A high quality, efficient, and reliable screw CNC machine shop making two million parts per month, Swiss Productions gained a competitive advantage by implementing two OB7 cobots on their CNC mills to eliminate idle spindle time and maximize production.
Case Study: Swiss Productions Maximizes Output with Two Productive Robotics OB7 Cobots
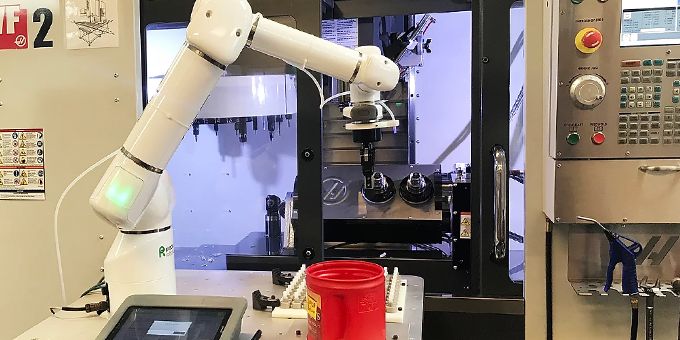
Case Study from | Productive Robotics
From a family owned company that started in a 750 square foot facility and 5 screw machines, Swiss Productions grew to what it is today – a high quality, precision, and reliable screw machine shop producing over 2 million parts per month to customers worldwide in the medical, electronics, aerospace, and government industries.
Located in Ventura, California, Swiss Productions today has over 50 screw machines and 30 secondary machines and produces components ranging in size from 2.5 inches in diameter down to syringe tips measuring .019 inches in diameter. Meeting the demands of their customers nationally and internationally while also maintaining the utmost quality requires constant innovation, forward thinking, and finding creative solutions to challenges.
So, when faced with the challenge of maximizing their machine output and employee productivity, they quickly began exploring new solutions.

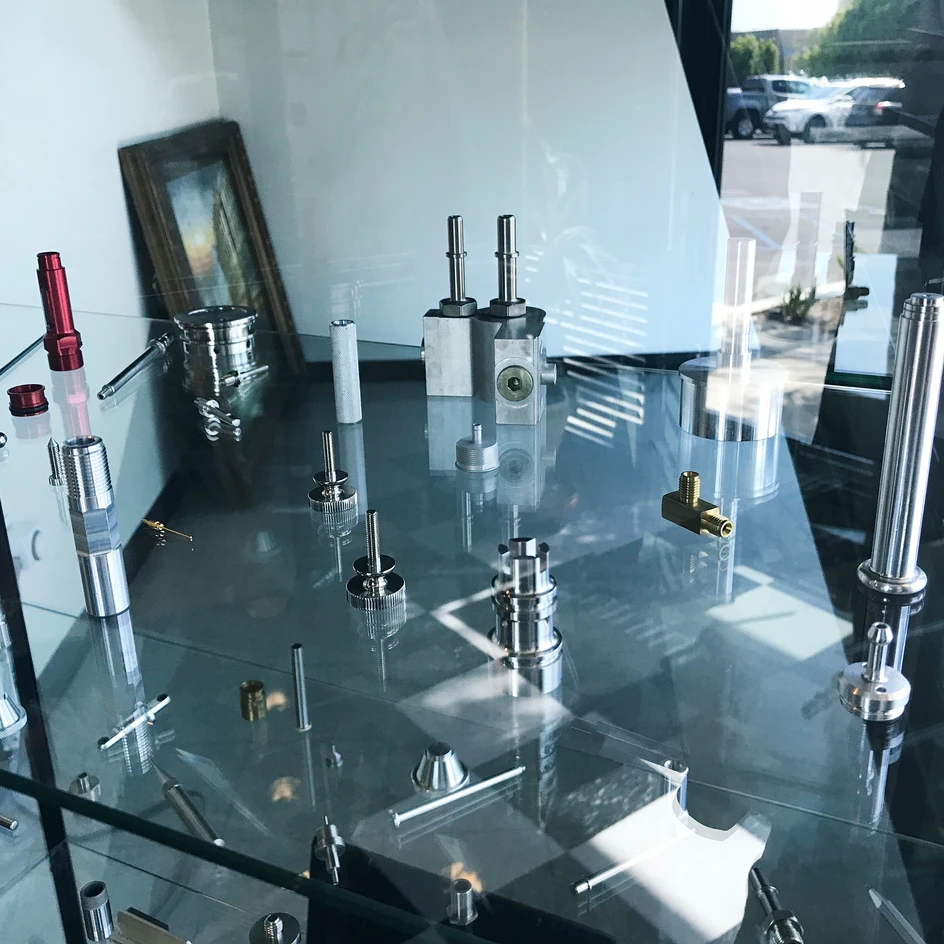
The Challenge: Minimizing Idle Spindle Time
Swiss Productions faced a production issue on their CNC machines. Although they had the skilled operators to handle their machining, they were not maximizing their spindle time. One of their biggest challenges was keeping their Hass Mill machine running consistently.
