Automate 2025 Q&A with DESTACO
There's nothing like seeing our products in action. We will have live demonstrations, giving attendees the chance to see the performance and capabilities of our solutions up close and personal.
Automate 2025 Q&A with Zimmer Group
We have evolved from a manufacturer of single components to becoming a full-range provider of complex system solutions in the field of robotics. Our portfolio covers the entire automation spectrum - from high-functioning grippers to robot accessories.
Maximum process reliability for the protein source of the future
For more than 30 years, the SCHUNK PGN-plus-P gripper has been the most versatile gripper on the market, and is constantly finding new applications. A current and unusual application example is the use in the automated production of animal feed from insect larvae in Austria.
Longer tool service life, lower energy consumption
It has become essential for production companies to manufacture in a climate-friendly and economical way. With process-integrated measures, pollutant emissions and the use of resources must be kept as low as possible, while protecting and relieving the burden on employees.
DESTACO Smart Electric Product Line of Clamps and Guides
The new smart electric product line represents a substantial leap forward in the automation and industrial clamping landscape, offering enhanced precision, energy savings, and seamless integration for modern manufacturing processes.
Productivity Inc. Wants Your Robot to Do More
Using ATI's QC-11 Tool Changer and RCT-151 Radially-Compliant Deburring Tool along with a Renishaw probe, they produced a demonstration highlighting their expertise in aiding potential customers to maximize productivity of the robots already installed in their facilities
Ideal Spindles for High-Speed Robotic Milling of Plastics and Composites
One application for which robot arms are well suited is using a kind of deburring tool as a cutting instrument when working with relatively soft materials like plastics and composites.
Talking AUTOMATE 2023 with Stäubli
When you visit us at booth 2632, you will be able to experience a live demo of our robotic tool changer system, as well as our new end-of-arm-tooling solutions for material handling in automated manufacturing processes including gripping, suction, and cutting.
Intelligent Box Opening Device (IBOD)
You have lots of cartons coming into a typical warehouse, let's say 600 boxes per hour, and razor blades are used to cut these boxes while keeping up with intake speeds. This invites risks and employees still get injured, despite safety precautions.
End-of-Arm-Tooling powered by Stäubli Fluid Connectors
Stäubli Fluid Connectors presents a new End-of-Arm-Tooling range: The mechatronics specialist offers a broad technology portfolio from a single source coupled with advice for individual solutions in robotic material handling.
4 Critical Considerations When Selecting a Robotic End-Effector System
Finding and implementing the perfect end-effector system is reliant on the user giving due consideration to four critical areas. Only when complete understanding of the needs in these four realms is acquired can an educated end-effector choice be made.
HP Multi Jet Fusion 3D Printing Technology for End of Arm Tooling
When HP set out to develop this technology, the aim was to push beyond prototyping and enable repeatable, higher volume additive manufacturing. We can do this by combining a powder bed fusion approach with HP's Thermal Inkjet (TIJ) technology.
ArtiMinds and ATI Accelerate Technology Implementation with Greene Tweed
Choosing the right automation partners led Greene Tweed to quickly develop, integrate and install a more flexible automated material removal cell.
Metal 3DPrinting over CNC for custom EOAT
This small component was stopping them from realizing the full potential of their manufacturing process as they could only run the system when there was someone there to restart the system if a stoppage occurred due to slippage.
How Robotics is Transforming Manufacturing
When you sell a robot, the amount of additional required pneumatic components, sensing products, vision inspection systems and machine safety products can cost as much or more than the robot itself. Every robot sold has an exponential economic ripple effect.
Records 1 to 15 of 26
Featured Product
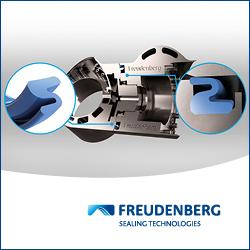
IP Seals for Robots
Freudenberg Sealing Technologies' IPRS (Ingress Protection Seals for Robots) provides reliable protection for robotic systems operating in harsh environments. Designed to prevent dust, moisture, chemicals, and wear from compromising performance, IPRS extends service life and reduces maintenance. The adaptive Z-shaped geometry ensures sealing integrity under continuous motion, making it ideal for high-speed automation and outdoor applications. Manufactured with high-performance elastomers such as Fluoroprene XP and EPDM, IPRS offers exceptional resistance to lubricants, cleaning agents, and extreme temperatures. This makes it the perfect solution for six-axis robots, SCARA robots, AMRs, AGVs, and cobots.
With its low-friction design and durable materials, IPRS enhances energy efficiency and operational reliability in industrial and autonomous robotics. Learn more about our IPRS Seals