The opportunities, conditions and business advantages offered by properly functioning collaborative automation solutions have never been more attractive, while the technology is also more accessible than ever.
Automation Lends Humans a Hand in High-mix Low-volume Manufacturing
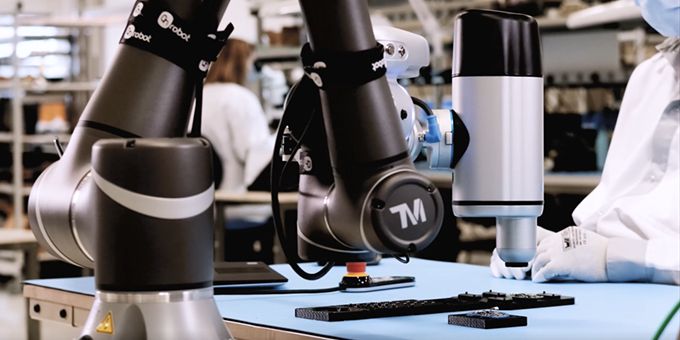
Case Study from | OnRobot
The opportunities, conditions and business advantages offered by properly functioning collaborative automation solutions have never been more attractive, while the technology is also more accessible than ever, there is now focus on the advantages of implementing flexible automation in High-Mix Low-Volume productions. High-Mix Low-Volume (HMLV) Manufacturing, also referred to as make-to-order manufacturing, is the process of producing a high variety of products in small quantities. This production method is often used to handle and produce unique and complex products with specific quality requirements. HMLV manufacturing requires constant changes in jobs, materials, and machines. With a limited number of production lines and a large variety of product requests, operators working in HMLV environments must constantly change the scheduling of jobs and materials, which can often lead to errors and inconsistency in products.
According to research, there are 5 steps to improving the profitability of High-Mix Low-Volume production:
- Utilize Sequential Processing Where Possible
- Stay Simple with Routings
- Implement a Predictable Process
- Create an Open Environment
- Maintain Flexibility
All 5 steps points in the direction that flexible automation can be the right solution for High-Mix Low-Volume manufacturing. Mariachi Oy is an example of a High-Mix Low-Volume manufacturer that implemented flexible automation.
An easy and simple solution for High-Mix Low-Volume manufacturing
Mariachi Oy is an EMS (Electronics Manufacturing Service) company from Turku in Finland. Mariachi Oy is a High-Mix Low-Volume manufacturing company with a clear goal to innovate and digitalize its production processes. For this reason, they decided to implement flexible automation in their production. The project was organized by DIH² and has been funded by Horizon 2020 - the European Union research and innovation programme tasked with bringing great ideas from the lab to market. In the project, the A2CS consortium (Wisematic Oy, Exsensio Oy and Mariachi Oy) adopted an Agile and Adaptable Cobotic System for High-Mix Low-Volume Electronic Manufacturing Industry.
Deployment of multiple collaborative robots onto a production floor for automation can get expensive in a low volume & high mix electronics manufacturing environment. There is a need to assist operators in executing monotonous task without investing in expensive custom infrastructure for the cobot to handle the existing task. For this, a system is needed that can control multiple instruments, industrial equipment’s, and IT systems to execute a given task. Most of the existing production tasks also need a machine vision system for validation. The operators and the management also need to have the ability to monitor the performance of the automated tasks during everyday production runs.
In the project, a Techman TM5-900 collaborative robot with an eye-in-hand vision system along with OnRobot products (RG6, RG2-FT, Dual Quick changer, and a screwdriver system) and Wisematic’s mobile robot platform was used to create a flexible automation system for collaborative and reconfigurable process with the ability to remotely monitor key performance index of different workstations. The developed software solution combined multiple cyber-physical system layers used in this project to control and orchestrate the tasks on the factory floor.
The solution is being flexibly used to automate test and assembly stations inside Mariachi Oy. The mobile cobot system is simply stationed at the designated spot and then the ethernet cable and power supply are plugged in. Once ready, the work cycle is being executed with Exsensio’s proprietary software. At the testing station, the cobot looks for pcba’s to pick up for testing and move them to their appropriate panel/bin based on the test result. After the task at test stations is completed, the mobile robot systems can be moved to the assembly station to execute the final product assembly by choosing the right configuration file in the control software. At the assembly station, the cobot works along with the human operator as this a collaborative work environment. For example, it makes sure the operators have completed certain task and validate it with a robot machine vision system. Exsensio’s proprietary software notifies the operator if the cobot requires operator validation, e.g. to refill components or notify assembly defects. The video shows the flexible solution that was implemented in Mariachi Oy and how it works in their High-Mix Low Volume production. The video has been created by Exsensio ltd.
Jukka Järvi-Laturi, chairman of the board of Mariachi Oy highlights some of the benefits that they have obtained by implementing flexible automation:
“Addressing flexible automation with cobots will increase our products portfolio while still keeping productivity high. We are extremely happy to be an innovator in adopting this technology that will assist our employees in manufacturing.” Jukka Järvi-Laturi, chairman of the board of Mariachi Oy.
The content & opinions in this article are the author’s and do not necessarily represent the views of RoboticsTomorrow
Comments (0)
This post does not have any comments. Be the first to leave a comment below.
Featured Product
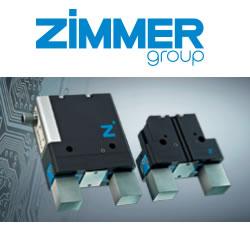