Standalone arms provide much greater flexibility in positioning compared to the conventional design, allowing multiple arms to be aligned in a plane much closer to parallel. To further approach the parallel ideal, the bulk of each arm must be minimized.
For Next-generation Surgical Robots, Minimize the Axial Length of Your Robotic Joints
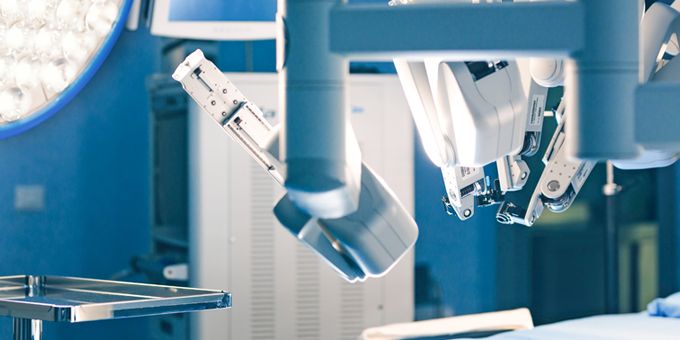
Article from | Kollmorgen
What if you could design and build a surgical robot that help doctors perform less invasive, more precise operations and achieve better patient outcomes? While the results of any surgery depend on the challenges of the specific case and the skill of the surgeon, better tools support better care. Here’s how next-generation motion engineering can help you develop the next generation of surgical robots.
Place the arms as close together as possible
Conventional surgical robots include large columns with multiple arms holding a tiny camera and various instruments such as scissors, graspers, needle holders, clip applicators and more. Depending on the surgery, the ideal procedure is performed through a single, small incision that must simultaneously accommodate the visualization camera and any needed instruments.
If you ask any surgeon, they will tell you that the ideal angle of approach for the camera and instruments into the incision site is as parallel and close together as possible—both to minimize trauma and to eliminate any discrepancy between the camera view and the angle at which each instrument operates.
Achieving an identical angle of approach is, of course, impossible, as the instruments can’t occupy the same space. Today’s instruments are very thin and compact, however. It’s the single-column, multiple-arm design of conventional surgical robots—plus the sheer bulk of their arm joints—that limits the angle of approach when multiple instruments are deployed. This is the principle challenge to overcome when designing the next generation of robots.
Minimize the axial length of arm joints
Standalone arms provide much greater flexibility in positioning compared to the conventional design, allowing multiple arms to be aligned in a plane much closer to parallel. To further approach the parallel ideal, the bulk of each arm must be minimized.
The limiting factor for how closely together the arms can operate is the axial length of the arm joints. You need a motor and gearing system that delivers all the required torque with the shortest possible axial length. Every millimeter saved without compromising performance helps surgeons work more effectively and creates an important market advantage for your surgical robot.
Start with the gearing
High-torque motors with short stack lengths are key to achieving optimum torque while minimizing axial length, total volume and weight. However, beyond the stack length of the motor itself, the gearing and feedback devices also need to be tightly integrated within the joint.
Ultimately, it’s the gearing that translates relatively high-speed motion of the motor into the lower speed and higher torque needed to move the load of the robotic arm at the optimum speed, precisely position it, and hold the load steadily in place. Because the selection of gearing also impacts the axial length of the joint, this is the place to start in creating your design.
The required speed, performance and load points will determine the appropriate gear set. No matter what ratio is required, this application calls for strain wave technology, also known as “harmonic” gearing.
Strain wave gearing provides three indispensable advantages. It enables the most compact axial integration within the joint. It offers relatively high gear ratios—typically ranging from a gear reduction of 30:1 to 320:1—to accelerate/decelerate loads smoothly and position them precisely. And it operates with zero backlash to minimize any unwanted movement that could potentially affect the precision of the procedure or induce unnecessary trauma.
Match the motor to the gearing and thermal requirements
Having specified the appropriate gear technology and ratio, you can select a motor based on the gear ratio, the speed at which the arm must run, and the mass it needs to hold. Thermal rise when operating at typical or maximum load can also be an important consideration, as excessive heat in the tight confines of the joint can damage gearing lubricant, encoder electronics and other components in close proximity. A motor that can deliver full performance at a lower thermal rise is desirable.
Take advantage of the D2L rule
As part of your motor specification process, you can further reduce axial length through an often-overlooked principle of motor design we refer to as the D2L rule.
In robotic joint design, the diameter of the motor is typically of minor concern. To enable robotic arms to operate as closely together as possible, you instead need to minimize the axial length. The D2L rule allows you to trade off a larger diameter for a significantly reduced axial length. Here’s how it works.
In the frameless motors used in robotic joints, torque increases or decreases in direct proportion to changes in motor length, but as the square of changes in the moment arm of the motor. In other words, under the D2L rule, doubling the moment arm—and thereby approximately doubling the overall diameter—produces a fourfold increase in torque.
Or, more relevant to surgical robot design, doubling the moment arm allows you to reduce the stack height by a factor of four while maintaining the same torque. This is a huge advantage when your design priority is to achieve the most compact axial length.
Optimize mechanical, electrical and thermal efficiency with TBM2G
For next-generation surgical robot performance, choose next-generation motors specially designed for robotic applications. Kollmorgen’s TBM2G frameless motors are engineered to address all the engineering challenges you face.
TBM2G motors deliver unprecedented mechanical, electrical and thermal efficiency in the most compact possible robotic joints. They are available in sizes under 1" in axial length—including end turns and PC boards—while delivering the motion industry’s highest torque density for their size. And they are designed to deliver all the performance you need with a significantly lower thermal rise, helping protect the integrity and performance of all the components in your robotic joint.
TBM2G motors are also optimized to work with readily available zero-backlash, high-ratio strain wave gear sets, with no customization or modification required. So you can accelerate your development time, count on a reliable production supply, and deliver surgical robots that allow doctors to operate instruments as close together and as close to parallel as possible.
Choose a partner who can help you succeed
One more benefit of using TBM2G motors is that they come with the expertise and support of an engineering partner that understands and can fulfill the unique requirements of surgical robot design and production.
Count on our self-service support options such as our online design tools, e-learning opportunities, knowledge base and the community of experts in the Kollmorgen Developer Network. And when you need one-on-one help, know that you can contact us anytime to chat online or over the phone with engineers who understand our products and your requirements inside and out—and who are dedicated to your success.
The content & opinions in this article are the author’s and do not necessarily represent the views of RoboticsTomorrow
Comments (0)
This post does not have any comments. Be the first to leave a comment below.
Featured Product
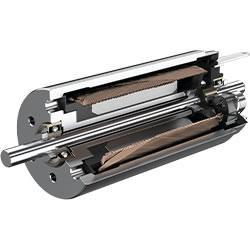