A 4pole design is stronger than a 2pole equivalent but can also fit within the same space and weight envelope. Greg Dutfield of maxon UK explains.
When to Choose a 4pole DC Motor
Article from | maxon group
Selecting a DC micromotor for use in applications from aerospace through to downhole drilling inspection, a 4pole motor has advantages. A 4pole design is stronger than a 2pole equivalent but can also fit within the same space and weight envelope. Greg Dutfield of maxon UK explains.
For DC motor applications that require high torque in a light weight and compact space envelope, 4pole motors can be the optimum choice. A 4pole motor can fit within the same footprint as a 2pole design but they are able to generate more torque. Importantly, a 4pole motor is also stronger than a 2pole motor of equivalent size, meaning that it more closely maintains its speed when a load is applied.
Pole count explained - speed
Pole count refers to the number of permanent magnet pairs within a motor. 2pole motors have a single pair of magnets in opposing north and south position. When current is applied, a magnetic field is created between the magnet pole pair, forcing the rotor to turn. Motor configurations also include 4pole, that includes two pole pairs of magnets, through to multi-pole designs that include up to 12poles.
Pole count is a significant aspect of motor design because it impacts the motor’s speed and torque characteristics. The lower the number of poles, the higher the motor’s speed. This is because each mechanical revolution of the rotor depends on the completion of the magnetic field cycle of each pole pair. The more permanent magnet pairs a motor has, the more magnetic field cycles that are required, meaning that it takes longer for the rotor to complete a 360° revolution. Speed is divided by the number of pole pairs at a fixed frequency, so taking a 10,000rpm 2pole motor as the basis, a 4pole motor would generate 5,000rpm, a six-pole motor would run at 3,300rpm, and so on.
Pole count explained - torque
Irrespective of pole count, a larger motor can generate more torque. But, comparing motors of the same volume, increasing the number of poles enables it to generate more torque. Taking a 4pole motor, its torque is greatly increased because its compact design features a thinner magnetic return path, enabling more space for a two-pair pole of permanent magnets and, in the case of maxon motors, a patented thicker knitted winding.
While a 4pole motor can fit within the same footprint as a 2pole design, it should be noted that further extending pole count, from six to 12 poles, means that frame size and mass must increase accordingly to accommodate the extra copper, iron, and magnets required.
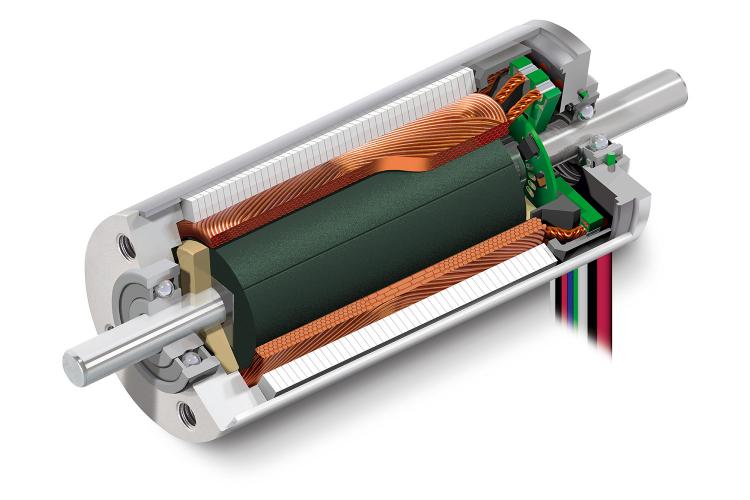
4pole motors are stronger
A motor’s strength is typically defined by its speed-torque gradient, which means that a stronger motor can more closely hold its speed when a load is applied. The speed-torque gradient is measured by the reduction in speed for each 1mNm load. A lower figure and shallower gradient means the closer a motor can maintain its speed under load.
