solves the full scope of these challenges with techno- logy that will carry manufacturers well into the future. YuMi’s inherent safety means that the delicate, dull, dirty or dan- gerous jobs in small parts assembly can be given to the robot, making people essential for the performance of jobs requiring cognitive and technical skills that robots will never master.
Collaborative: Friendly in appearance and operation
Intentionally designed to resemble its human counterparts, YuMi has a compact body that requires no more space than a human workstation. Its dual magnesium arms each flex on seven axes to move in human-like fashion without entering a coworker’s space unless required too. YuMi operates equally effectively side-by-side or face-to-face with its human co- workers, and in addition:
- Its inherently safe design is intended to eliminate the need for fencing, caging or other barriers.
- Its hands (the servo grippers) can easily locate and then direct the grippers to pick parts.
- Real-time algorithms set a collision-free path for each arm, customized for the required task.
- Padding protects coworkers by absorbing force if, in the unlikely event, contact is made.
- If the robot encounters an unexpected object – for example, the slightest contact with a human coworker – YuMi can rapidly diagnose the change in its environment and, if necessary, register the overload, shutting down the motion within milliseconds to prevent injury.
- Pinch points, locations on the robot where fingers and other ancillary parts could be damages as axes move and gaps open and close, have been largely eliminated on YuMi by design to encourage close collaboration and remove one additional hazard to human safety.
Productive: Versatile and easy to deploy
YuMi performs jobs in small parts assembly and is capable of handling anything from a watch to a tablet PC with the level of precision that could thread a needle. Further, the robot’s extreme versatility – a function of its size, weight, flexibility and ease-of-programming – enables it to adapt to changes in the production environment in much the same way a high-value employee does, by quickly repositioning and learning new tasks. It will radically change the way the industry thinks about assembly automation.
Conclusion
In bringing YuMi to market, ABB Robotics has harnessed the enormous potential of human-robot collaboration in small parts assembly. YuMi offers manufacturers a transformational new solution, the first dual arm robot purpose-built for the small parts space: inherently safe, extremely accurate, and fiercely protective of its human coworkers. While designed specifically for the electronics industry, YuMi is also well suited to other small parts environments, including the manufacture of watches, toys and automotive components. These end-markets have been changing faster than the pro- cess improvements they demand – until now. About ABB Robotics ABB (www.abb.com) is a global leader in power and automation technologies that enable utility, industry, and transport and infrastructure customers to improve performance while lowe- ring environmental impact. As part of the Discrete Automation and Motion division of ABB Group, ABB Robotics is a leading supplier of industrial robots, modular manufacturing systems and related services. ABB Robotics has installed more than 250,000 robots worldwide to help companies improve productivity, product quality and worker safety.
About ABB Robotics
ABB Robotics is a leading supplier of industrial robots - also providing
robot software, peripheral equipment, modular manufacturing cells and service for tasks such as welding, handling, assembly, painting and finishing, picking, packing, palletizing and machine tending. Key markets include automotive, plastics, metal fabrication, foundry, electronics, machine tools, pharmaceutical and food and beverage industries. A strong solutions focus helps manufacturers improve productivity, product quality and worker safety. ABB has installed more than 250,000 robots worldwide.
The content & opinions in this article are the author’s and do not necessarily represent the views of RoboticsTomorrow
Comments (0)
This post does not have any comments. Be the first to leave a comment below.
Featured Product
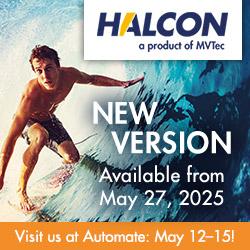