If robots are capable of rapidly adjusting their dampness, stiffing and dynamics, like octopi are, the added flexibility can make for more versatile robotics than ever.
This New Kind of Robot Mimics Octopus to Change From Rigid to Soft
Kayla Matthews | Productivity Bytes
Octopus muscles and joints are a point of focus for researchers from the Harvard John A. Paulson School of Engineering and Applied Sciences (SEAS) and the Wyss Institute for Biologically Inspired Engineering. Specifically, researchers are studying how to mimic an octopus' use of elbows, applying it to robotics.
Octopi contract muscles in their tentacles to create temporary revolute joints, which limit their arms' wobbliness and allow for more controlled movements. The temporary revolute joints lead to more precise actions, which aid in processes like grabbing food.
These researchers have interest in mimicking octopus' kinematics, specifically their ability to form and eliminate joints on command.
If robots are capable of rapidly adjusting their dampness, stiffing and dynamics, like octopi are, the added flexibility can make for more versatile robotics than ever.
One can find the research in two academic papers: Advanced Functional Materials and IEEE Robotics and Automation Letters.
Merging Soft and Traditional Rigid Robotics
The research helps merge soft robotics and traditional rigid robotics, with the classification of soft or inflexible becoming irrelevant in the next generation of structures and machines. The structure itself is simple enough, with layers of flexible material that’s wrapped around a plastic envelope and then connected to a vacuum source.
The vacuum helps to hold the structure stiff, while still being molded into other forms, resulting in a transition that's a byproduct of laminar jamming, when applying pressure creates friction that joins a group of flexible materials.
The pressure generates a frictional force that acts like glue, where control of stiffness, dynamics, damping and kinematics is made possible by changing the number of layers.
The phenomenon, deriving from the mechanical behavior of laminar jamming, is a focus for the research team, consisting of Yashraj Narang, Joost Vlassak, the Abbott and James Lawrence Professor of Materials Engineering, Robert Howe, the Abbott and James Lawrence Professor of Engineering, and Alperen Degirmenci, a current graduate student in SEAS.
Two-Fingered Gripper in Action
The researchers have no issues demonstrating the structure's abilities as shock absorbers, specifically through attachment to a drone, serving as landing gear. Tuning of the stiffness and damping are done by the team to help absorb the impact of landing.
Additionally, real-world devices have involvement in the process, with the team creating a two-fingered gripper that can wrap around and grab onto sizable objects without a vacuum. With a vacuum, the gripper can pinch and hold onto objects about the same size as a marble.
Such robots utilizing laminar jarring, helping accommodate octopus-like mechanical flexibility, can prove extremely useful, ranging from surgical robotics to flexible technology and wearables.
The Exciting Future of Robotics
Research like this is exemplary of robotics’ exciting future. It’s feasible to think that robots with octopus-like movements will become a norm in the future, especially as research teams continue to integrate laminar jarring in aiding mechanical flexibility.
Whereas many today associate robots with stiff pieces of automation, it’s realistic that the near future will host robots that are better able to multi-task and complete an eclectic array of functions, from medical surgery to offshore drilling repairs.
Continuous research moves robotics away from repetitive tasks and into more creative tasks. More flexible movement, like octopi, will help expedite this process, especially with laminar jarring flexibility coinciding with advances in big data and AI.
Together, these technological advances can play prominent roles in robotics to ensure productivity across a variety of fields.
Although some jobs will expire due to these robots, many more will open up, as is the history of automation in times like the Industrial Revolution. Especially in high-end fields, like medical work, human supervision will likely always be a necessity.
New kinds of robots are mimicking octopi, opening up a broad array of possibilities for robotics and how research in laminar jarring will continue to shift robots away from rigid movements and into more flexible versatility.
SOURCES:
- https://techxplore.com/news/2018-05-robot-transitions-soft-rigid.html
- https://www.seas.harvard.edu/news/2018/05/robot-transitions-from-soft-to-rigid
- http://knowledge.wharton.upenn.edu/article/future-jobs-world-ai-robotics/
The content & opinions in this article are the author’s and do not necessarily represent the views of RoboticsTomorrow
Comments (0)
This post does not have any comments. Be the first to leave a comment below.
Featured Product
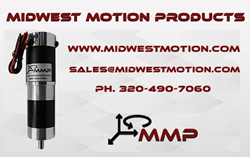