Downtime is particularly costly in an operation that relies on carefully coordinated logistics, so optimizing charging times and speeds based on operational needs is very advantageous.
Wireless Charging Technology for Autonomous Robotics
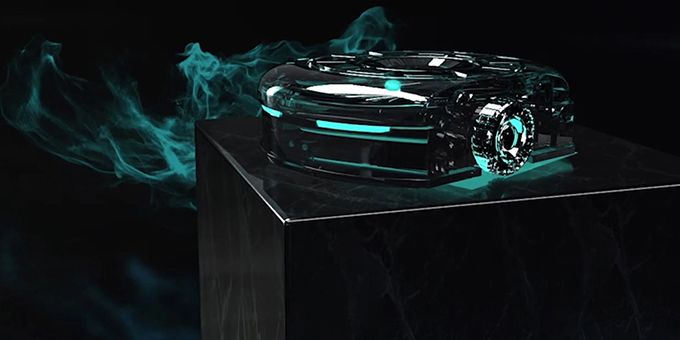
Q&A with Aya Kantor, VP of Product | Powermat
Tell us about yourself and Powermat.
I’m the VP of Product at Powermat where I’ve worked for nearly 10 years, leveraging my expertise in multidisciplinary product development, image processing and data analytics. Powermat has been the perfect place to bring my passion bringing game changing new products to market.
Powermat designs B2B wireless power and wireless charging platforms. We are focused on transforming how industries keep devices powered with end-to-end software-based wireless power platforms that enable autonomous, mobile, and connected technologies.
When Powermat started, the wireless power industry was still maturing and most of the applications were in the consumer space. For example, we worked with Starbucks to offer their customers wireless charging in stores. As technology has advanced, so have the applications for wireless power. Today as the industry has expanded and the benefits are more readily understood, Powermat is applying its advanced technology to benefit the 5G, IoT, and robotics markets and our innovation roadmap reflects this.
How does wireless charging work? Is wireless charging more efficient than wired charging?
Wireless charging is based on magnetic induction. Magnetic induction is a means of creating an alternating electromagnetic field to safely and efficiently transfer energy between a transmitter unit and a receiver unit, both of which contain an induction coil. When placed near the transmitter, the receiver unit receives the electromagnetic field and converts it into power. Using in-band or out-of-band signaling to communicate, the two units can regulate power levels and manage the power transfer accordingly.
There are three primary approaches to wireless charging: tightly coupled inductive charging, in which the transmitter and receiver need to be tightly coupled and in close proximity with each other for the energy transfer to occur; loosely-coupled resonant charging that can transmit power over distances and in higher misalignment (a few inches at most); and Powermat’s SmartInductive™ solution, which bridges the gap between classic inductive charging and resonance to leverage the best of both worlds, delivering more power, more freedom of positioning, with longer range between the transmitter and receiver - all at a lower cost of implementation.
How are you seeing wireless charging being used on the manufacturing floor with mobile robots?
Whether purposed for cleaning or handling a large facility’s logistics, manufacturers use autonomous mobile robots to boost operational efficiencies and reduce labor costs. But many mobile robots with self-charging capabilities used in manufacturing have trouble docking properly or require costly alignment mechanisms – leading to high cost of ownership, inefficiencies, increased downtime, and additional human intervention and repairs. Downtime is particularly costly in an operation that relies on carefully coordinated logistics, so optimizing charging times and speeds based on operational needs is very advantageous.
Powermat’s wireless charging technology drastically simplifies the docking process by making it unnecessary for robots to dock precisely at a charging station, eliminating the need for pogo pins, or any manual human interference. It can also provide optimization of the charging process to make sure each device is charged at the optimum voltage and current, which prolongs battery life and avoids costly battery replacements and is really helpful for distributed robot fleets. As a result, users benefit from enhanced reliability and productivity of operations and avoid unexpected costs.
Why do you feel robotics manufacturers and companies utilizing mobile robots should invest in wireless power?
For organizations to get the most return on their investment in autonomous solutions, service robots should always be able to complete their task autonomously and recharge quickly without human intervention and maintain battery health over time. Enabling flexible and efficient wireless charging for commercial and industrial robotics offers the last missing piece of the puzzle to enable full robot autonomy.
Can you give an example of how Powermat’s technology is benefiting commercial robots?
Absolutely. We partnered with Jetsons Robotics to help design wireless charging stations for their autonomous rooftop solar installation cleaning robots. Cleaning rooftop solar installations can cost companies anywhere from $100,000 to $500,000 per year but replacing human labor with robots dramatically cuts down on these costs if they operate efficiently. That’s where wireless charging comes in. Plug-in or contact-based charging is too tricky in outdoor environments, but an inductive charger would be costly and the misalignment support due to environmental and mechanical conditions insufficient. That’s why our magnetic induction charging technology, Powermat SmartInducitve, ended up being the best fit. Now these robots can operate at maximum efficiency, cleaning roughly 1.7 megawatts of solar installations on a daily basis.
Tell us about your new robotics power platform and how it is different from the technology you were offering to Jetsons Robotics? What are the key features of the platform?
While Powermat has been working with robotics companies such as Jetsons Robotics on custom solutions for several years, this new platform is designed to suit a wide range of robot types, power levels and use cases. It includes features such as advanced communication, beaconing for improved robot alignment, greater misalignment flexibility, and power ranges that can service a greater scale of robotics fleets. We developed the platform with extensive feedback from customers and we believe it offers the best in class wireless charging solution for this market.
What is the future of wireless charging related to robots?
Robots are moving well beyond factory floors. A new wave of robotics has begun, and we’re seeing adoption in more industries than ever before, such as healthcare, retail, hospitality, agriculture, logistics and manufacturing. Consider that the global market for AMRs was worth $1 billion in 2017, and it’s now forecast to hit $7 billion this year. Wireless charging technology will give robotics manufacturers a competitive edge. Our commercial robotics platform makes it easier and more cost effective than ever before to implement wireless charging capabilities, and it’s incredibly powerful - working even in the most adverse conditions. As more industries turn to robots to overcome labor shortages and improve productivity and safety, I think wireless charging will become an essential component.
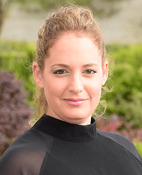
Aya Kantor joined Powermat in 2012, bringing with her over 15 years of product experience in the fields of multidisciplinary product development, image processing, and data analytics. Prior to joining Powermat, she held multiple product management and product marketing roles in leading global companies, such as Applied Materials and NICE.
The content & opinions in this article are the author’s and do not necessarily represent the views of RoboticsTomorrow
Comments (0)
This post does not have any comments. Be the first to leave a comment below.
Featured Product
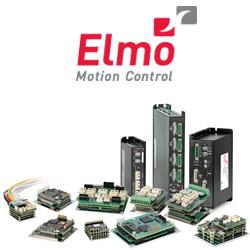