A stronger motor is achieved thanks to the same design attributes that also help it reach higher torque, such as increased windings, and by using the optimum materials in their manufacture. For this reason, a 4pole motor design is stronger than a 2pole motor of the equivalent frame size.
For example, a 22mm maxon 4pole motor has a speed-torque gradient of 19.4rpm/mNm, meaning that for every 1mNm applied, it loses just 19.4rpm, whereas the same frame size 2pole maxon motor has a speed-torque gradient of 110rpm/mNm. Not all motor manufacturers match maxon’s design and materials specification, so the speed-torque gradient of an alternative brand 2pole motor might be higher, signifying a weaker motor.
When should you use a 4pole motor?
Applications across the aerospace industry benefit from the increased strength of a 4pole motor combined with low weight. These attributes are also necessary for hand-held power tools that often need more torque than a 2pole motor can provide, yet still retaining a low mass and small size design.
4pole motor characteristics are also important for manufacturers of mobile robots. Whether inspecting oil & gas pipelines or searching for trapped earthquake victims, wheeled or tracked robots need to negotiate rough terrain, obstacles, and steep inclines. 4pole motors provide the torque and strength necessary to overcome these loads, while helping mobile robot manufacturers achieve a compact, lightweight design.
Small size combined with a low speed-torque gradient is also vital for downhole drilling inspection within the oil & gas sector. For this application, a compact 2pole motor wouldn’t be strong enough, while a multi-pole motor would be too large to fit the drill bit inspection space envelope, so maxon specifically designed a 32mm 4pole motor to fit.
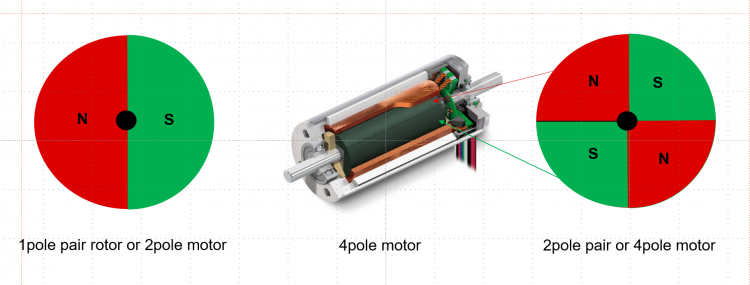
Optimising a 4pole motor
Many applications where a 4pole motor is suited take place in extreme environments or conditions, requiring the ability to operate under high temperature, pressure, and vibration. For example, motors in downhole drilling inspection might have to operate in temperatures above 200°C, while those installed in autonomous underwater vehicles (AUVs) are fitted in oil filled housings able to withstand the highest pressures at depths of up to 6,000m. Specifying additional design features such as sleeves as well as techniques to enhance heat dissipation, compact 4pole motors can handle extreme operating conditions long-term.
While motor specification is fundamental, in order to optimise an application, the design of the complete drive system should be considered, including gearboxes, encoders, drives and controls. As well as advising on motor specification, maxon’s engineers can engage with an OEM design team to develop a complete drive system specific to application requirements.
The content & opinions in this article are the author’s and do not necessarily represent the views of RoboticsTomorrow
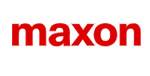
maxon group
maxon is a leading supplier of high-precision DC brush and brushless servo motors and drives. These motors range in size from 4 - 90 mm and are available up to 500 watts. We combine electric motors, gears and DC motor controls into high-precision, intelligent drive systems that can be custom-made to fit the specific needs of customer applications.
Other Articles
Multi-axis motion control drives pipe-based robots
Automate 2025 Q&A with maxon group
Understanding Torque and Speed in Electric Motors
More about maxon group
Comments (0)
This post does not have any comments. Be the first to leave a comment below.
Featured Product
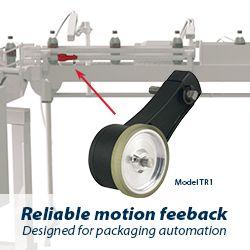