One application for which robot arms are well suited is using a kind of deburring tool as a cutting instrument when working with relatively soft materials like plastics and composites.
Ideal Spindles for High-Speed Robotic Milling of Plastics and Composites
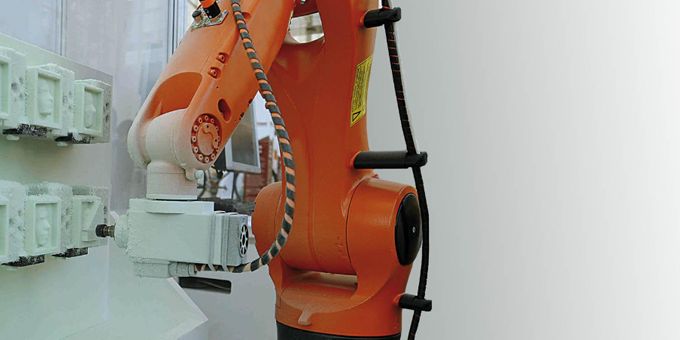
Mark Fairchild | Precision Drive Systems
Robot arms are finding their way into a wide variety of applications because of their precision, strength, and versatility. Robotic milling systems have become more common in recent years and have several advantages over traditional machine tools for certain applications. One application for which robot arms are well suited is using a kind of deburring tool as a cutting instrument when working with relatively soft materials like plastics and composites.
Industries That Use High-Speed Milling of Thin Composite Materials
An example of an industry that might need such a system would include boat builders. Recreational boats are comprised of fiberglass parts in the boat's interior that require many cutouts and have complex, molded shapes. Automotive dashboards and interiors, refrigerators, washing machines, shower stalls, and whirlpool hot tubs are all applications for this method of cutting and forming.
A six-axis, articulated robot arm can follow complex contours. Using a high-speed, rotating deburring bit, such a system is highly effective at cutting plastics and composite materials, even after the material has been molded into a complicated surface.
Is It Milling or Cutting?
Although the requirement is to cut through a sheet of molded plastic or fiberglass, it can be considered a milling application because the main forces applied to the spindle are perpendicular to the shaft of the tool. However, as we'll see below, this process is not so simple or straightforward.
Common Pitfalls in Choosing a Spindle For Such an Application
Kenny Wilson, an Engineering Manager at Precision Drive Systems with more than 25 years of experience, explains that because the material to be cut is thin - maybe only 90 thousands thick - some robotic integrators figure they can get away with a high-speed, small, and lightweight spindle. These would be spindles rotating at 24,000 to 44,000 rpm.
"And it can be misleading because when the integrator tries or tests it out, everything works and works well. Perhaps even for a while. ”Wilson commented further that the robotic integrator would often want to choose a smaller spindle because that also means they can specify a less powerful robot arm, making the whole system less expensive. However, the problem is that smaller spindles do not have the lateral stiffness that larger ones do, and their bearings cannot withstand the repeated radial forces to which the spindle is subjected.
Wilson describes what happens:
"The result is that the spindle will only last maybe three or four months, or six to eight months max. Then it fails, and they send it to us for repair. Unfortunately, we often find that the spindle has been destroyed."
Wilson related further that aside from the radial force, there is a "pulling" force to which the spindle is subjected. Because this application uses a deburring type of bit, the teeth in the bit engage the composite material in a way that pulls on the spindle shaft. Lighter-weight spindles are just not designed to handle that force repeatedly.
Often this only becomes evident after multiple systems have been installed. The customer becomes frustrated and dissatisfied because of the repeated downtime. The robotics integrator is then forced to buy spare spindles to swap in, to try to minimize the disruption to system uptime. Of course, this is not ideal, but there is a better way.
Making a Better Choice of Spindle
A better choice would be to go to the next family of spindles up in terms of weight and size of bearings. Such a choice may also mean the robotics integrator must choose the next more powerful class of robot arm. And this adds some increase to the initial cost of the system. Yet the overall cost of ownership will be less for the customer, and their uptime and satisfaction level will be far higher.
And, after all, the cost of dissatisfied customers can be very high indeed.
Conclusion
Design and specification engineering is often about making trade-offs. In a competitive situation, it is understandable that a robotics integrator will want to propose a system that will get the job done at the most affordable price point. Sometimes, however, a cheaper system will have ongoing negative consequences that far outweigh the initial savings.
Robotics integrators can take advantage of the insight and experience of spindle specialists like Precision Drive Systems. Choosing the right spindle for the job can make all the difference in uptime, throughput, finished product, and shop and customer satisfaction.
About Precision Drive Systems
Since 1996, PDS has been the global leader in providing new spindles, design and engineering, customer support, and repairs for spindle applications in fabricating metal, wood, plastics, stone, marble, glass, and robotics manufacturing industries. The PDS corporate office is located near Charlotte in Bessemer City, NC. European customers are provided local solutions by the PDS service facility in Herford, Germany, with affiliated offices located worldwide. For more information, visit www.SpindleRepair.com or call 704-922-1206.
The content & opinions in this article are the author’s and do not necessarily represent the views of RoboticsTomorrow
Comments (0)
This post does not have any comments. Be the first to leave a comment below.
Featured Product
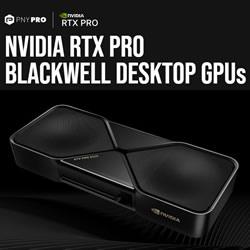