Precision soldering applications have long been dependant on manual processes, making it virtually impossible to provide consistent quality. Human error is always a risk with manual soldering.
Good Things Come in Automated Packages
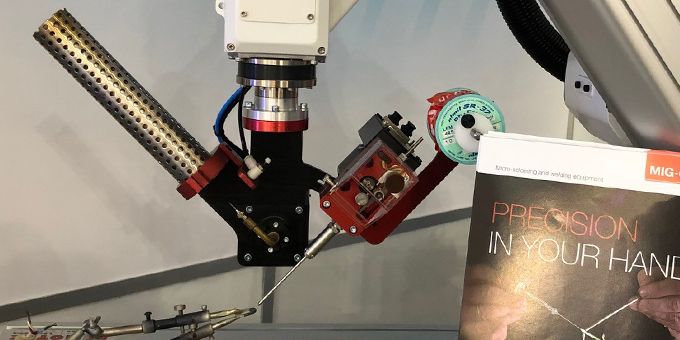
Case Study from | TM Robotics
The earliest printed circuit boards, patented by Austrian inventor Paul Eisler in 1943, were assembled by hand. The tedious method involved manually cutting, trimming and soldering numerous wires. The process was slow and prone to error and unfortunately, it hasn’t evolved much since. Focusing on the manual side of processes, such as extra assembly, MIG-O-MAT approached industrial robot suppliers, Elmotec and TM Robotics to develop an automated soldering solution.
Plasma welding and microflame soldering company, MIG-O-MAT, believes automated precision soldering is the solution. Since 1972, MIG-O-MAT has been developing welding technologies and corresponding appliances in the fields of plasma welding and microflame soldering. The company’s micro-soldering and welding units benefit from their own gas production; the electrolysis of distilled water produces a hydrogen and oxygen mixture which is used to feed the microflame, leaving no residue.
For end users, this ensures the microflame is able to reach temperatures up to 3000 degrees Celsius, nearly melting every metal and editing glass or other materials due to its constant composition. Using lightweight micro-nozzles, units are almost always operational and consume very little distilled water, boasting the benefits of contactless soldering and no static charge in the parts. However, this doesn’t tackle the issue of inaccuracy which is prevalent in manual soldering.
Precision soldering applications have long been dependant on manual processes, making it virtually impossible to provide consistent quality. Human error is always a risk with manual soldering. After all, human movement can never be entirely precise. This issue of inaccuracy is more apparent in the manufacture of smaller component packages. Populating assembly boards with components, for instance, requires extremely high levels of accuracy to ensure electricity flows through the circuit correctly. As electronics components become increasingly smaller, the problem of inaccurate soldering is even more likely to occur.
MIG-O-MAT wanted to bolster its already established soldering technology, increasing accuracy and repeatability. To do this, the company began to investigate ways to remove 100 per cent of process fatigue by deploying automation. In other words, remove humans from the equation.
Automating the process
Six-axis robots are an ideal option to automate repetitive tasks and as such, they have proliferated with the rise of mass production. Six axes allow a robot to position itself using yaw, pitch and roll movements, as well as allowing the robot to move in the x, y, and z planes; perfect for simulating a human arm performing complex movements.
Six-axis robots also display high levels of positional repeatability; around 30-50µm. This repeatability has seen six-axis robots move from traditional manufacturing facilities into new applications, such as adaptive processes, accurate machining and in this case, soldering.
To find a machine that could automate the soldering process, MIG-O-MAT specified a robot that could deliver high levels of repeatability, while being flexible enough to be installed in an array of applications.
One important area of application for MIG-O-MAT’s customers is the production of solder joints in electronic mechanical engineering and electronics. The smallest component size which can safely be mastered in are solder joints on transducer with a wire diameter of just 0.06 millimetres, highlighting the need for not just a flexible robot, but one that could deliver extremely high levels of accuracy.
“Reducing process fatigue was a key priority when searching for a robot to integrate with our microflame soldering technology,” explained Burak Maltepe, sales engineer at MIG-O-MAT. “This came with two objectives: to increase the frequency and repeatability of precise micro-soldering applications without compromising the key positional accuracy of soldering, while also allowing end users to specify their own installation, allowing it to be suitable for numerous sectors.”
To achieve this, MIG-O-MAT approached Elmotec, the Swiss partner of TM Robotics, the EMEA, North and South American distributor of Toshiba Machine industrial robots. Elmotec specialises in solving application problems through the development and production of electric drives and controlled soldering equipment and machines.
TM Robotics and its network of global partners prides itself on its ability to recommend the right automation solution for unique applications, as opposed to selling an off-the-shelf machine. For this specific application, TM Robotics suggested the TVL500, a light-weight, compact vertically articulated six-axis robot.
