When digital information transforms into precise physical motion, previously infeasible use cases suddenly become possible. This improvement delivered Industry 4.0 to applications such as advanced robotics, Internet of Things (IoT) and Industrial Internet of Things (IIoT),.
Precision Motion Control Enables Automation
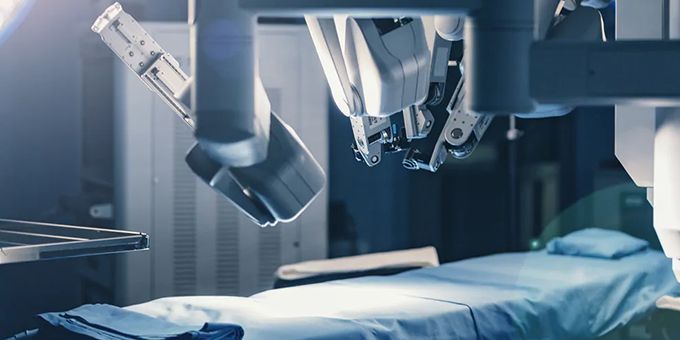
Adam Kimmel | Mouser
The world of automation exists in four dimensions: height, width, depth, and time. When the equipment must place an object in an exact location precisely, it requires motion control—the control of position, speed, and acceleration. Fabricating objects for specialized applications leverages the precision and reliability of motion control more than most other disciplines.
When digital information transforms into precise physical motion, previously infeasible use cases suddenly become possible. This improvement delivered Industry 4.0 to applications such as advanced robotics, Internet of Things (IoT) and Industrial Internet of Things (IIoT), battery-powered medical devices, additive manufacturing, and prosthetics. Each of these applications requires high precision in the control of the manufacturing equipment. As a result, turning digital information into physical motion and accurate part placement for these applications requires more than just transferring data into movement.
In the following, we’ll discuss precision motion control, review medical and industrial automation applications needs, and highlight high-performance Trinamic product recommendations in each area.
Precision Motion Control
Precision motion control uses stepper motors to guide the active machine components’ position. Open-loop systems employ a stepper motor, which converts the electric control signal into a precise rotational position for the shaft. For higher-precision uses, engineers incorporate a check feature to measure the shaft’s position. The measurement device sends dimensional data back to the controller to compare with the setpoint, allowing variance correction. The two-way communication is termed closed-loop.
CNC machining is one of the most well-known applications that benefit from advanced-precision motion control, but 3D printing and desktop manufacturing also benefit from tighter tolerances. Inspection equipment that feeds information back to the controller, pick and place machines, and automated assembly lines are three of the other segments that benefit from high-precision motion control.
With precision motion control, labs run more smoothly, and warehouses experience additional increases in operational efficiency. Simultaneously, this control improves product cost elements driven by inefficiencies, such as:
- Heat loss and power consumption
- Resonance
- Audible noise
- Diagnostics without sensors
- Battery life
The Trinamic Motion Control Architecture consists of functional building blocks. The motor controller (or motion controller) receives commands over a selected interface in a defined protocol. The tasks are translated into signals for the motor control and driver part. For ease of integration into the application’s firmware, the code exports in Trinamic’s format or C. Read on to learn about Triminic’s recommended products for medical and industrial automation applications.
High-Precision Applications
Trinamic developed products that address the performance issues in medical and industrial automation.
Medical
Medical devices, such as pumps and ophthalmic devices, need precise control at low speeds. Applications ranging from tissue analysis to blood centrifugation and liquid handling provide opportunities for a solution to low-speed, minimal-vibration precision. Trinamic technology provides current loops that are nearly perfect sine waves to address excessive vibration. The smooth curves limit vibrations that would hinder tolerances. Inefficient current conversion in the motor leads to temperature rise in the component, creating a system failure or automatic shutoff event. Furthermore, tweaking the acceleration profile can allow system operators to improve precision and smooth out machine component movements.
Below are Trinamic product recommendations ideal for the respective medical applications:
- Tissue analysis: TMCM-3110 (3-axis for sensorless load dependent current control) (Figure 1)
- Blood centrifugation: TMCM-1636 (1-axis for 3-phase BLDC motors)
- Liquid handling: TMCM-6110 (6-axis for sensorless load dependent current control)
Figure 1: The TMCM-3110 is a triple axis stepper motor controller/driver module for sensorless load dependent current control. (Source: Mouser Electronics)
Ensuring precise, low-speed, smooth operation is the key to motion control in medical device automation. With a range of solutions from sophisticated chips to smart motors, Trinamic’s motion control solutions are customizable and flexible to applications in this space.
Industrial
Productivity and throughput drive product development for industrial applications. As motion control improves, Trinamic’s advanced diagnostics and interconnected drives enable an intelligent factory. The technology is robust enough to apply to standalone applications to networks by creating building blocks that system designers can use to build the most efficient, customized solution for their needs.
3D printing, robotics, and factory automation are three applications that require precision automation. Trinamic products that serve these use cases are:
- 3D printing: TMC2209 (ultra-silent motor driver integrated circuit for 2-phase stepper motors)
- Robotics: TMC5160 (high-power stepper motor controller) (Figure 2)
- Factory Automation: TMC262 (integrated stepper motor)
Figure 2: The TMC5160 combines a flexible ramp generator for automatic target positioning with industries’ most advanced stepper motor driver. (Source: Mouser Electronics)
The products above address significant challenges with industrial applications. 3D printing is notoriously loud, disrupting activities happening near the operation. TMC2209 smooths the sine waves and enables quiet part fabrication at higher dimensional accuracy. The TMC5160 is similarly soft and rapidly produces high-accuracy robotic components. It is highly integrated and scalable, maximizing operational efficiency to drive throughput without wasted energy or time. The TMC262 can drive to a gate current of 40mA, ideal for laboratory and factory automation applications.
Conclusion
Precision control transformed two crucial macro industries—medical and industrial automation. Precision motion control is the enabler for both. It improves vibration performance, energy efficiency, noise, and smoothness of motion and significantly reduces the tolerance of automatic movement to enhance its precision.
Industrial automation is propelling Industry 4.0 forward, bringing smart manufacturing technology into the market. Adding precision motion control can unlock 3D printing, CNC machining, pick and place machines, inspection, quality, test equipment, automated assembly lines and conveyors, and collaborative robots. To aid in supply chain and operations, automated guide vehicles (AGVs) and autonomous mobile robots (AMRs) improve productivity and increase product velocity, approaching a just-in-time product flow state.
The content & opinions in this article are the author’s and do not necessarily represent the views of RoboticsTomorrow
Comments (0)
This post does not have any comments. Be the first to leave a comment below.
Featured Product
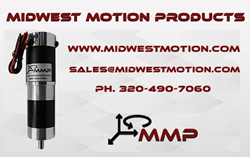