“We chose a combination of solutions from OnRobot, Universal Robots, and EasyRobotics because they are easy to program, and the investment will pay for itself in just nine months. It’s one of the best business decisions we’ve ever made.”
FT-Produktion Boosts Output Capacity Without Adding Personnel by Employing Combination of Collaborative Robots and Robot Grippers
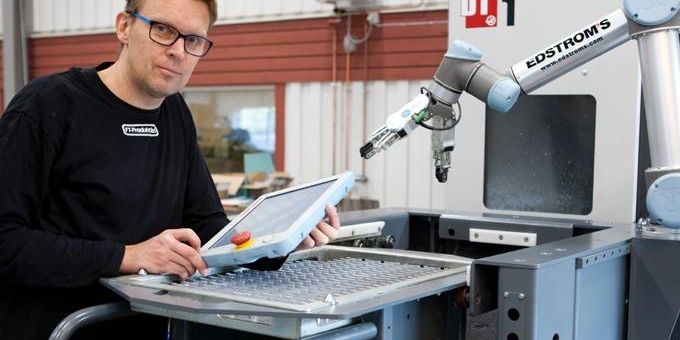
Case Study from | OnRobot
No machine shop would turn down global industry leaders like Volvo, Renault, and Scania when they come calling with orders – even if it means pushing capacity and productivity to the limit. But in a labor market where recruiting qualified employees is easier said than done, it takes innovation to increase output capacity. Plus, with an annual revenue of just over 2 million US dollars a year, saying no to new business would mean limiting FT-Produktion's otherwise enormous capacity for growth.
Based in the southern Swedish town of Åseda, FT-Produktion has a diverse staff of 25 employees with roots in Sweden, Norway, Lithuania, Syria, and Thailand. Working in tandem with neighboring company Profilgruppen, FT-Produktion supplies a wide range of customers – including carmakers, construction companies, and the furniture industry – with metal parts used in the manufacturing of balconies, solar panels, electrical fixtures, and trucks. To meet growing market demand, the Swedish machine shop turned to specialized robot technology designed to meet the automation needs of small and medium-sized manufacturing businesses.
“The demand for productivity continues to grow,” said Joakim Karlberg, who owns and operates FT-Produktion with his sister. “But relevant manpower is hard to come by these days. Thanks to automation, an operator can keep three or four machines running at once without stress.”
FT-Produktion discovered collaborative robot – or cobot – solutions during a meeting with the machinery dealer Edströms, which supplies and installs turnkey cobot solutions with various processing machines. Edströms also offers thorough training courses for employees tasked with operating and reconfiguring cobot arms, grippers and filling modules.
FT-Produktion discovered cobot solutions during a meeting with the machinery dealer Edströms, which supplies and installs turnkey cobot solutions.
In 2017, the company made the largest investments in its history by renovating much of its machinery. A small share of the overall investment went to a key addition: the introduction of a flexible robot cell featuring a UR5 cobot from Universal Robots, two RG2 robot grippers from OnRobot, and a ProFeeder from EasyRobotics. This trio of Danish cobot solutions has now provided automated machine operation at FT-Produktion for more than a year. Almost immediately, the sales department could accommodate orders with much higher volumes and shorter delivery times – without asking employees to work overtime.
“I would like to see more robots here,” says Mikael Andersson, who is not afraid of losing his job. Rather, his daily tasks are more varied and interesting following the introduction of automation technology at FT-Produktion.
Noted Karlberg, “We chose a combination of solutions from OnRobot, Universal Robots, and EasyRobotics because they are easy to program, and the investment will pay for itself in just nine months. It’s one of the best business decisions we’ve ever made.”
Streamlined filling processes
With the cobot cell working up to 16 hours a day, five days a week, a run of 150,000 units can be manufactured in less than two months. Once every 25 seconds a gripper on the robot arm removes a raw part from the ProFeeder’s parts tray in the mover and inserts it in a CNC machine. In the same robot arm movement, the other gripper takes a finished part out of the CNC machine and places it in a container. This is made possible by the robot arm’s “two hands”: an RG2 double gripper from OnRobot that reduces the cycle time by 12 seconds per task. In other words, FT-Produktion saves 500 hours when manufacturing a series of 150,000 parts.
