We have been hearing a lot about AGVs and AMRs in warehouses and fulfillment centers. But do you understand the differences between these two? Let’s find out from the experts.
What’s the Difference Between AGVs and AMRs?
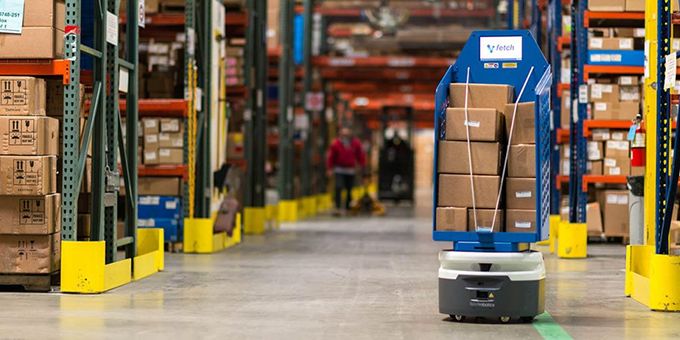
Q&A from David Lin | Zebra Technologies
But how exactly are AMRs different from AGVs? (They are technically both mobile robots.) And why should you consider AMRs over AGVs for your facility for material handling? We’ve asked one of Zebra’s robotics experts, David Lin, to help answer these questions and many more…
Your Edge Blog Team: What is the most fundamental thing that differentiates AMRs from AGVs? For people who have been using AGVs in their facility, how would you explain AMRs to them?
David: The fundamental difference lies in the name itself: one is a guided vehicle while the other operates autonomously. AGVs follow a fixed route inside your facility, usually along wires or magnetic tape embedded in the ground. AMRs have the ability to replan their routes and can navigate dynamically using a digitized facility map that you create during the initial setup.
Apart from that fundamental difference, what stands out most for me is the obstacle avoidance technology built into AMRs. They can see an obstacle – either stationary or moving – and move around it to complete their designated task. AGVs, on the other hand, can only perform collision avoidance. AGVs sense an obstacle but they just stop and wait until that obstacle is removed by someone.
Your Edge Blog Team: Sounds like AMRs are very intelligent robots! How exactly do they avoid obstacles? What happens if there isn’t enough space to pass through without hitting an obstacle?
David: An AMR knows its destinations, so it can change its route to reach wherever it is supposed to go. For instance, in Google maps you can see many routes to reach your destination and you take the one that’s most suitable for you, whether it’s to avoid traffic congestion or accidents. Similarly, when an AMR senses an obstacle in its way, it can turn around and take another route if it is unable to bypass obstacles safely.
In fact, an AMR can even avoid moving objects, as it is equipped with sensors, 3D depth cameras, and LiDAR technology to ensure the safety of people around it. These sensors work together to facilitate vision and smart identification of both static and dynamic objects within the robot’s field of view.
Your Edge Blog Team: You mentioned the need for magnetic tapes and wires for AGVs. Do businesses have to make a lot of infrastructure changes to deploy AMRs as well?
David: For AGVs, you need to create a route in your facility using tapes or wires or beacons, and they are restricted to this fixed path when completing tasks. They can’t steer off the path for any reason.
For AMRs, you don’t have to make these physical infrastructural updates because the robot knows where it is physically through a process called localization. AMRs will scan the environment as they move and match these scans to a stored map. AMRs can take multiple routes to complete their tasks; you just need to create a map of your facility on the robotics software. Within the software you can specify preferred AMR travel paths, keep-out zones, and even control the speed limit when an AMR enters a designated area.
In terms of the IT infrastructure, if you’re using cloud-based AMRs, they can work with any facility's existing Wi-Fi networks. And since workflows are built on software using drag-and-drop features, just about anyone can work with these AMRs. You don’t have to be an IT expert or robotics engineer to use these robots. And once you’ve mapped your facility, it’s easy to scale as needed by adding more robots to help with seasonal spikes, for example.
Your Edge Blog Team: Would you then say it is easier to work with AMRs than AGVs?
David: There are two parts to working with these robots — one is the initial set up and the other is collaboration. To set up an AGV, you need certified engineers who know how to adapt it to your infrastructure properly. An AGV operates much like a train on a track that has multiple stops, so you need experts to determine the right path and the right stops if you want to make your operations efficient.
The set up for an AMR is much simpler: you just have to create a digital map in the robotics software by scanning your facility with the AMR. Generally, there’s no other fixed infrastructure to install. You can also update this map anytime by re-scanning the space. You can even program complex conditionals for the AMR using the same software. For instance, if an AMR has a task to pick up a cart and finds nothing at its destination, you can build conditions like “go to another station to pick up packaging material.” This helps maximize robot utilization.
Now on to the collaboration side of these robots. AGVs are meant to load and unload material on a single route. That’s it. AMRs were designed to work with people either via a built-in touchscreen or a handheld scanner, wearable, or another smart device. You can have multiple applications with AMRs, which makes them more flexible. AMRs can even direct warehouse employees on where to pick, what to pick, and where to place picked items with the help of interactive devices and dynamic LED lighting. There’s so much possibility for collaboration between humans and AMRs.
Your Edge Blog Team: In terms of safety, how do AGVs compare to AMRs? Are AMRs safer because they have obstacle avoidance technology?
