If the robot is not sure whether it can complete the task—for example if the part is "buried" within the bin—it takes pictures of its situation and calls a remotely located human (the "human on call") for help.
S.K. Gupta | University of Maryland A. James Clark School of Engineering
Like a driver who refuses to ask for directions when lost, today's industrial robots don't know when they're in trouble and should stop and get help—which limits their usefulness in manufacturing.
Now University of Maryland Professor S. K. Gupta and his students have developed RoboSAM (ROBOtic Smart Assistant for Manufacturing), an industrial robot smart enough to know when something is wrong, to pause and to call a human for help.
Currently, industrial robots are used mostly for high-volume, reliably repetitive tasks with unchanging, tightly proscribed parameters, such as automobile assembly lines. These robots are custom-built and programmed specifically for the tasks at hand. While they excel in such environments, the robots have a limited ability to assess whether they can successfully complete tasks. The robot doesn't know it should stop what it's doing if, for example, the parts it needs are not in the exact position it expects. A chaotic mess can result—one which humans must then fix.
That's why industrial robots are not used in factories where high task reliability cannot be ensured. Gupta, a professor in the A. James Clark School of Engineering, believes a better economic model would be to give robots the ability to assess whether they can successfully complete a task, and if they sense they cannot, to stop and ask a human for help.
His new RoboSAM, based on the Baxter industrial robot platform, is able to estimate the probability it can complete a task before beginning it, and can ask a "human on call" for help if necessary. RoboSAM's abilities may provide a path forward towards smarter, more versatile industrial robots and more interesting duties for the humans who work with them.
Gupta's team has successfully demonstrated RoboSAM in a "bin picking" situation. The robot needs to find a desired object in a bin of similar objects, pick it up, and deliver it to another area in a specific placement. If the robot is not sure whether it can complete the task—for example if the part is "buried" within the bin—it takes pictures of its situation and calls a remotely located human (the "human on call") for help. The human then suggests to the robot what it should do to complete the task, such as stir the contents of the bin, then try again to locate the needed part.
Gupta believes this work is the beginning of providing a better economic model for deploying robots, especially for small- and medium-sized manufacturing companies. "In most situations, providing task assistance help to robots is much more cost-effective than recovering from a system shutdown, and it enables humans to move from doing dull tasks like monitoring and clean up to more challenging work like helping robots with the tasks with which they struggle."
This research is funded by the National Institute of Standards and Technology and the National Science Foundation. Gupta holds a joint appointment in the Department of Mechanical Engineering and the Institute for Systems Research, and is the director of the Maryland Robotics Center.
The content & opinions in this article are the author’s and do not necessarily represent the views of RoboticsTomorrow
Comments (0)
This post does not have any comments. Be the first to leave a comment below.
Featured Product
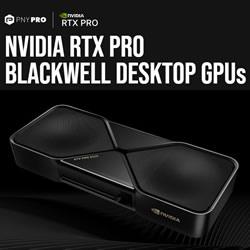