Machine tools are as much as 50 times stiffer than robotic arms. This lack of stiffness in robots makes it challenging to produce the desired performance. Minimizing chatter is a frequent concern and should not be overlooked to ensure the right results the first time.
How to Reduce Chatter in Robotic Milling Applications
Mark Fairchild | Precision Drive Systems
Have you optimized the performance of your robotic arm as it performs milling operations? Machining with articulated robot arms is an attractive alternative to machine tools because they offer ease of set-up, repeatability, a large workspace, and versatility. However, machine tools are as much as 50 times stiffer than robotic arms. This lack of stiffness in robots makes it challenging to produce the desired performance. Minimizing chatter is a frequent concern and should not be overlooked to ensure the right results the first time.
In this article, we explore some best practices for reducing chatter with a focus on the spindle and tooling.
The Crucial Importance of the Spindle
Many robotics integrators will choose the robot first and leave the choice of the spindle to later. "It should be the other way around," says Kenny Wilson, a Precision Drive Systems project engineer with more than 25 years of experience. A spindle with a standard set of bearings may not offer longevity in a milling application because of the radial loads to which the spindle is subjected.
Wilson goes on to explain:
"Choosing a standard spindle for milling can be deceiving because, in initial testing, the system may do the job. But then, at the customer's site, when put into the production environment, within six months or so, parts start to go out of tolerance, and the spindle can fail rather quickly. The customer is unhappy, and the integrator looks bad. They send the spindle to us for repair and want to know why this is happening."
If the material is hard and the feed rates are sufficiently high, the standard spindle will not be able to handle the loads. To achieve greater radial stiffness and resilience, a triplex or quad set of bearings in the spindle may be needed to more effectively withstand the physical demands.
"A quad set of bearings is often not something you can order from a catalog," remarked Wilson. "It often has to be custom built." He also pointed out a trade-off is involved because increasing the number of bearings to increase radial stiffness usually requires reducing the rotational speed of the spindle. That's because, with a larger number of bearings, the heat in the spindle increases.
Custom building of spindles is a service Precision Drive System offers.
To underscore the crucial impact of choosing the right spindle upfront, Wilson also commented that sometimes the integrator is stuck because adding bearings to a spindle increases its weight. And the integrator may have chosen a robot arm that can't handle the extra weight. This may happen after the integrator has supplied the customer with multiple robot arms. Therefore, the upgrade cost can be significant because of initial oversight.
At that point, the robot integrators may resign themselves to having a system in which the spindles routinely fail after six to nine months. They are forced to buy additional or spare spindles to swap in so they can maintain the uptime of the system. And the result is that the customer is unhappy with the increased and unexpected costs and likely dissatisfied with the uptime or reliability of their automation investment. This is clearly not the optimal way of designing a new system and is far from an operating best practice.
If the spindle had been properly considered first, then the robot that could handle that spindle would have been chosen, and such downstream issues would be avoided. Such a solution might have taken more time upfront, but everyone would be happier with the lower operating costs and greater longevity of the result. The design and products chosen would be optimized for the operating specifications of the customer application.
Tooling and Its Effect on Chatter
"Reducing the number of flutes on the end mill may reduce chatter," said Wilson. Shortening the length of the tooling and increasing the speed of the spindle can help. "It's all about feeds and speeds," he said. Sometimes cutting back on the feed rate can eliminate or minimize the chatter.
"Most customers know they need to use balanced tooling," remarked Wilson. Sometimes the key is to use tooling with a larger diameter. The interface is also a crucial factor. It must have a sufficient gripping force to do the job. Various interfaces are available, and choosing the right interface for the task is vitally important.
The Fixture Can Be the Key
"We've had cases where there was chatter, and it turned out it was the fixture," related Wilson. The workpiece was secured with a pneumatic gripper, and over time, dust and chips clogged things up. The result was the part itself was vibrating, and that was the cause of the chatter. By changing the nature of the fixture or making sure everything was cleaned out, and routinely maintained, the problem was solved.
Conclusion
Reducing chatter in robotic milling is both an art and a science. One must take a methodical approach to investigating the root causes or operating variables and limits, which could be a combination of factors. Choosing the right spindle for the job as part of the design process is critically important. It is often the single greatest factor in a successful project versus one that needs to be reworked – or worse, completely re-designed.
The content & opinions in this article are the author’s and do not necessarily represent the views of RoboticsTomorrow
Comments (0)
This post does not have any comments. Be the first to leave a comment below.
Featured Product
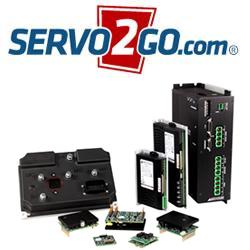