Harmonic Bionics has developed a patented robotic actuator, which uses a load cell that is mechanically isolated from any extraneous loads. The result is that each load cell can sense the force exerted by only the joint of the robot it is mounted to.
Medical Exoskeleton for Rehabilitation
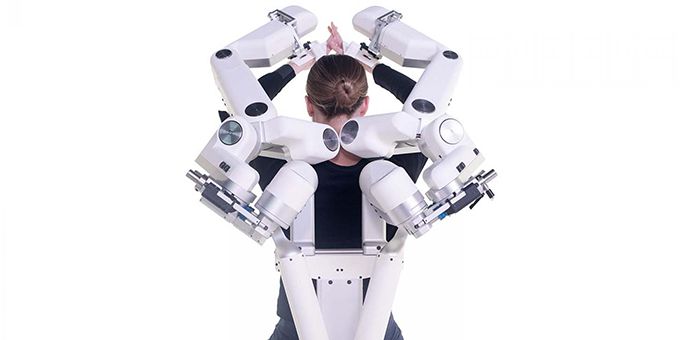
Article from | maxon group
The goal achieved was to provide an intelligent, data-driven treatment therapy for dealing with neurological and musculoskeletal movement impairments.
The primary aim for Harmonic Bionics is to empower patients and care providers by designing intelligent technology that facilitated a data-driven treatment protocol when dealing with neurological and musculoskeletal movement impairments. To this end, the company was responsible for the complete design and assembly of their Harmony SHR™ bilateral upper extremity exoskeleton.
By enabling early intervention, functional repetition, and intent-based therapy, Harmony SHR delivers users the ability to improve the efficiency and effectiveness of upper-body rehabilitation. As the company’s flagship product, the Harmony SHR is designed to provide unique value in three areas of practice: neuroscience and movement science research, movement disorder assessment, and rehabilitation. Harmonic Bionics has selected commercial off-the-shelf (COTS) components to integrate into their various robotic actuators according to each actuator’s requirements to simplify product design efforts. The company did have to make minor tradeoffs in the design phase, at times, for instance between actuator size and load capacity/weight, and between maximum torque and torque sensitivity. The end product is strong enough to assist with physical exercises while not being too heavy or cumbersome to use.
Typically in robotic arm applications, people have to be separated from robotic arms so that the robot cannot injure a person while moving. Most robotic arms on the market are not designed to interact with humans safely – they cannot detect a person in their way or move around a person while performing the programmed task. Due to this, typical robots could be very dangerous for people to interact with, especially in a physical therapy application. This is not a problem with the Harmony SHR, which has been designed to be force sensitive and to be controlled by force inputs from users instead of the position setpoints typical of most robotic arms.
To assist patients with exercises, it is much more important for the robot to apply exact forces to the patient rather than position them accurately (see Figure 1). The robot has been designed with compliance in mind so that even small forces applied to the robot can cause the robot to move out of the way, to slow down, or to stop completely. This feature makes the robotic exoskeleton extremely safe to be in and around.
This force sensitivity necessitated a redesign of typical robotic actuators. Harmonic Bionics has developed a patented robotic actuator, which uses a load cell that is mechanically isolated from any extraneous loads. The result is that each load cell can sense the force exerted by only the joint of the robot it is mounted to, while being isolated from the forces being applied to others, thus maximizing the sensing accuracy of the load cell. ESCON controllers, manufactured by maxon were compact in size and easy to integrate electrically and physically (see Figure 2). We found that the software was straightforward to use. The motors had informative datasheets which made them simple to integrate. We have rarely had to revise our motor selection because the datasheets help us make the correct motor decision the first time.
Actuators used in the Harmony SHR exoskeleton are either rotary actuators with torque and angle sensing output used to assist with patient motion, or linear actuators with position feedback used to resize the robot to fit a patient. The exoskeleton is designed to provide objective assessment of a patient’s movement capabilities. The system incorporates over 80 sensors that record measurements 2,000 times per second, allowing it to precisely measure multiple parameters, including range of motion, force generation, and number of repetitions.
The motion system uses several motors designed and manufactured by maxon. maxon was able to supply motors that satisfy a wide variety of unique needs of the system. For example, EC Flat motors provided the high torque output needed in a compact package that fit the exoskeleton’s compact size (see Figure 3). The flat motors could also be supplied with angle sensors.
An EC 60 Flat motor was selected because the outer diameter was similar to that of the harmonic drive and because they are axially compact. The shaft of a maxon EC 60 DC Flat motor is attached to a wave generator of a size 17 harmonic drive, which was selected for its compact axial size and high torque capacity. Harmonic drive gear reducers offered the high reductions, low backlash, and high torque capacity the company needed for the design.
The stator of the maxon motor is mounted to the circular spline of the harmonic drive. The flex-spline of the harmonic drive is attached to an output shaft supported by a crossed roller bearing, which supports all loads that are not the torque output of the actuator. Because the crossed roller bearing supports the other loads, the only load that acts on the load sensor is the torque output of the load sensor.
The maxon motor, output shaft, and harmonic drive assembly are free to rotate in the crossed roller bearing. A bracket is attached to the circular spline of the harmonic drive and to the stator of the maxon motor. A load sensor is attached to the bracket so that output torque of the overall assembly can be measured through the load sensor.
The alignment of the harmonic drive to the shaft of the maxon motor is very critical to the life of the actuator. Even a minor misalignment can cause premature wear or failure of the mechanism. Therefore, the machined components are manufactured to be parallel to within about 20 microns while concentricity is maintained within about 30 microns to align the circular spline to the maxon motor. The overall footprint of the actuators inside the robot is approximately 80 mm in diameter and 90 mm in length. The machined components that go into each actuator are made from various fatigue resistant aluminum alloys, and grade 5 titanium where stresses are high.
The output torque of the overall actuator is approximately 30 Nm, and the actuator can output over 100 Nm peak. The actuator is attached to an extremely sensitive load cell, which has a resolution of less than 10 mNm. Each actuator is designed to have a life of over 3 million revolutions.
Conclusion
The actuators used in the Harmony SHR are of a mature design and are expected to need few improvements in the future. According to the company, it is unlikely that they will be changing any of the COTS components during future revisions, particularly the maxon components. maxon’s DC motors were highly configurable, plus the company offered low backlash versions of gear reducers for use in the rotary actuators, as well as small diameter brushed dc motor + planetary gearbox combinations to create compact rotary actuators. The company’s leadscrew gear reducers were also available to use in linear actuator applications. All this is to say that maxon was able to supply all the motors and controller needed for the application, providing Harmonic Bionics with a reliable single supplier.
The content & opinions in this article are the author’s and do not necessarily represent the views of RoboticsTomorrow
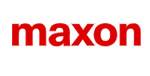
maxon group
maxon is a leading supplier of high-precision DC brush and brushless servo motors and drives. These motors range in size from 4 - 90 mm and are available up to 500 watts. We combine electric motors, gears and DC motor controls into high-precision, intelligent drive systems that can be custom-made to fit the specific needs of customer applications.
Other Articles
Multi-axis motion control drives pipe-based robots
Automate 2025 Q&A with maxon group
Understanding Torque and Speed in Electric Motors
More about maxon group
Comments (0)
This post does not have any comments. Be the first to leave a comment below.
Featured Product
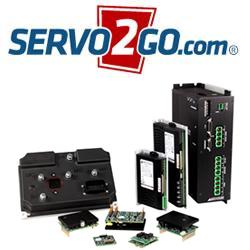