There are 4 possible scenarios for collaboration between user and robot. The bottom line is that in truth the only safe way to work with a robot is to guard it.
Collaborative Robots and Robot Safety
David Sands | ST Robotics International
When you consider the number of robots in the world – 8.6 million – the safety record of these robots is exemplary. Over 30 years there have been 27 robot deaths in USA and probably 50-60 worldwide. The last death by robot appears to have been a worker in a Volkswagen car factory in Germany in 2016. He got trapped by a robot and crushed against a metal plate. At a time when the robot population is increasing at a quarter of a million a year we should not be complacent. I see the advent of so-called collaborative robots as potentially relaxing standards and ignoring the dangers. Quite a lot of robots are being installed lately without any guarding, working next to or with human workers and declared safe because they have the ability to stop on impact with a human worker.
Most robot deaths have been caused by robots that are very strong and have crushed someone directly or placed something very heavy on a human worker. A lot of robots are being installed now that may not be so strong but happen to be very fast. Newton's first law of motion tells us, simply, that the robot cannot stop dead; it has to decelerate which takes time and distance. If a human being is trapped in that distance even a bench top robot can injure.
There are 4 possible scenarios for collaboration between user and robot. ST Robotics has 3 possible solutions:
1. The ST Robotics' 'Sentry' system is a module that sends out 3 IR beams across the workspace. The distance sensed by the module is adjustable and 2 or more can be used to guard the whole workspace. If a human user reaches into the workspace the robot stops.
2. There are some situations where the user and the robot must both have access to the same space, for example the user may want to place an item in a fixture that the robot subsequently accesses to remove the item. That is not a problem if the robot is stationary and waiting for the area to clear, and the Sentry module can work like that.
3. There may also be situations where the user must access the workspace while the robot is still moving, perhaps in another part of the workspace. The user's presence would then stop the robot which might not be what you want. The Sentry module can be temporarily disabled in the program to permit this to happen. The danger then is when there is some misunderstanding and the robot comes to the shared space while the human is still there perhaps with his/her hand while the Sentry is disabled. For this situation ST has a variant of the Sentry that mounts on the end of the robot. The drawback with this approach is that the sensor senses anything at all, not just a human hand. The sensing range has to be very close if the robot is not to be shut down just by getting close to, say, a fixture or item to be picked up.
4. So for this final scenario the ideal is a sensor mounted on the end of the robot that detects only human presence. For this case a number of robot manufacturers use capacitive sensors fitted to their standard robots for collaborative work. ST Robotics approach is a sensor fitted to the robot hand that senses a change in the electric field caused by the proximity of a human being. This is usually a human hand of course. There still exists a hazard from the rest of the robot arm if a person is determined to put his/her fingers where they should not be.
The bottom line is that in truth the only safe way to work with a robot is to guard it. However options 1 and 2 above are practical where true collaboration is required.
The content & opinions in this article are the author’s and do not necessarily represent the views of RoboticsTomorrow
Comments (0)
This post does not have any comments. Be the first to leave a comment below.
Featured Product
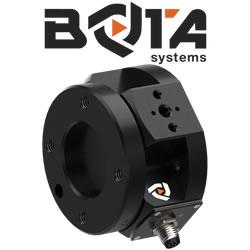