Advances in semiconductors have led to dramatic developments in a wide range of sensor and camera technologies, including sensors/cameras for area scan and line scan, IP/network, 3D, and thermal imaging platforms.
How Computers Deliver the Ability to See
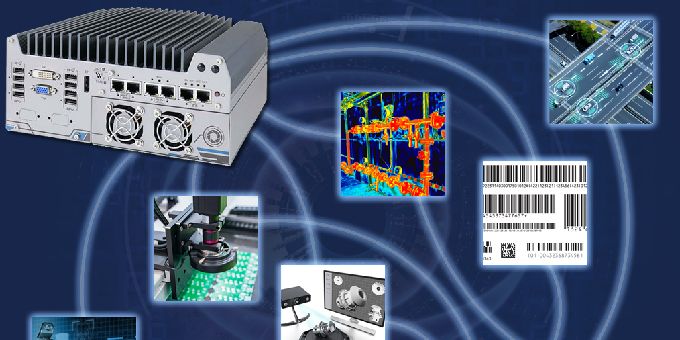
Article from Scott Hartman | COAST IPC
Advances in semiconductors have led to dramatic developments in a wide range of sensor and camera technologies, including sensors/cameras for area scan and line scan, IP/network, 3D, and thermal imaging platforms. Many of these new devices, when coupled with robust computing power, are driving improved efficiency in automation, robotics, safety, security, health care, and more.
Here are a few notable applications that demonstrate how far the reach of computer vision and machine vision is in our world:
- Material handling, mail and package sorting, order fulfilment
- Surveillance and security, critical infrastructure, and asset monitoring
- Smart cities, automatic tolling systems, access control, and traffic monitoring
- Inspection and quality control, real-time factory process control
- Surgical robotics, medical imaging, health-care diagnostics
- Autonomous and semiautonomous vehicles such as cars, trucks, buses, taxies, boats, drones, and automated guided vehicles
Industrial PCs (rack-mounted units, edge AI devices, compact embedded fanless systems) are also improving as fast as Intel and AMD develop new CPUs. Depending on the application, systems can consist of a single sensor/camera and a small edge PC or a large, fully integrated multiple PC configuration with various types and quantities of sensor/camera technologies. Following is a useful checklist of considerations when selecting an industrial PC selection for machine vision or computer vision applications.
Machine Vision Application Checklist for Industrial PCs
Environment: When selecting a PC, a great place to start is by considering where the computer will be located. Consider space and mounting/installation requirements to ensure the PC will fit. Ventilation also deserves attention. Small embedded systems to larger 4U rack-mounted systems all have different ventilation and/or cooling capabilities. Many industrial applications do not require wide temperature or shock and vibration considerations. However, vehicle-based projects, some surveillance and security, as well as outdoor deployments often need extended temperature, vibration mitigation, and/or ingress protection. Todays embedded systems offer a wide range of configuration options for environmental protection. However, all sublevel components of a “system” (memory, storage, graphics cards, and so forth) must also meet the very same parameters.
Industrial PC I/O and connectivity: Adding the selected camera or vision sensor to the PC can be as simple as installing the device(s) and supporting hardware. Common device interfaces include USB ports, GigE ports (RJ45 or M12 connections), and PoE options. Additional hardware cards can be installed by way of available M.2, PCI/PCIe, or other interface methods. Integrators must ensure that the industrial PC they choose offers the right I/O for the task at hand.
Special attention should be given to GPUs, VPUs, frame grabbers, and custom network interface cards (NICs) to ensure that physical size, interface, and power connections are compatible with the PC (PCIe Gen size and number of slots and power connections are all common fitment concerns). Other considerations include whether the system will require additional communications ports (RS-232/422/485) antennas, or wireless/cellular/satellite connection.
Compatibility, updates, and custom images: Installation and testing plays a major part in successful deployments. Experienced integrators must ensure that the subcomponents, operating system, optional expansion boards, and related software drivers are all properly installed, updated, and stress tested (burned-in). OEM systems can be reliably and securely duplicated (imaged) at the integrator level for repeat installations.
While not a comprehensive checklist, these considerations will put systems integrators and OEMs on track for selecting the right industrial PC for their machine vision or computer vision application. Contact CoastIPC today at info@coastipc.com if you have specific computing needs in your machine vision applications.
The content & opinions in this article are the author’s and do not necessarily represent the views of RoboticsTomorrow
Comments (0)
This post does not have any comments. Be the first to leave a comment below.
Featured Product
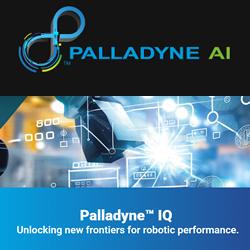