“The machine would only get 9 hours of production a day, and an employee would sit on the machine loading and unloading every 7-8 minutes, and take one hour worth of breaks a day,” explained Swiss Productions General Manager, Timo Lunceford.
Production would also be interrupted if the machine operator lost focus while attending to other tasks.
Swiss needed a way to keep their machines running 24 hours a day, generating more products while lights were out. Consequently, their machine operator was losing time to focus on other tasks while operating the machine.
“Our operators would stand for 10 minutes, wait for the part to finish and then reload it. We were losing precious time that could be used more efficiently.”
The Solution: Machine Tending CNC Mills with OB7
To find the answer to nonstop production, Swiss Productions investigated various collaborative robots on the market. They discovered Productive Robotics, and were immediately drawn to OB7. Swiss was attracted to OB7 in particular because of its 7 axes, which would provide the extra flexibility for handling their CNC machines.
“When we discovered OB7, we knew the 7th axis for us is key. We are going in, grabbing the parts, moving sideways with them, and then blowing out the collets that we are using to hold our parts. We need a quick turn radius because we also have to teach it to close the door and then double check that the door is closed, and then be able to pivot to press the start button, which is a complete 180° from where it was,” States Lunceford.
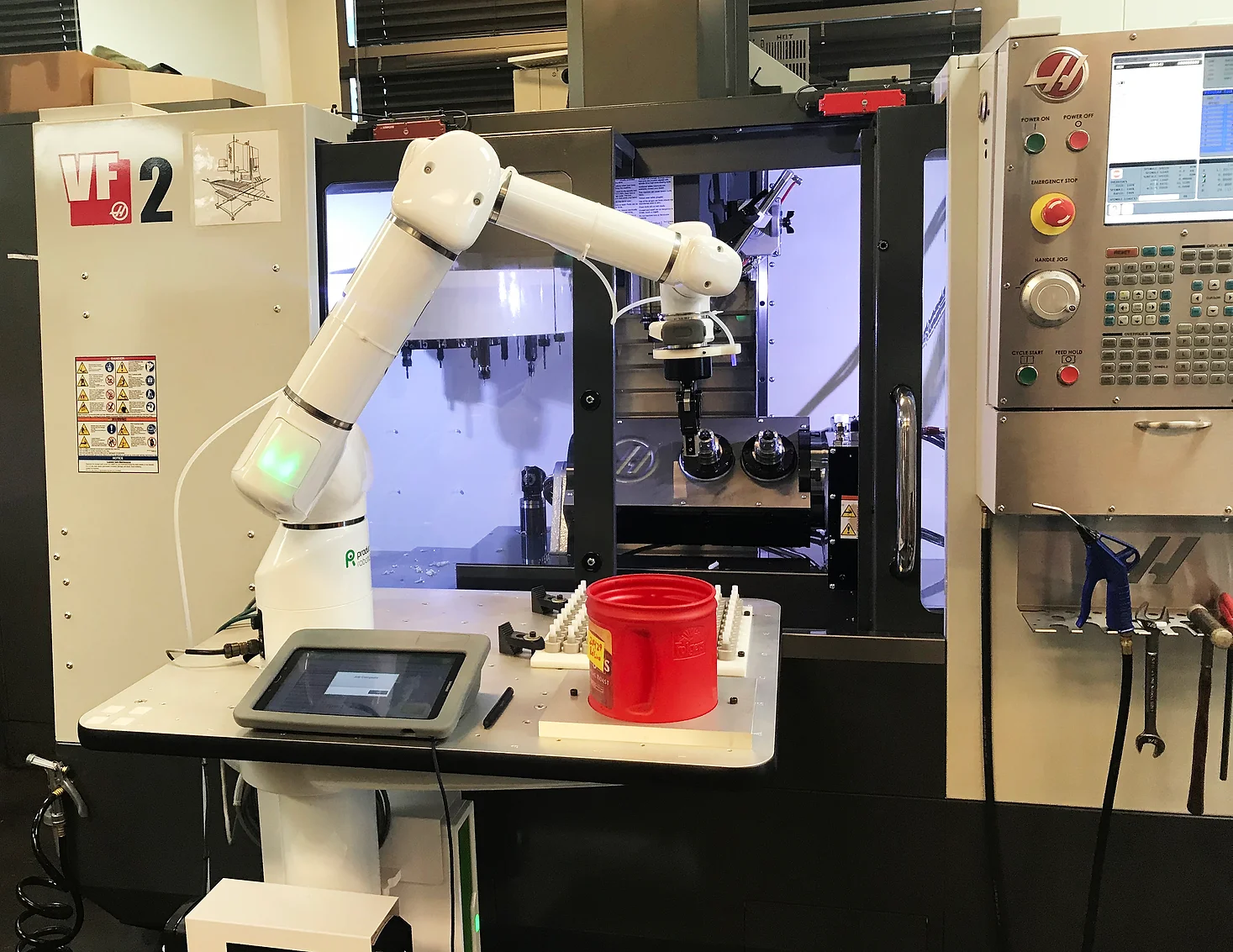
Integrating OB7 with the Haas Mill was accomplished entirely by Swiss employees, no outsourcing needed. In a few days, OB7 was up and running.