The TVL500 offers high performance and productivity on all pick-and-place and assembly operations. Yet, because of its compact size, it also saves on space. For MIG-O-MAT this small footprint was imperative. With a large number of potential applications in industry, keeping the robot’s space requirements to a minimum would allow MIG-O-MAT to target a wider customer pool.
Adjusting a six-axis robot to ensure high positional accuracy in precise soldering applications can be a significant operation. When integrating the robot with existing technology, there are a lot of considerations to be made in relation to positioning and reach.
The TVL series from Toshiba Machine fulfils this need. In fact, it was awarded the Nikkan Kogyo Shimbun Machine Design award for its ergonomic design. This includes the addition of four additional tool fixture tap holes, which are ideal for adding peripheral devices to the robot. Secondary tap holes on the base of the unit also allow the robot to be installed sideways. For MIG-O-MAT, this provides even more installation options for end users with tricky soldering requirements.
The TVL500 six-axis robot is the smallest of the two robots in the Toshiba Machine TVL range, offering a maximum reach of 602mm and a maximum payload of 3kg. With a standard cycle time of less than 0.4 seconds, this competitive automation is ideal for applications where high speeds and accuracy are necessary.
“Integrating the TVL500 improved the overall process time of a general soldering operation, but an unexpected advantage was the increased ease in which an operator can detect possible errors during soldering,” continued Maltepe. “With manual soldering, any errors that do occur are inconsistent and almost impossible to detect. Using automated technology means errors — which have already been drastically reduced — can be identified easily. More importantly, end users can reprogram the robot to the correct adjustments and ensure the error does not occur again.”
The process of adapting the TVL500 for soldering was made easier because of TM Robotics’ experience in supplying robots for niche applications. As the official distributor for Toshiba Machine outside of Japan, the company has several decades of experience supplying robots through its large distributor network, of which Elmotec is a Swiss distributor.
“At TM Robotics our entire philosophy is about making things straightforward and easy for our customers” said Nigel Smith, managing director of TM Robotics. “This philosophy stems through the ease of integrating our robots into production lines, to ensuring we have a trustworthy network of distributors who are able to fully understand their customer’s needs and provide the ideal solution.
“The TVL500 is just one of the much larger six-axis robot range offered by TM Robotics, we also supply the TV and TVM robot series, both of which have an array of options to adapt for different operations,” continued Smith.
Since the collaboration, MIG-O-MAT presented the micro-precision soldering solution at the Productronica Show, a trade fair for electronics production, held in Munich, Germany. The creation piqued the interest of a number of micro-precision soldering companies, and gathered invaluable feedback on the feasibility of deploying this robot in electronics production.
Accuracy is important in all industries, but for the micro-precision soldering industry, maintaining absolute positional accuracy is key. As MIG-O-MAT discovered, automating precision tasks using a six-axis robot not only improves the accuracy substantially, but also the repeatability and throughput of the whole process.
The content & opinions in this article are the author’s and do not necessarily represent the views of RoboticsTomorrow
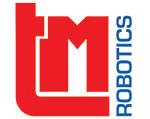
TM Robotics (Americas) Inc
TM Robotics, in partnership with Shibaura Machine, formerly known as Toshiba Machine until 1st April 2020, offers a comprehensive range of industrial robots ideally suited for high-precision assembly, machine loading/unloading and material-handling applications that can be dust proof, clean room, or IP65/67. The company's extensive product line starts with a Cartesian solution available in thousands of combinations from single actuators to four-axis solutions; six-axis solutions that can include precise vision-control; and a complete range of SCARAs from low cost to the industry-leading SCARA with 1200-mm reach that can carry up to 20 kgs. TM Robotics sells and services robots throughout Europe, the Middle East, India, Russia, and Africa, as well as North, Central, and South America, from headquarters in Hertfordshire, England and Elk Grove Village, IL, USA. For more information, visit www.tmrobotics.com or follow us on Twitter, LinkedIn and YouTube.
Other Articles
Giving lens cleaning cloths a robotic hand - Robotic automation for textile processing
Investing in the UK’s injection moulding sector - The case for all-electric machines and robotic integration
Robotic solutions for pharmaceutical packaging - Automated system addresses key limitations of manual processes
More about TM Robotics (Americas) Inc
Comments (0)
This post does not have any comments. Be the first to leave a comment below.
Featured Product
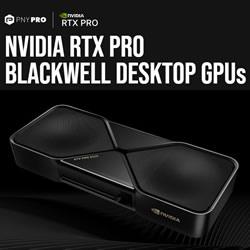