MIRAI learns by watching demonstrations: a human guides the robotic arm through various motions, MIRAI watches, generalizes and learns to solve the same task autonomously.
MIRAI - Using AI to Train Robotic Arms
Ronnie Vuine | Micropsi Industries
Tell me about Micropsi Industries.
Micropsi Industries is a robotics software company, founded in 2014 in Berlin, Germany, with operations in Europe and the U.S.
What's unique about your AI system, Mirai?
MIRAI allows engineers to train robotic arms to perform difficult tasks -- typically tasks that involve reacting to information that is only available visually. MIRAI learns by watching demonstrations: a human guides the robotic arm through various motions, MIRAI watches, generalizes and learns to solve the same task autonomously.
What made you launch the company?
The founders are artificial intelligence experts. We wanted to work on systems that learn to deal with environments they weren’t prepared for. And when we looked at industrial robotics specifically, it quickly became obvious that there was a major gap there: The limits of machines that had nothing to do with the hardware. We could make them so much more powerful by adding cameras and an AI system that could learn hand-eye-coordination movements.
AI seem to be a buzzword today. How hard is it to deploy AI applications and why?
Yes, AI is a buzzword. People have started using the term “AI” for pretty much anything that contains an algorithm, which can be annoying. We’ve been doing this for a long time and will continue to do so even after the hype has died down.
Deploying AI (or machine learning) is hard for end-users because they often don’t have the expertise to do it, especially if they’re mid-sized or small companies whose core business is something else entirely.
The way to make real progress in AI available to these companies is productization – which is what we’re doing at Micropsi Industries. With MIRAI, you can solve a fairly complex computer vision problem without understanding much about the technology. You need to be able to install the robot and use a couple of hours to train it – it’s all physical, intuitive activity now, not a month-long experience of learning or an expensive expert hire.
Can you give us a real world example of how your software is being implemented?
We use a demo to show how the system can plug in cables. The system works with any task that requires positioning a robotic arm by watching a human – MIRAI controllers can also place testing probes on soldering points, find and approach features on steel part, pick up various types of objects, and help build complex structures out of carbon fiber.
What are some trends that you see in 2019?
The trend is automation -- no matter what happens to the world economy. In robotics specifically, I’m looking forward to a whole range of new experimental robotic arms, more and better sensors, especially cameras, and startups that take these new components and build exciting vertical applications: from building houses to manufacturing rocket engines to making pizzas. When it comes to the large fields of application, besides assembly (which is what we target with MIRAI) I think we’ll see more logistics automation with robots – the space has heated up considerably in the last years and looks very promising.
About Ronnie Vuine
Ronnie Vuine is co-founder and CEO of Micropsi Industries, a robotics software company headquartered in Berlin, Germany -- recognized by Smart Industry as one of 10 startups whose “technology will shape our future.” A philosopher and computer scientist by training, he has a long-standing passion for artificial intelligence and enabling technical systems to inter-act autonomously with the real world. With the Micropsi Industries team, he set out to transform the industrial robotics market by applying the flexibility made possible by machine learning to manufacturing. He regularly speaks at tech conferences and writes about the future of artificial intelligence, robotics, and manufacturing automation.
The content & opinions in this article are the author’s and do not necessarily represent the views of RoboticsTomorrow
Comments (0)
This post does not have any comments. Be the first to leave a comment below.
Featured Product
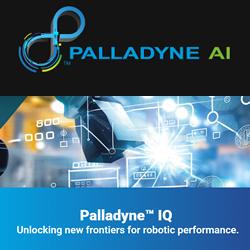