There is a seemingly endless selection of DC, stepper, and servo motor products on the market, each with their own advantages and drawbacks. Going into the selection process having answered a few key questions will vastly simplify the selection process.
How to Select the Best Motor for a Jointed Arm Robot
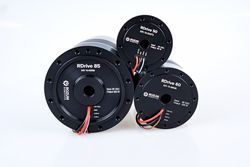
Article from | Rozum Robotics
With their many parts and the need to be able to smoothly rotate all of their axes, jointed arm robots require the perfect actuator to power their specialized movement with the right type and amount of force. Robots with jointed arms are often tasked not only with mundane tasks, but also with performing human-like actions in dangerous or high-stakes environments, so the motor must be perfectly matched to these requirements. There is a seemingly endless selection of DC, stepper, and servo motor products on the market, each with their own advantages and drawbacks. Going into the selection process having answered a few key questions will vastly simplify the selection process.
There are several factors to consider when selecting a motor to power a robot with a robotic joint
1. What type of robotic joints are used? There are five types of robotic joint: linear, orthogonal, rotational, twisting, and revolving. Does your application use the simpler linear and orthogonal joints, the more dynamic rotational, twisting, or revolving joints, or a mixture of both? This will determine the types of motions and the related nuances of their requirements.
2. How much noise is tolerable in the application? If your application will be used in a factory largely away from people, noise may not be an issue. But if it will be used alongside humans for more than a brief amount of time, you may favor a quieter motor.
3. How much precision is required? When a robot is being used to move shelves in a warehouse, not much precision is required, whereas there is no room for error when one is filling prescriptions. Different motors provide precision in different ways, some with distinct disadvantages; it’s important to know which of these may be allowable for your product.
4. How much torque is necessary? Torque can be achieved at various speeds and with varying degrees of constancy. If you need high torque only at a particular speed, you may be able to sacrifice unnecessary torque capability for other motor features.
Now let’s review the three types of electric motors most often used to run applications on a typical jointed arm robot—DC, stepper, and servo—against these considerations.
DC motors come in brushed and brushless varieties. It is commonly thought that brushless DC motors have supplanted brushed ones, but brushed DC motors are still quite popular for some applications. A brushed DC motor is about 75%–80% efficient, achieves high torque at low speeds, and is simple to control, but creates quite a bit of noise due to the brushes used to rotate the machinery. On the other hand, a brushless DC motor is quieter, even more efficient, and can maintain continuous maximum torque, but is more difficult to control and can sometimes require a specialized regulator. Although DC motors usually provide low torque, they can achieve high speeds and are good for washing machines, fans, drills, and other machines that require constant circular motion.
There is always the option of adding a gearbox to the system to create more torque for robotic applications utilizing a robotic joint mechanism. Keep in mind, the motor and gearbox should be designed to work together, so purchasing a motor with an integrated gearhead is a good idea in this case.
Stepper motors can control precise movement, have maximum torque at low speeds, and are easy to control, making them popular in process automation and some other robotics. However, they come with several drawbacks: They are noisy and relatively inefficient, and they run hot since they continuously draw maximum current. Finally, since they have low top speeds, they are known to skip steps at high loads, which can be a critical flaw in some jointed arm applications. Despite these limitations, they have proven effective in medical imaging machines, 3D printers, and security cameras.
Servo motors provide extremely precise movement, thanks to a feedback loop that senses and corrects discrepancies between actual and target speed. They can provide high torque at high speeds, and can even handle dynamic load changes. Additionally, servo motors are lightweight and efficient. Downsides of using servo motors include their possibility for jitter as they respond to feedback and their requirement for sophisticated control logic. Despite these drawbacks, the precision offered by servo motors often make them a good option for a jointed arm robot, the sophisticated movement of which is designed to match that of humans!
Your jointed arm robot may perform sensitive tasks and come with high expectations, so you need a motor that not only powers your system but makes your robot maximally appropriate for the environment in which it operates. When selecting a motor, making sure you know exactly what you’re trying to achieve and ranking your priorities will help you make smart functionality tradeoffs for optimal performance and suitability.
The content & opinions in this article are the author’s and do not necessarily represent the views of RoboticsTomorrow
Comments (1)
Featured Product
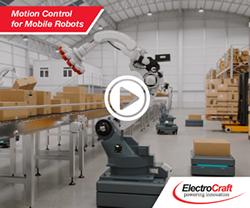