Robotic devices for clinical rehabilitation of patients with neurological impairments come in a wide variety of shapes and sizes and employ different kinds of actuators.
Morphological Approaches in Medical Technology
Contributed by | maxon motors
Reprinted with permission from drive.tech from maxon motors:
The design process for rehabilitation robots is driven by the intention that the technical system will be paired with a human being; it is of paramount importance that safety and flexibility of operation are ensured. When designing a robotic device for people with paretic limbs it is usually desirable to specify the actuators and controllers in such a way that a degree of compliance and yielding is retained, rather than forcing the limbs to rigidly follow a pre-programmed trajectory. This reduces the likelihood of injury which might result from forcing a stiff joint to move in a non-physiological manner, and it allows the patient to positively interact with the system and actively guide the therapy.
It is not uncommon to come across the viewpoint that electric actuators are not well suited to applications having compliant design requirements: in traditional control engineering, DC motors are programmed to provide accurate and fast setpoint tracking; it is often thought that they are not ideally suited for clinical rehabilitation tasks where “soft” behavioural characteristics are called for. This view has led to the emergence of alternative actuator concepts where the desirable properties of compliance are more obvious: passive elastic components, pneumatic valves and actuators, or even artificial muscle constructs have been employed. This gives devices with interesting properties which naturally interact in a yielding manner with the human user. These approaches can be said to take a morphological viewpoint, viz. they have the shape, form or external structure akin to that of an organism.
Recumbent trike prototype for adults. The power for the flat motor and rear wheel hub is supplied by a battery.
Designing a rehabilitation robot from a robust engineering perspective with high-performance DC motors does not preclude features more readily associated with morphological computation and control concepts, i.e. characteristics of compliance and yielding. A simple embodiment of this principle is an impedance control strategy where the torque at a joint is controlled to be proportional to the position deviation, velocity and higher-order terms. These ideas are visible in products like the Lokomat locomotion-rehabilitation robot from Hocoma AG, or in our own range of rehabilitation tricycles including the PowerTrike.
The design of rehabilitation robots lends itself well to morphological ways of thinking since computation and control structures are farmed out from a central processing unit – in this case the damaged central nervous system – to external materials and components. In my view traditional control engineering approaches are well able to deliver systems of this form: engineering concepts for the design of electric drives and control systems have been around for a very long time; they can provide a solid basis for rehabilitation robots and, with an appropriate perspective, they can embody behavioural features to the fore in morphology.
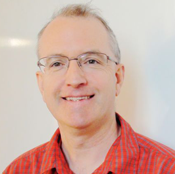
Kenneth Hunt is Professor for Rehabilitation Engineering and head of the Institute for Rehabilitation and Performance Technology in the Department of Engineering and Information Technology at Bern University of Applied Sciences in Burgdorf, Switzerland. He is also a Research Associate at the neuro-rehabilitation clinic Reha Rheinfelden, Rheinfelden, Switzerland. The Scottish-born expert in the field of rehabilitation was co-founder of the “Scottish Centre for Innovation in Spinal Cord Injury” in Glasgow and left his mark on the Centre as inaugural Director of Research.
The content & opinions in this article are the author’s and do not necessarily represent the views of RoboticsTomorrow
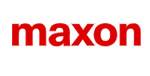
maxon group
maxon is a leading supplier of high-precision DC brush and brushless servo motors and drives. These motors range in size from 4 - 90 mm and are available up to 500 watts. We combine electric motors, gears and DC motor controls into high-precision, intelligent drive systems that can be custom-made to fit the specific needs of customer applications.
Other Articles
Multi-axis motion control drives pipe-based robots
Automate 2025 Q&A with maxon group
Understanding Torque and Speed in Electric Motors
More about maxon group
Comments (0)
This post does not have any comments. Be the first to leave a comment below.
Featured Product
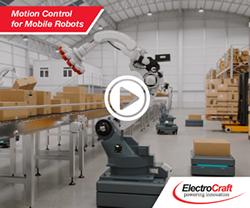