The feeding system can handle parts smaller than 0.1 mm and up to 10 mm in size.
Asyfeed Pocket Module Feeding System Handles Swiss Watches' Most Delicate Parts
Contributed by | Asyril
For years, specially trained employees at Swiss watch part supplier Affolter SA underwent the tedious task of manually handling a large variety of highly precise parts designed to operate some of the world’s best watches. The work was monotonous but necessary. Enter the Asyfeed Pocket Module by Asyril SA—an integrated flexible feeding module that updates the part-loading/machine-tending process of a traditional polishing machine. The result? Increased production flexibility and a gain of one to two seconds over manual cycle time, not to mention elevated employee morale.
How does the feeder handle such intricate parts without inflicting damage? The parts to be polished are fed in bulk into the hopper of Asyril’s Asycube 50 robotic parts feeder, which is integrated into the Asyfeed Pocket Module. They land on Asycube 50’s vibration platform, where Asyril’s 3-axis vibration technology goes into action, gently bouncing them so that they quickly separate. Illuminated by a backlight, the vision system detects the correctly oriented parts and sends the part coordinates to the module’s built-in, highly precise delta robot. Once the processing operation is complete, the robot removes the part and the cycle restarts with the next preoriented part.
Asyril’s Asyfeed Pocket Module is ideal for system integrators looking for an easy-to-integrate feeding system capable of supplying a large variety of products and materials. The feeding system can handle parts smaller than 0.1 mm and up to 10 mm in size. The Pocket Module is the perfect solution for automating any feeding, sorting, and palletizing tasks.
The content & opinions in this article are the author’s and do not necessarily represent the views of RoboticsTomorrow
Comments (0)
This post does not have any comments. Be the first to leave a comment below.
Featured Product
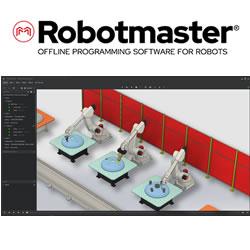