Quickly working “lights out,” Swiss gained an extra 32 hours per week of machine running time on top of the normal 40 hours. In addition, they gained back the hours lost during breaks, bringing the total weekly production time up to 76 hours.
Employee productivity was another priority for Swiss. With OB7 tending the machines, employees were able to take on other tasks to advance production.
“The employee that would normally sit at the machine before OB7 is now able to run two of our smaller lathes at the same time. Previously, the cycle time wouldn’t allow for that between all three machines,” noted Lunceford.
OB7 was driving higher output while also saving Swiss thousands of dollars monthly.

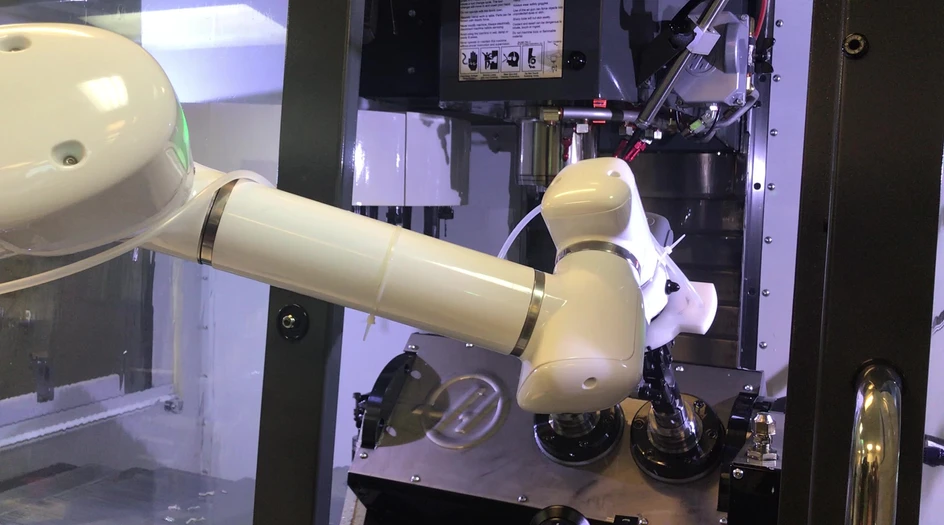
The Future: Plans for OB7 on Lathes and other machines
Integrating OB7 into their machine shop has allowed Swiss to gain a competitive advantage by increasing their production and enhancing their team’s productivity. The success with OB7 was so valuable that Swiss Productions implemented a second OB7 to operate one of their other CNC mills.
"We have not let go of any employees and our production has increased. We have big plans for OB7, not just on our mills but on our lathes we are producing parts as well,” Lunceford shared.
With each challenge providing opportunities for growth and innovation, Swiss Productions is on their way to unsurmountable growth. With OB7, there are no limits to their future going forward in size, quality, and innovation.
“We have not let go of any employees and our production has increased. We have big plans for OB7, not just on our mills but on our lathes we are producing parts as well” Timo Lunceford, General Manager, Swiss Productions, Inc.
