With the growth and proliferation of collaborative robots, there has become an increased need for a wide variety of grippers and end effectors in general. One of the more challenging applications is for automated gauging and measurement of small parts.
Smart Gripper for Small Collaborative Robots
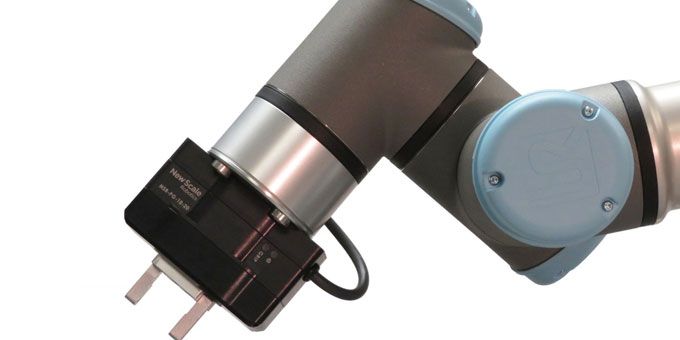
Case Study from | maxon Group
Reprinted with permission from maxon:
Such a device must provide high-resolution positioning with resolutions as low as 2.5 micrometers that can be continually available to decision-making software in automation applications. This is why New Scale Robotics (NSR), a Division of New Scale Technologies decided to design and manufacture one of their latest grippers.
Built for the smallest collaborative robots, the NSR-PG-10-20, Precision Parallel Gripper, is a mechatronic system that integrates motor, sensors, precision bearing guides, drive, and control electronics, along with embedded firmware for automation, into one device. During the design process, NSR decided that the gripper had to offer plug-and-play integration that could be installed in minutes to Universal Robotics (UR) line of small cobots. The NSR-PG-10-20 offers users the smallest size and mass with the highest precision. All power and control circuitry is located through the robot tool port and slip rings so that no external cable or electronics boards are required. To install the gripper, simply mount it to the UR robot tool flange and connect the single cable to the UR tool I/O port. Motion commands are received through the robot’s 8-pin tool I/O interface. No external wires or separate electronics are needed, which allows for full 360-degree or infinite rotation of the UR robot wrist joint without cable interference.
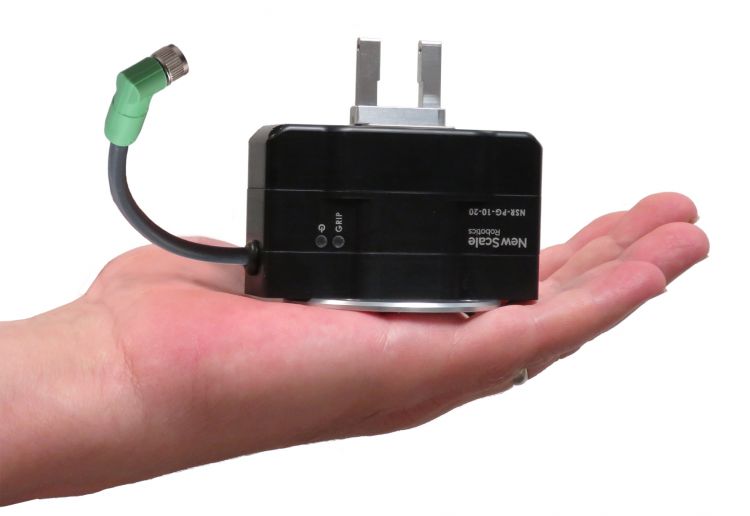
The NSR-PG-10-20 Precision Parallel Gripper incorporates maxon’s EC-20 Flat motor for high precision operations
The Precision Parallel Gripper incorporates an internal absolute position sensor specifically for automated metrology applications offering high precision for intricate small part handling, measurement, sorting, and assembly. The grippers had to provide fast, precise movements repeatedly over a long life cycle.
