Short-term, robotic integration will continue to grow as companies continue to establish automation plans, and long-term, robotic automation will be a standard in every facility. This will be a requirement for companies to compete in the global marketplace.
Thomas R. Cutler
Manufacturing journalist Thomas R. Cutler recently interviewed Steven Hogg, Inside Applications Engineering Manager at Bastian Robotics, a division of Bastian Solutions. With fifteen offices globally, Cutler wanted to understand how the manufacturing and distribution sectors are responding to the dramatically increasing demand for robotics solutions.
Hogg noted that most end-users are typically aware of industrial robotics and the various applications within their facility where they can be applied. Many of Bastian’s customers understand the long-term benefits associated with robotics and have developed a strategic plan for robotic automation within their facility. This knowledge is driven by the large volume of information, case studies, and content available through different media outlets.
The information media sources, including Robohub, have done an effective job profiling the overall advantages of robotics technology. According to Hogg, where there is a distinct approach in presenting the efficacy of the robotics solutions in material handling often includes 3D renderings and simulations of the proposed solution. These tools help outline the process flow of the automation and highlights the key areas of process improvement. It is a powerful message delivered to the customer, when you can show a robot handling their product and verify the solution can meet their project objectives. In addition to providing the customer with a great visual aid of the system, these renderings and simulations are utilized throughout the lifecycle of the project. The simulation allows you to do robotic programming in a 3D virtual environment while the renderings are converted to 3D human machine interfaces for advanced system diagnostics and ease of use by operators.
Hogg added that the greatest resistance to change from fixed automation occurs when the company does not have any robots at their facility and have not developed a long term plan for automation and process improvement. He added when the warehouse or distribution center has an established programming architecture that technicians have utilized throughout their facility, the introduction of new technology into the facility is frequently met with resistance. In these cases, it is pivotal to educate the end-user on the programming structure provided and supply training to the technicians that will be operating the system. Many times the diagnostics of the system can be displayed on the HMI and very little interaction with the robot controller is necessary to operate the system.
Hogg acknowledged there is a willingness within material handling regarding robotics because many times conventional fixed automation lacks the flexibility required to adapt to changing market conditions and the development of new product lines. That said what is driving the receptivity of robotics in materials handling environments is the demand by management for increased productivity and quality metrics. Hogg also noted that given the propensity of workers' compensation claims in this environment there is a strong push for improved ergonomics and safety.
Vision Systems Driving Robotics Flexibility in the Materials Handling Arena
Cutler asked Hogg how robotics developers can address the needs of these challenges. Hogg noted that advancement in vision systems have brought robotics to a whole new level of flexibility. Before vision systems, robotics relied on static programming and force feedback to determine product location. With 2D and 3D vision systems, the robots are given sight to determine the location of the product as the vision guidance system captures images from a static or dynamic position to perform its analysis. The end result is the coordinates of the product position (x, y, z) and orientation (roll, pitch, and yaw angles). Mobile robotics have provided even more flexibility to industrial robots to allow for movement between interaction zones while providing alternative layouts and space planning.
Companies like Bastian Robotics have shared with their global clientele that the use of high precision servos and error proofing vision systems allow end-users the ability to maintain high system uptime while monitoring for quality issues in production. The collaborative robot movement has allowed robots to work side-by-side with human operators. This level of collaboration has helped break the stereotype that robots are not safe by removing the physical barrier and allowing the two groups to work together. When determining the safety requirements and whether a collaborative robot is necessary, a risk assessment should be performed to identify potential areas of risk within the work cell. At each stage of the assessment, individual safety requirements will be identified and the appropriate guarding and safety devices are determined in order to reduce the potential hazards. These requirements should be based off of OSHA and ANSI/RIA R15.06-2012 safety standards.
Given the growing market for industrial robotics, too many system integrators in this sector are now attempting to create one stop shopping for the materials handling distribution center yet have too little robotics experience. Hogg shared that having designed and installed hundreds of successful robotic systems, Bastian has established a proven method for robotic system integration and leverages over 60 years’ experience in the material handling industry. Bastian continues to push the boundaries of robotic integration through the company's R&D program, where they engineer custom end-of-arm tools, advanced controls and equipment design to provide a full robotic turnkey system solution.
Looking Ahead
Hogg shared with Cutler that short-term, robotic integration will continue to grow as companies continue to establish automation plans, and that long-term robotic automation will be a standard in every facility. This will be a requirement for companies to compete in the global marketplace.
About Thomas R. Cutler
Thomas R. Cutler is the President & CEO of Fort Lauderdale, Florida-based, TR Cutler, Inc., (www.trcutlerinc.com). Cutler is the founder of the Manufacturing Media Consortium including more than 6000 journalists, editors, and economists writing about trends in manufacturing, industry, material handling, and process improvement. Cutler authors more than 500 feature articles annually regarding the manufacturing sector. Cutler is the most published freelance industrial journalist worldwide. Cutler can be contacted at trcutler@trcutlerinc.com and can be followed on Twitter @ThomasRCutler.
About Steven Hogg
Steven Hogg is an Inside Applications Engineering Manager at Bastian’s robotics division in St. Louis, MO. Hogg has been with Bastian Solutions for nine years working to generate project-winning material handling system concepts. He has worked closely with VARs, consultants, and end-users directly to develop standard quote template documents that are simple to use and highly organized. These documents allow the sales force to provide quotes faster and with a higher degree of professionalism.
The content & opinions in this article are the author’s and do not necessarily represent the views of RoboticsTomorrow
Comments (0)
This post does not have any comments. Be the first to leave a comment below.
Featured Product
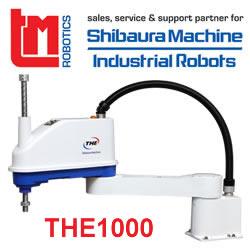