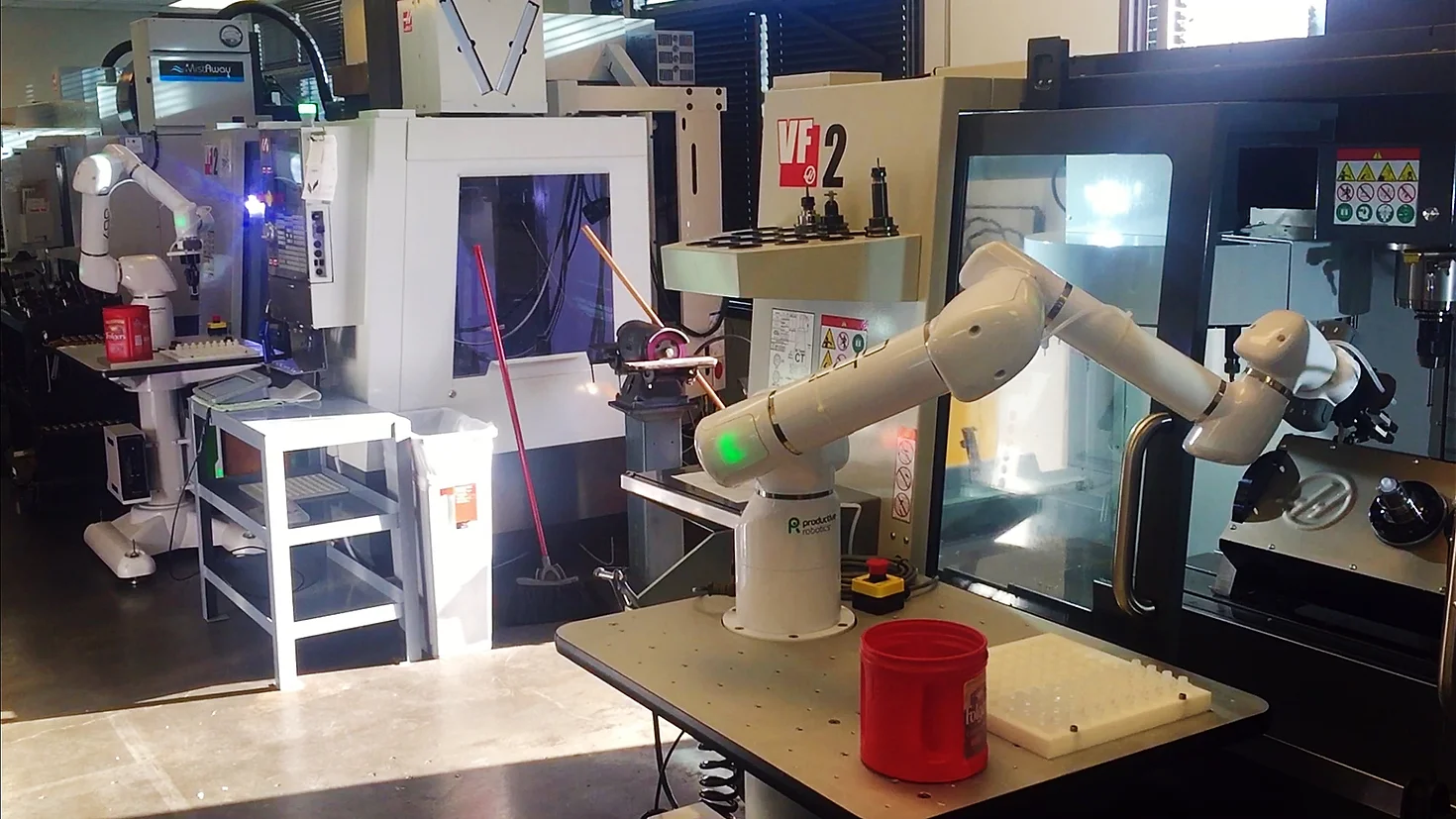
Case Study Highlights

Challenge
- Not maximizing machine spindle time by only getting 9 hours of production a day
- Machines frequently idle due to breaks and stalls in between jobs
- Operators losing valuable time to focus on other tasks
- 7 Axes
- Simple Teaching Interface
- Customer Service
The content & opinions in this article are the author’s and do not necessarily represent the views of RoboticsTomorrow
Comments (0)
This post does not have any comments. Be the first to leave a comment below.
Featured Product
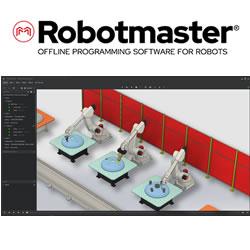