Robotic dress packs are tasked with protecting, managing, securing and guiding cables and hoses over millions of work cycles. These high demands place an enormous amount of stress on every component within the system.
Robotic Dress Pack Component Basics
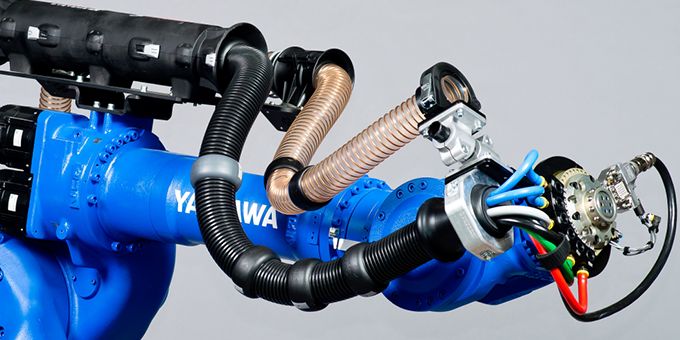
Keith Wilkerson, Business Segment Manager Robotics & Automation | Helukabel
PROTECT – MANAGE – SECURE – GUIDE: Dress packages (a.k.a. dress outs, umbilicals, utility supply systems, etc.) provide an organized way of protecting the fill package from environmental hazards. This helps reduce time spent on preventative maintenance. Any industrial robotic application where an End Of Arm Tool (EOAT) needs various supply lines such as servo power, welding power, water supply, ethernet communication, etc. would be in need of a dress pack
Robotic dress packs are tasked with protecting, managing, securing and guiding cables and hoses over millions of work cycles. These high demands place an enormous amount of stress on every component within the system. Unfortunately, failures will occur. It’s a matter of when, not if a problem will arise. Over 85 percent of robotic downtime is attributed to fill package failures. In order to mitigate failures in the best way possible, it is important to select solutions from an application specific, as well as an overall system, point of view. In other words, each robot has a task to perform. Therefore, dress packs should be specifically designed around the complete work cycle of each task. Many companies have “ready to install” systems based on a robot model; some have online design tools. However, these should only be considered as a starting point because the solution suggested may fit the robot but may not fit the application. Think of it this way, we wear different clothes based on the task or event, like mowing the lawn or going to a birthday celebration. Correct? You didn’t change but the “application” did.
Read on as we explore some of the main components that make up a dress pack and explain the role they play in the protective system for your specific fill package.
CORRUGATED TUBING / FLEXIBLE CONDUIT
This is the first line of defense in protecting the fill package. The corrugated tubing covers the cables and hoses for the majority of their length starting at the base plate below Axis 1 to their exit at Axis 6. The most widely used material is polyamide (PA12). Plastic (PV), polyurethane (PU), and other materials can be utilized based on the environment and/or the application. It is important to allow enough slack in order to avoid catastrophic failures, unnecessarily exposing the fill package (see figure 1).
SYSTEM HOLDER
This one piece system joins the corrugated tubing to the metal support brackets or pipe holders. It can be installed in a fixed position or on a pivot bearing/rotating flange allowing movement when needed.
ARTICULATING JOINT 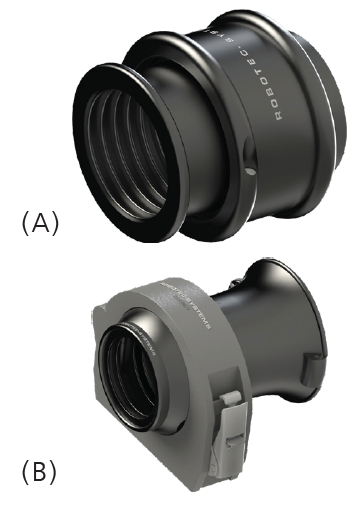
Articulating joints are used when spherical movement of the corrugated tubing is needed at Axis 6. Structurally, the articulating joint must be very robust in order to withstand the mechanical stress it will endure. Two styles of joints are seen in the field.