In the past, an employee had to manually insert four parts at a time in a CNC machine, wait for 90 seconds, and then repeat the process for the duration of the workday. Now, the solution requires just five minutes to manually fill one of the ProFeeder’s two movers. When the robot has emptied one of the mover’s parts trays, the operator removes the empty mover and clicks a filled mover into place in the ProFeeder, allowing the CNC to rapidly resume operation. Using the Lean Robot Automation concept from EasyRobotics, the filling process can be further optimized if the machine shop places the parts for processing directly into one of the mover’s parts trays in the preceding step of the overall process.
“Now we can fill bigger orders despite the scarcity of labor,” says Joakim Karlberg, who is dedicated to creating a good and attractive working environment for his 25 employees. He is pictured here speaking with machine operator Agneta Hult.
“It seems like there’s no end to this economic upswing, which means no end to our bottleneck issue,” noted Karlberg. “We can already see many more opportunities for improved optimization and automation. If things keep going as planned, we imagine we’ll have two additional cobots in our facility within the next two years.”
“Plus,” continued Karlberg, “robotizing the high-volume production run has enabled us to eliminate monotonous manual tasks, giving employees more time to work on smaller runs with greater variation in their tasks.”
A less monotonous work day
Mikael Andersson is a machine technician at FT-Production. One year ago, he also became a robot programmer and robot operator following two days of theoretical and hands-on training at Edströms. The training course was based on the Universal Robots Academy concept, which includes ongoing follow-up training via free e-learning courses. Mikael also received training in the use of the EasyRobotics ProFeeder and the dual gripper from OnRobot, enabling him to easily and flexibly install, program, operate, and reconfigure the overall solution.
“Using the robots was actually more intuitive than I expected,” said Andersson. “The cobot solution is so easy to reconfigure that even small production runs are no longer cost prohibitive. Plus, it just makes my job so much more interesting.”
“We deliver a complete solution – a CNC machine automated with collaborative robot technologies,” says Adam Asplund, sales representative at Edströms.
The family-owned machine shop FT-Produktion is located in the southern Swedish town of Åseda and has 25 employees. FT-Produktion has annual turnover of just over 2 million US dollars.
Working in tandem with the neighboring company Profilgruppen, FT-Produktion supplies a wide range of customers, including carmakers, construction companies, and the furniture industry. The company’s metal parts are used in the manufacturing of balconies, solar panels, electrical fixtures and trucks.
FT-Production shop manufactures 650 different aluminium profiles and fills 7,000 orders annually, with production runs ranging from five to 150,000 units. Given the wide range of tasks and volumes, flexible automation is absolutely essential. A single robot solution must be capable of handling many different parts with minimal downtime when reconfiguring from one production run to the next.
The new generation of collaborative robot arms also requires high performance accessories. For example, the functionality and user-friendliness of grippers ultimately determines the scope and variety of tasks and parts that can be automated, as well as the ROI time for automation investments.
“It only takes 10 seconds to change to a different part on the robot’s display,” says Andersson. “The robots are not taking any jobs. Instead, they’re enabling us to fill more orders and deliver more detailed parts with higher quality.”
FT-Produktion’s first cobot cell is based on the plug & produce principle, which makes flexible automation easy and profitable for small and medium-sized manufacturers. The cobot cell includes the following components from the global leaders in modern collaborative robot technology: A UR5 robot arm from Universal Robots; a ProFeeder from EasyRobotics; and a dual gripper solution with two RG2 grippers from OnRobot. This fully integrated robot solution offers intuitive operation and programming, with 3D visualizations on the robot arms touchscreen. The ProFeeder and RG2 are certified by Universal Robots and offered through the Universal Robots+ app platform.
If you like this article you may like "Smart Gripper for Small Collaborative Robots"
The content & opinions in this article are the author’s and do not necessarily represent the views of RoboticsTomorrow
Comments (0)
This post does not have any comments. Be the first to leave a comment below.
Featured Product
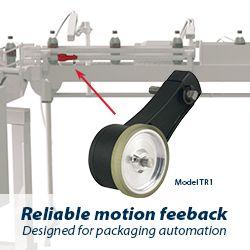