Ans: One of the best things about AMRs is that they’re specifically designed to work around people, so in a way, the robots are “trained” to avoid obstacles like humans. In the case of AGVs, it’s more practical to train employees to avoid the robots through general awareness and creating visual boundaries. That’s why the usual practice in facilities that use AGVs is to train people not to walk across an AGV’s path, just like you would tell kids not to cross train tracks unless it’s safe!
As you mentioned, AMRs are smart enough to avoid obstacles of all kinds including people, forklifts, carts, racks, boxes, and just about anything that it could encounter thanks to the way AMR providers are designing intelligence into these robots. For instance, cloud-based AMRs can leverage machine learning algorithms to identify different types of material handling equipment and then modify their movement behavior to optimize safety with efficiency.
In fast-paced environments, lift trucks, humans, and robots are moving in the same aisles at the same time. With these new learning capabilities, AMRs can move safely around forklifts, manual carts, people, and pallet jacks. This enables a fulfillment or distribution operation to run both automated and manual tasks within the same aisle, such as replenishment, let downs, order picking, and case picking.
Your Edge Blog Team: One of the major concerns with any new technology is the time required for deployment. Whether it’s a manufacturing business or a 3PL, nobody can afford downtime as it hurts their business, especially these days. Demands are growing and lead times are shrinking. So, how does deployment work for AMRs versus AGVs? What’s the typical lead time?
David: Because of user-friendly robotics software and simple interfaces that are used to create a facility map, it is possible for AMRs to be deployed within a few days. Even with a complex warehouse management system (WMS) and warehouse enterprise system (WES) integration, AMRs can be configured and deployed in weeks – not months, which is more of the “norm” for AGVs.
To deploy an AGV, you must plan out your facility and space. You must ask questions like: “Do we need infrastructural changes?” and “Can these AGVs fit in our aisles?” Also, once you deploy AGVs, it’s not easy to change the routes. You have to redo the planning and embed magnetic tapes on the new route. So AGVs take much longer to deploy and are not as flexible.
Your Edge Blog Team: What about maintenance? Should organizations expect a lot of wear and tear with mobile robots?
David: Routine maintenance of the robots themselves is generally minimal, such as servicing the wheels and batteries when needed. However, if your AGV uses some form of magnetic tape that is laid on concrete flooring, you typically need to invest more time and effort in maintenance. These tapes are fragile, with people pulling pallet jacks over them all the time or forklifts driving across them. This amount of traffic can damage the tapes, so you need to maintain these regularly. If there’s any damage, the AGVs can stop and are effectively immobile until the tape is repaired.
Since there’s no tape required for AMRs to navigate, there's less chance of interruptions to the material flow caused by damaged guidance infrastructure, and less to maintain.
Your Edge Blog Team: What is the typical investment required for AGVs vs. AMRs? And is there a difference in the anticipated return on that investment?
David: Some people believe that because AMRs use advanced cameras, laser sensors, and hardware, they are automatically more expensive than AGVs. However, AMRs can be a much smaller initial investment than AGVs if you consider a subscription model, and that lowers the total cost of ownership (TCO). In fact, the Robots-as-a-Service (RaaS) model is becoming a popular option among manufacturers, distribution centers, and 3PLs who are looking for a predictable cost model, and the flexibility to scale as needed. It allows them to change robot types if their operations and payloads change. Plus, with RaaS, everything needed to automate facilities is included, such as regular maintenance, service and support, over-the-air software updates, and of course, the use of AMRs.
Due to the rapid deployment of AMRs, you can also realize a faster return on investment compared to AGVs. If you do an out-of-the-box deployment (when integration is not required), you do not have any IT burden or cost with AMRs either. The flexibility of AMRs also allows for continuous improvement and expanded use of robots over time, and you can deploy the same AMRs across multiple workflows, while with an AGV you’re stuck running just one. In other words, AGVs can be significant capital investments with a potentially longer payback period.
Your Edge Blog Team: What are the primary use cases for AMRs today? And are there any uses cases in which AMRs will be the only option because of AGV’s navigational or “training” limitations?
David: AGVs can still be suitable in some large-scale manufacturing plants where they are required to transport very heavy payloads, upwards of 2,000kg or 4,400lbs or more, like automotive chassis and heavy industrial parts, in a production line environment. Some AGVs cannot move in reverse, though. So, for applications where speed, flexibility, and multi-direction navigation are required, AGVs are not ideal.
AMRs, however, can be deployed in a variety of fulfillment, distribution, and manufacturing uses cases, and excel in applications in which velocity and worker collaboration are critical, such as e-commerce order picking. Smart AMRs can help increase associates’ pick productivity for each, case, and even pallet picking, while reducing the amount of unproductive walking time. We also see distribution operations deploying multiple AMR workflows within the same facility, such as combining automated put away, storage carousel picking and transport, and even automated removal of packaging and recyclable material all within the same building. For manufacturers, they can automate transport of raw materials to the line to keep production flowing smoothly and utilize AMRs for work-in-process movement as well. These use cases enable the assembly technicians to focus on their tasks and maintain or exceed output goals.
The content & opinions in this article are the author’s and do not necessarily represent the views of RoboticsTomorrow
Comments (0)
This post does not have any comments. Be the first to leave a comment below.
Featured Product
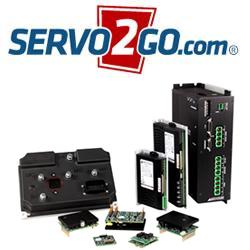