The next generation of robotic systems require high performance inertial sensors but also demand high volume, low cost solutions.
High Performance Inertial Sensors for Robotic Systems
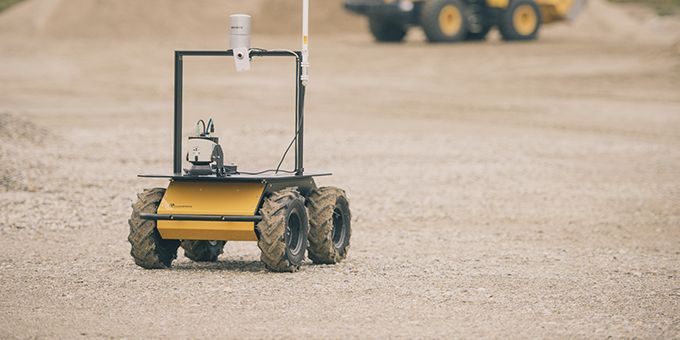
Q&A with Jonathan Bessette, PhD, Staff Engineer | Parker
What is the 3DMCV7?
The 3DMCV7 is Parker's latest addition to our line of MicroStrain inertial sensors. It is specifically designed for high volume OEM robotics applications, introducing tactical grade gyro performance at a fraction of the typical cost.
How does the 3DMCV7 improve upon the previous generation 3DMCV5?
The 3DMCV7 offers improved capability in nearly every critical OEM IMU performance specification. Size, weight, power and cost have all been significantly reduced. In addition, a new tactical grade gyro design with 1.5°/h bias instability provides a 5x improvement in noise performance over the 3DMCV5. We’ve also added a host of new features, including a ground-up redesign of the state estimation filter for more robust attitude and bias tracking, a precision timing engine, user selectable sensing ranges and continuous internal health monitoring.
You tout a new timing engine capability, why is timing so critical for an AHRS?
Timing accuracy is often overlooked, but is fundamental to performance when using inertial sensors in a navigation context. MEMS inertial sensors are fundamentally angular rate and acceleration sensors, and are integrated with respect to time to measure changes in angle and velocity. Any error in the time interval used for integration is directly manifested as scale factor error in the integrated quantity. When using an IMU with other complementary sensors in a sensor fusion context, it’s critical to time align all sensor measurements to a consistent time base to minimize inertial integration error.
The 3DMCV7 employs several technologies to mitigate these timing errors. First, all sensor subsystems are sampled with microsecond level precision and internally aligned to the master system clock, removing errors such as measurement and communications latency. Second, a new event-based triggering system has been developed for time synchronization with external measurements devices, such as cameras. The 3DMCV7 can input and output digital synchronization signals that are time aligned with the internal sensor measurement stream. For example, the 3DMCV7 can be connected to a camera shutter signal and sample precisely at the moment an image is taken. Many visual navigation systems rely on host PC timestamping for measurement alignment, which can result in measurement timing error on the order of tens of milliseconds when using non deterministic communication methods like USB. With hardware synchronization methods enabled by sensors like the 3DMCV7, timing errors can be virtually eliminated from the sensor fusion problem.
Many other MEMS vendors have solder down modules for their OEM designs. Why does the 3DMCV7 use an aluminum case for mounting?
Solder down modules do have some benefits when it comes to manufacturing and size, but these benefits come at the cost of inertial performance and flexibility. Performance can be negatively impacted for two main reasons: board stress and calibration accuracy. Inertial MEMS components are highly susceptible to package stress, which can be introduced by the soldering process or thermal expansion of the host PCB during temperature cycling. The precise CNC machined aluminum case in the 3DMCV7 works to isolate the sensing components from the end users PCB, maximizing performance in all designs. It also provides consistent, precision mounting between the temperature calibration process at our factory and the end user installation. Solder down modules do not provide precision mounting features to ensure repeatable alignment, introducing misalignment errors in the end application. Finally, the 3DMCV7 design gives the user flexibility in mounting. It can be both chassis and PCB mounted, giving the end user design freedom to place the IMU in locations where there is no PCB.
What are some of the benefits of your new state estimation filter design?
The state estimation filter in any AHRS is responsible for combining data from angular rate sensors and accelerometers, as well as data from magnetometers and sometimes other sources, to give a continuous estimate of attitude and heading. Estimates of other states can be tracked as well, such as gyro and accelerometer bias errors. A good filter will be tuned to give a balanced response, one that is smooth and accurate at all time scales. The optimal tuning depends on the characteristics of the sensors, but is also highly dependent on the platform dynamics during operation. Lateral accelerations (e.g. from a vehicle cornering at speed) or platform vibrations are common examples of application dependent dynamics that affect AHRS filter tuning. The 3DMCV7 uses robust adaptive filtering to automatically compensate for these changes, rejecting measurement outliers and adjusting for platform vibration, with no active tuning required from the user.
Sensors are constantly getting smaller, lighter, and more efficient. What have you done to stay ahead of the competition in the SWaP-C (size, weight, power, and cost) specifications?
The 3DMCV5 was already an industry leader in many of the SWaP-C categories, and the 3DMCV7 improves upon these specifications even more. The next generation of robotic systems require high performance inertial sensors but also demand high volume, low cost solutions. Until the 3DMCV7, the tactical grade performance needed for these applications wasn’t achievable in a low cost OEM sensor. We’ve also focused on optimizing and lowering the power consumption of the 3DMCV7. Mobile robots are generally operating on batteries with tight power budgets, requiring low power sensing subsystems to improve operational life per charge. Finally, we took the already small form factor of the 3DMCV5 and removed even more size and weight, responding to the needs of our weight conscious aerial customers.
You can find more information about the 3DMCV7, as well as all other inertial sensing options, on the MicroStrain website, Parker 3DMCV7 Product Page.
About Jonathan Bessette
Jonathan Bessette, PhD is a Staff Engineer at Parker and has worked on development of the MicroStrain inertial sensing and navigation products since 2014. His expertise includes inertial system design, analysis, and calibration, as well as sensor fusion techniques including adaptive Kalman filtering and tightly integrated GNSS-INS navigation.
The content & opinions in this article are the author’s and do not necessarily represent the views of RoboticsTomorrow
Comments (0)
This post does not have any comments. Be the first to leave a comment below.
Featured Product
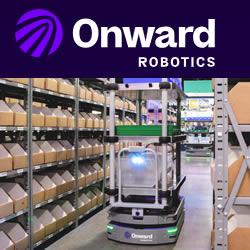