(A) The two-piece joint offers angular movements ranging between +/- 11°.
(B) An additional type is the ball and socket. Similar to a Heim joint, ball joint or gimbal, it provides spherical “relief” at the exit point of the fill package. It offers angular movements ranging between +/- 15°.
SPRING RETURN SYSTEM - ENCLOSED
Sometimes called a spring retreat or recirculation system. The spring return system allows safe movement of the service loop portion of the corrugated tubing between Axis 3 and Axis 6.
The ROBOTEC SYSTEMS version — the Ro-Box — can be stacked three high with no additional support bracketry, employs a more efficient/durable compression spring technology, and has three spring tension specifications to match force calculations based on the fill package. Additionally, it utilizes the “quick clip” system, which are plastic clips that connect the half shells of the Ro-Box. This allows for quicker installation and changeout of the essential dress pack components (corrugated tubes, fitted wires/hoses) without tools or other hardware.
SPRING RETURN SYSTEM - EXTERNAL
Operates on the same concept as the enclosed system without the addition of the energy tube. The external system is less robust; therefore, it’s typically used for vacuum tubing or when lighter hoses are added to accommodate EOAT retrofits.
TRUMPET
Used for guiding corrugated tubing as well as part of an external spring return system. The trumpet can be secured to a pivot bearing when movement is needed in the midsection of a corrugated tubing run.
RING CLAMP WITH PIPE
This metal support item secures the dress pack to Axis 6 with the use of a pipe clamp. Typical failures are weld breakage and bending of the pipe section.
These failures could possibly cause irreparable damage to the EOAT. It is also referred to as the tennis racket, frying pan and/or wrist support within the industry.
PIPE CLAMP
Connects and secures the system holder to either an Axis 6 ring clamp or a precision tube. The mounting flange serves as a holder for the pivot bearing and base plate.
CABLE & HOSE STRAIN RELIEF
This is widely know as a cable star. It is essentially a custom engineered grommet, similar to a multi-hole cable gland, that is placed at each end of a corrugated tubing run. This ensures the fill package is securely held in place and minimizes lateral push/pull movement. Due to the variations of fill packages, this component is custom designed and cut to each dress pack.
ADAPTER PLATE
Secures the system holder to a pipe clamp. Multiple holes are drilled and tapped allowing the system holder to be placed at an optimum angle. This decreases stress on the corrugated tubing.
IMPACT PROTECTOR
Used to minimize wear and tear of the corrugated tubing as it “snakes” over the robot arm. It can also be utilized in repair situations as a way to connect two pieces of corrugated tubing. It is important to consider using versions without screws as this will damage the paint and sometimes the robot’s aluminum casting (figure 2). HELUKABEL offers the “quick clip” system, which secures the two halves without tools, and can rotate freely on the corrugated tube (figure 3). The same clip system is employed on the Ro-Box enclosed spring return system.
METAL SUPPORT BRACKET
The metal support brackets ensure the foundational strength of any dress pack system securing the entire system to the robot castings. Structural grade steel such as 1.0037 or A36 should be utilized. Aluminum extrusions are less expensive, but will fail prematurely.
STRAIN RELIEF RETAINER
This component marries the corrugated tubing or the system holder and the cable star. These are installed on each end of the robot.
PRECISION TUBING
Galvanized steel pipe utilized when metal brackets are not cost effective or may restrict movement of the dress pack. Most often used when a secondary dress pack bypasses the base plate of the robot.
Click here to download the PDF
The content & opinions in this article are the author’s and do not necessarily represent the views of RoboticsTomorrow
Comments (0)
This post does not have any comments. Be the first to leave a comment below.
Featured Product
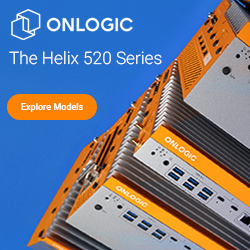