Precision Motion Control
During the design process, NSR researched the needs of their Precision Parallel Gripper and selected the EC-20 Flat brushless DC motor (BLDC) designed and manufactured by maxon. This motor offers up to five winding types as well as built-in encoders. Multiple power outputs are available, and the motors provides high stability and quiet operation. The motors were primarily selected because of their extremely small mass of only 15 grams as well as their high continuous torque of 3.75 mN-m. The motors’ excellent torque-to-mass ratio means that the NSR-PG-10-20 can achieve an adjustable gripping force of ±3 to 10 N while using a modest gear ratio of 16:1. The gripper incorporates a symmetric timing belt drive with a range of 20 mm. Plus, the operational voltage, current, and torque were a good match with the internal robot power supply.
The BLDC rotary motor drives gear reduction to a timing belt that converts rotation to linear motion. A separate angle sensor is used to measure the motor shaft angle, while separate digital electronics are used to generate the three-phase drive current needed for operation. This mechanism provides the linear motion necessary to open and close the gripper fingers used to grab and release small parts. Gripper fingers are able to grip from the outside or inside of the part depending on the application. Through the use of the embedded sensor mentioned above, the linear part measurement resolution of the gripper is 2.5 micrometers. The open/close speed of the gripper is 20 mm/second and the open/close range is 20 mm.
According to David Henderson, CEO of NSR, “The tricky parts of the design were maintaining the small size, height, and low mass of the gripper while providing closed-loop position and velocity characteristics. It was also a challenge to find a low power and current motor that allowed us to use the internal power on the robot.” maxon’s EC-20 Flat allowed NSR the leverage they needed to deliver the product their customers most needed — and still be easy to install and operate. The mechanical integration was the easiest part. The company used an EC-20 Flat without an angle sensor and instead provided their own external angle sensor for commutation. “In the future, we expect to extend our product range to include grippers with higher gripping forces — and correspondingly higher mass and power motors—longer gripping ranges, and embedded force sensors to improve force control,” Mr. Henderson said.
The gripper is equipped with interchangeable fingers. The NSR-PG ships with factory fingers installed so that users can get right to work. The gripper also provide teachable finger positions when used with Universal Robotics’ UR3, UR5, UR10 robots as well as the company’s latest line of eSeries Robots, the UR3e, UR5e, and UR10e robots. Manually move fingers to the desired position and set them using the teach pendant—a process familiar to anyone who has used a UR robot in teach mode. Position is repeatable to 0.01 mm. By setting finger open and close positions that match a user’s workpiece allows the user to minimize the finger motion (stroke) for each operation, saving time and energy. Overall, the NSR-PG-10-20 allows the user to automate repetitive, labor-intensive measurement and quality control tasks so that the UR cobot becomes a powerful tool for metrology applications.
Finding the right motor for such specific applications can be a daunting task. Having the availability of the latest technology in the smallest package motor has allowed NSR to fulfill the needs of their customers. maxon’s EC-20 Flat was a key component in the design and manufacture of the NSR-PG-10-20 Precision Parallel Gripper.
The content & opinions in this article are the author’s and do not necessarily represent the views of RoboticsTomorrow
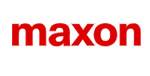
maxon group
maxon is a leading supplier of high-precision DC brush and brushless servo motors and drives. These motors range in size from 4 - 90 mm and are available up to 500 watts. We combine electric motors, gears and DC motor controls into high-precision, intelligent drive systems that can be custom-made to fit the specific needs of customer applications.
Other Articles
Multi-axis motion control drives pipe-based robots
Automate 2025 Q&A with maxon group
Understanding Torque and Speed in Electric Motors
More about maxon group
Comments (0)
This post does not have any comments. Be the first to leave a comment below.
Featured Product
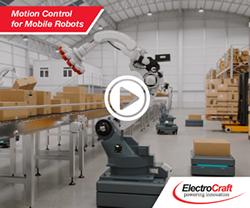