The electroadhesive clutch is a general-purpose clutch for exoskeletons, offering increased functionality while being lightweight and consuming very little energy.
What is an Electroadhesive Clutch?
Steve Collins | Experimental Biomechatronics Laboratory at Carnegie Mellon
Please tell us a bit about yourself and the projects you are working on?
My name is Steve Collins and I am an IEEE member and associate professor of mechanical engineering at Carnegie Mellon University. I direct the Experimental Biomechatronics Laboratory.
The main goal of my lab is to develop robots that you can wear on your leg to help you get around more easily. We have developed technologies for rehabilitation, where we try to help people relearn to walk after they have had an injury, and for assistance for a permanent disability like amputation, and for augmentation to enable people without disabilities to increase maximum performance.
What is the electroadhesive clutch and spring and what new elements does it use to conserve user energy and to enhance mobility?
The electroadhesive clutch is a general-purpose clutch for exoskeletons, offering increased functionality while being lightweight and consuming very little energy. It is three to 30 times lighter than other clutch mechanisms with the same holding force; it consumes 340 to 750 times less energy compared to previous devices; and it operates at four to 20 times lower voltage than previous electrostatic components in robots.
It works by electrostatic adhesion. A layer of Luxprint® (an insulating material) separates two sheets of aluminum-coated Mylar®, allowing a strong electric field to develop when voltage is applied. The electrons on one side are attracted to the protons on the other, causing the sheets to stick together and preventing sliding. The charge can develop quickly, and power consumption is low because the electrons don’t flow across the Luxprint®. When the voltage is removed, the electrons equalize and the coated Mylar® sheets just slide against each other.
This leads to a lightweight, low-power clutch that can engage and disengage quickly, setting the stage for devices with many clutches acting together.
What are the benefits in functionality that your electroadhesive clutch is providing, specifically to the disabled community and those undergoing rehabilitation?
We hope that in the near future it will result in lighter, more compact, and more affordable exoskeletons for rehabilitation and assistance to people in these communities. When many of these clutches are used together in an exoskeleton, they can offer the wearer selectable stiffness, which means that the level of assistance could change depending on the wearer’s task (such as walking up a hill or carrying a bag).
What are the current applications of mobile exoskeletons that you see in the industry today and where may we find them being implemented in the future?
Exoskeletons are currently used by factory workers to enhance strength or reduce fatigue. We expect exoskeletons to be used in hospitals for rehabilitation therapies, by older people and people with disabilities to get about more easily, in recreational athletics, in industry to enhance performance at manufacturing or distribution tasks, and in the military. Probably there are many creative uses of exoskeletons that we haven't yet thought of.
Are the major advances in robotics based on hardware or software at the current time?
Both. We need new hardware, particularly actuators, to improve the performance and affordability of exoskeletons compared to traditional designs based on electric motors and hydraulics. We need improvements in software that encode the functionalities that are actually beneficial to the human user, which remains the primary intellectual challenge in the field. Human-in-the-loop optimization of exoskeleton control appears particularly promising in this regard.
Are there any unusual applications for robotics that haven’t been introduced or talked about yet? Are the possibilities limitless or is there a ceiling on how far robotics can go?
The possibilities are limitless.
About Steve Collins
Steve Collins is an IEEE member and Associate Professor in the Department of Mechanical Engineering and the Robotics Institute at Carnegie Mellon University. He is director of the Experimental Biomechatronics Laboratory, organizes the CMU Bipedal Locomotion Seminar, and teaches courses on Design and Biomechatronics. Professor Collins uses a combination of mathematical models, experimental robots and biomechanics experiments to aid the design of biomechatronic devices for human rehabilitation, assistance, and augmentation.
The content & opinions in this article are the author’s and do not necessarily represent the views of RoboticsTomorrow
Comments (0)
This post does not have any comments. Be the first to leave a comment below.
Featured Product
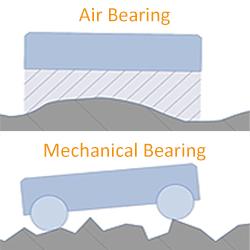